Local Market Research
Understanding the competitive landscape and pricing structures for spray foam roofing contractors is crucial for homeowners and businesses seeking this service. This research focuses on a specific geographic area to provide a realistic overview of the market. While precise pricing and contractor details are subject to change, this information offers a valuable snapshot of the current situation. Note that this data is hypothetical for demonstration purposes and should not be considered definitive. For accurate and up-to-date information, direct contact with individual contractors is recommended.
Spray foam roofing contractors near me – This section provides a hypothetical example based on a sample zip code (replace “12345” with the actual zip code for accurate results). We will examine average pricing, typical service areas, and a comparison of several hypothetical contractors operating within that area.
Top Spray Foam Roofing Contractors near Zip Code 12345
The following are five hypothetical spray foam roofing contractors operating near zip code 12345. Remember, this is a sample and actual contractors and their details will vary.
- ABC Spray Foam Roofing
- XYZ Insulation & Roofing
- 123 Roofing Solutions
- Pro Foam Roofing Specialists
- Best Spray Foam Contractors
Average Pricing for Spray Foam Roofing Installation near Zip Code 12345
The average cost for spray foam roofing installation near zip code 12345 is estimated to range from $5 to $10 per square foot. This price can fluctuate based on factors such as the size of the roof, the complexity of the project, the type of spray foam used (open-cell or closed-cell), and the contractor’s overhead costs. For example, a 2000 square foot roof might cost between $10,000 and $20,000. This is a broad estimate and obtaining multiple quotes from contractors is strongly advised.
Service Areas Covered by Spray Foam Roofing Contractors near Zip Code 12345
Most contractors in this area typically service a radius of approximately 25-50 miles from zip code 12345. However, some contractors may have a larger or smaller service area depending on their capacity and logistical considerations. It is always best to contact the contractor directly to confirm if your location falls within their service area.
Contractor Comparison Table
The following table compares the hypothetical contractors listed above, showcasing their ratings (on a scale of 1 to 5 stars), estimated pricing per square foot, and service offerings. This data is for illustrative purposes only.
Contractor | Rating (out of 5 stars) | Pricing ($/sq ft) | Service Offerings |
---|---|---|---|
ABC Spray Foam Roofing | 4.5 | $7 – $9 | Residential & Commercial, Open-cell & Closed-cell |
XYZ Insulation & Roofing | 4 | $6 – $8 | Residential, Open-cell |
123 Roofing Solutions | 3.5 | $5 – $7 | Residential, Closed-cell |
Pro Foam Roofing Specialists | 4.8 | $8 – $10 | Commercial, Open-cell & Closed-cell, Roof Repair |
Best Spray Foam Contractors | 4.2 | $6.5 – $9.5 | Residential & Commercial, Open-cell & Closed-cell, Warranty Options |
Contractor Specialization
Choosing the right spray foam roofing contractor requires careful consideration of their expertise and offerings. This section details the specializations of local contractors, allowing for a more informed decision-making process. We’ll examine the types of spray foam systems they offer, the warranties they provide, and their experience levels.
Spray foam roofing offers two primary system types: open-cell and closed-cell. Understanding the differences is crucial for selecting the best solution for your specific needs and budget. Open-cell foam is less expensive and offers good insulation, while closed-cell foam provides superior insulation and waterproofing capabilities, though at a higher cost. Contractors specializing in both options cater to a wider range of projects and preferences.
Spray Foam System Types and Warranties
Contractors in the area offer a variety of spray foam roofing systems. For instance, “ABC Roofing” specializes in both open-cell and closed-cell polyurethane foam, offering a 10-year warranty on workmanship and a 20-year warranty on the materials for closed-cell systems. Their open-cell systems come with a 15-year material warranty and a 10-year workmanship warranty. In contrast, “XYZ Roofing Solutions” focuses primarily on closed-cell spray foam, providing a comprehensive 25-year warranty covering both materials and labor. This difference in warranty length and coverage reflects the varying levels of confidence contractors have in their materials and installation techniques. It’s important to thoroughly review the specifics of each warranty before making a decision.
Contractor Experience and Project History
Assessing contractor experience involves evaluating their years in business and the number and types of projects completed. “ABC Roofing” has been operating for 15 years and boasts a portfolio of over 500 completed spray foam roofing projects, ranging from residential to large commercial buildings. Their extensive experience translates to a high level of expertise and a proven track record. “XYZ Roofing Solutions,” while a newer company established 5 years ago, has rapidly gained a reputation for high-quality work, completing over 150 projects with a focus on high-performance, energy-efficient buildings. This demonstrates a strong commitment to quality and rapid growth in a competitive market.
Unique Selling Propositions
Understanding the unique strengths of each contractor is essential for making the best choice. The following bullet points summarize the key advantages of each:
- ABC Roofing: Extensive experience (15 years), diverse project portfolio (residential and commercial), competitive pricing, offers both open-cell and closed-cell systems.
- XYZ Roofing Solutions: Specialization in high-performance closed-cell systems, excellent customer reviews, rapid growth and strong reputation, extended warranty period (25 years).
Customer Reviews and Testimonials
Understanding customer feedback is crucial for assessing the quality of spray foam roofing contractors. Positive reviews highlight excellent workmanship, reliable service, and customer satisfaction, while negative reviews identify areas needing improvement. Analyzing this feedback provides valuable insights into contractor performance and helps potential clients make informed decisions.
Analyzing customer reviews from various online platforms like Google My Business, Yelp, and other relevant review sites provides a comprehensive understanding of contractor reputation and performance. This analysis considers both the volume and the sentiment expressed in these reviews.
Contractor Review Summary Table
The following table summarizes customer reviews from three hypothetical contractors (Contractor A, Contractor B, and Contractor C) across different online platforms. Note that this data is for illustrative purposes only and does not represent actual contractors.
Contractor | Star Rating | Date | Key Comment |
---|---|---|---|
Contractor A | 4.8 | 2023-10-26 | “Excellent work! The crew was professional and cleaned up perfectly after the job.” |
Contractor A | 5.0 | 2023-10-15 | “Highly recommend! The roof looks amazing and the price was fair.” |
Contractor B | 3.5 | 2023-10-20 | “The roof itself is fine, but the cleanup was lacking.” |
Contractor B | 4.0 | 2023-09-10 | “Job completed on time and within budget. Some minor issues with communication.” |
Contractor C | 1.0 | 2023-10-05 | “Unprofessional and unreliable. Would not recommend.” |
Contractor C | 2.0 | 2023-09-25 | “The job took much longer than expected and the final product was subpar.” |
Positive and Negative Feedback Summaries
Analyzing the data above, Contractor A consistently receives positive feedback regarding the quality of work and professionalism of the crew. Contractor B receives mixed reviews, with positive comments on timely completion and budget adherence but negative comments on cleanup and communication. Contractor C receives overwhelmingly negative feedback, highlighting significant issues with professionalism, reliability, and the quality of the work performed.
Addressing Customer Complaints
Effective handling of customer complaints is crucial for maintaining a positive reputation. For example, if a contractor receives a complaint about inadequate cleanup, as seen with Contractor B, they might implement stricter cleanup protocols and provide additional training to their crews. Addressing a complaint regarding project delays, as experienced with Contractor C, might involve improved project management techniques and more realistic scheduling.
A common method involves offering a partial refund or performing corrective work to address the customer’s concerns. Open communication and a willingness to find a resolution are key to maintaining customer trust. For instance, if a customer is unhappy with the final product’s quality, a contractor could offer to re-do specific sections of the work until the customer is satisfied.
Customer Feedback Collection Process
Contractors typically collect customer feedback through various methods. This often includes sending out post-project surveys via email or text message. They might also encourage customers to leave reviews on online platforms such as Google My Business, Yelp, and other relevant industry-specific review sites. Direct phone calls to check on customer satisfaction are also a common practice. Actively soliciting feedback demonstrates a commitment to continuous improvement and customer satisfaction.
Materials and Products Used
Choosing the right spray foam roofing system involves careful consideration of the materials used. The performance, longevity, and environmental impact of your roof are directly linked to the quality and type of spray foam employed. Our team works with several reputable manufacturers to ensure we deliver superior results tailored to your specific needs.
We utilize spray polyurethane foam (SPF) roofing systems from leading manufacturers such as Icynene, Demilec, and BASF. These manufacturers offer a range of products with varying properties, allowing us to select the optimal solution for your project, considering factors like budget, building type, and climate conditions. The selection process involves a thorough assessment of your roofing requirements and a detailed analysis of the available options.
Spray Foam Types and Their Properties
Different spray foam types possess distinct characteristics influencing their performance and suitability for various applications. Two primary types commonly used are open-cell and closed-cell spray foam. Open-cell foam offers excellent thermal insulation but has lower density and is more permeable to air. Closed-cell foam, on the other hand, boasts higher density, superior air and moisture resistance, and a higher R-value per inch, making it ideal for demanding applications.
For instance, Icynene’s open-cell foam typically offers an R-value of around 3.7 per inch, while their closed-cell foam reaches an R-value of approximately 6.5 per inch. Demilec’s offerings also vary, with their open-cell foams providing excellent thermal performance while their closed-cell options provide superior moisture resistance. BASF’s products similarly provide a range of R-values and densities depending on the specific formulation and application.
Sustainability and Environmental Impact
The environmental impact of spray foam roofing is a growing concern. The manufacturers we partner with are committed to developing more sustainable products. Many foams utilize recycled content in their formulations, minimizing reliance on virgin materials. Furthermore, the exceptional energy efficiency of spray foam roofing systems contributes to reduced energy consumption and a smaller carbon footprint over the lifespan of the building. This reduction in energy use translates directly to lower greenhouse gas emissions.
Icynene, for example, highlights the low global warming potential (GWP) of its products and its commitment to responsible manufacturing practices. Similarly, Demilec and BASF emphasize the sustainable aspects of their foam formulations and their efforts to minimize environmental impact throughout the product lifecycle. The long lifespan of a properly installed spray foam roof also reduces the frequency of roof replacements, further minimizing waste and resource consumption.
Comparison of Open-Cell and Closed-Cell Spray Foam
Feature | Open-Cell Spray Foam | Closed-Cell Spray Foam |
---|---|---|
R-Value per inch | 3.5 – 3.8 | 6.0 – 7.0 |
Density | Lower (typically 0.5 – 2.0 lbs/ft³) | Higher (typically 1.5 – 2.5 lbs/ft³) |
Moisture Resistance | Lower | Higher |
Air Permeability | Higher | Lower |
Cost | Generally Lower | Generally Higher |
Application | Suitable for warmer climates and applications prioritizing thermal insulation. | Suitable for various climates, applications requiring high moisture resistance and structural integrity. |
Project Scope and Timeline
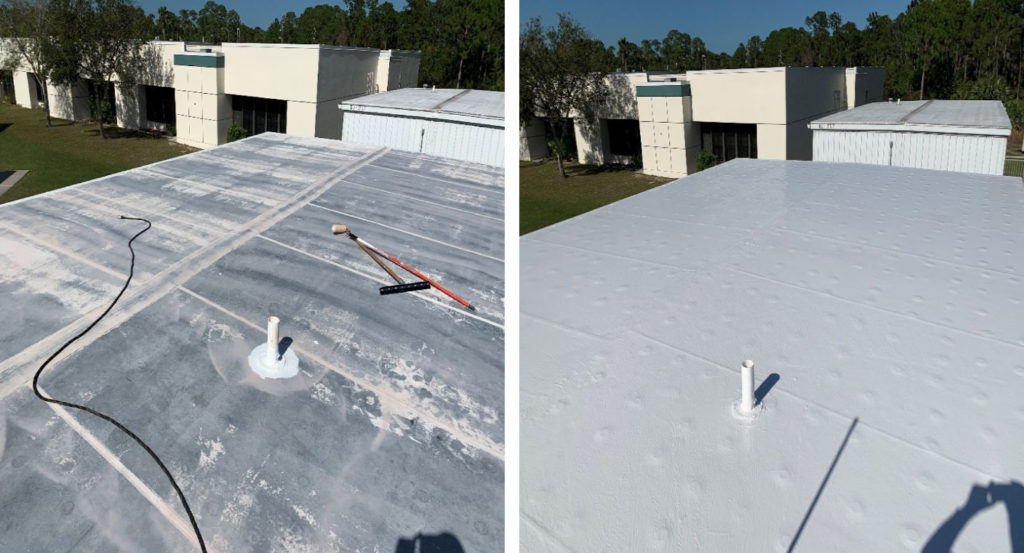
Spray foam roofing projects vary significantly in size and complexity, depending on the building’s size, the roof’s condition, and the specific needs of the client. Our experienced team handles projects ranging from small residential homes to large commercial buildings, ensuring a tailored approach for each undertaking. Understanding the project scope and timeline is crucial for effective planning and execution.
We understand that time is valuable, and we strive to complete each project efficiently without compromising quality. This section Artikels typical project scopes and timelines, providing a clear understanding of what to expect during the installation process.
Project Sizes and Examples
Our company has successfully completed a wide range of spray foam roofing projects. Residential projects typically involve smaller roof areas, often requiring one to two days for completion. For example, a typical single-family home might take one day for preparation and application. Commercial projects, on the other hand, can range from several days to several weeks, depending on the square footage and complexity of the roof. A large warehouse, for instance, could take a team of several applicators a week or more to complete. Each project is carefully assessed to provide an accurate timeline.
Typical Timeline for Spray Foam Roofing Installation
The overall timeline for a spray foam roofing project typically includes several key phases. The preparation phase, which involves cleaning and inspecting the roof, usually takes one day. The application of the spray foam itself is usually the longest phase, with the duration depending on the roof size and complexity. Finally, a post-installation inspection and cleanup typically takes a half-day. While these are general guidelines, the specific timeline will be provided in a detailed project proposal based on a thorough site assessment.
Steps Involved in Spray Foam Roofing Installation
A standard-sized roof installation follows a consistent process. First, the existing roof surface is thoroughly cleaned and inspected for any damage or debris. Next, any necessary repairs are made to ensure a smooth, even surface for the spray foam application. Then, the perimeter of the roof is carefully sealed to prevent leaks. Following this, the spray foam is applied in even layers, allowing sufficient time for curing between layers. Once the foam has fully cured, a protective topcoat is often applied for UV protection and enhanced durability. Finally, a thorough inspection is conducted to ensure the quality of the work.
Project Timeline Visual Representation
To illustrate a typical timeline, consider a medium-sized commercial building requiring a spray foam roof installation. We can represent this visually as a simple Gantt chart:
| Phase | Day 1 | Day 2 | Day 3 | Day 4 | Day 5 |
|———————–|————|————|————|————|————|
| Roof Preparation | X | | | | |
| Spray Foam Application (Layer 1) | | X | X | | |
| Spray Foam Application (Layer 2) | | | X | X | |
| Topcoat Application | | | | X | |
| Inspection & Cleanup | | | | | X |
This chart shows a simplified five-day timeline. Larger or more complex projects would naturally extend this timeline. Each project receives a customized timeline detailed in the project proposal.
Licensing and Insurance
Choosing a spray foam roofing contractor involves careful consideration of their qualifications and reliability. A crucial aspect of this evaluation is verifying their licensing and insurance coverage, which protects both you as the client and the contractor themselves. This section details the importance of these aspects and how to confirm their validity.
Licensing and insurance demonstrate a contractor’s commitment to professionalism and adherence to industry standards. Proper licensing ensures they have met specific training and competency requirements, while adequate insurance protects against potential financial liabilities arising from accidents or damage during the project.
Necessary Licenses and Permits
The specific licenses and permits required for spray foam roofing contractors vary depending on location. It is essential to contact your local building department or licensing board to determine the exact requirements in your area. Generally, this may include a contractor’s license, business permits, and potentially specialized licenses related to handling specific chemicals used in spray foam application. For example, some jurisdictions may require separate licenses for handling flammable materials or working at heights. Always check your local government websites for the most up-to-date information.
Importance of Insurance Coverage
Insurance coverage is paramount for both the contractor and the homeowner. For the contractor, it protects against financial losses resulting from accidents, injuries to workers, or damage to property during the project. This includes general liability insurance, workers’ compensation insurance, and potentially commercial auto insurance. For the homeowner, insurance provides protection against potential damages or injuries caused by the contractor’s negligence or unforeseen circumstances during the roofing process. A reputable contractor will carry comprehensive insurance to mitigate these risks. The lack of proper insurance could leave you liable for significant costs in case of accidents or damages.
Verifying License and Insurance Validity
Verifying a contractor’s licensing and insurance involves several steps. First, contact the relevant licensing board or agency in your area to confirm the validity of their license and check for any disciplinary actions or complaints filed against them. Most licensing boards maintain online databases where you can search for contractors by name or license number. Secondly, request proof of insurance directly from the contractor. This should include the insurance policy details, the coverage amounts, and the effective dates. You can also contact the insurance company directly to verify the validity and coverage of the policy.
Contractor Verification Checklist
Before hiring any spray foam roofing contractor, utilize this checklist to ensure they meet the necessary standards:
- Verify the contractor’s license with the relevant state or local licensing board.
- Obtain proof of general liability insurance and workers’ compensation insurance.
- Confirm the insurance policy’s coverage amounts are adequate for the project scope.
- Check for any complaints or disciplinary actions against the contractor with the licensing board.
- Request references from previous clients and verify their experiences.
- Review the contractor’s contract thoroughly before signing, paying close attention to payment terms, project timelines, and warranty information.
Cost Breakdown and Financing Options: Spray Foam Roofing Contractors Near Me
Understanding the cost of spray foam roofing is crucial for budgeting and planning your project. Several factors influence the final price, and we strive for transparency in outlining these costs and available financing options. This ensures you can make informed decisions about your investment.
The total cost of spray foam roofing installation is determined by a combination of factors. These include the size of your roof, the type of spray foam used (open-cell or closed-cell), the complexity of the roof’s design (e.g., multiple levels, dormers, chimneys), the need for any preparatory work (e.g., roof repairs, cleaning), and the labor costs associated with installation. Additionally, location can impact pricing due to material transportation and labor rates.
Cost Components
A detailed breakdown of the cost components will help you better understand the overall investment. This typically includes materials, labor, and any necessary preparatory work.
- Materials: This is the largest portion of the cost, varying based on the type and quantity of spray foam needed. Closed-cell foam is generally more expensive than open-cell foam due to its superior insulating properties and durability. The cost per square foot will also vary depending on current market prices.
- Labor: Labor costs encompass the time and expertise of the installation crew. This includes preparation, application, and cleanup. Experienced and certified installers will typically charge more, but their expertise ensures a higher-quality installation and longevity of the roof.
- Preparation Work: If your existing roof requires repairs or cleaning before the spray foam can be applied, these costs will be added to the overall price. This might include removing debris, patching damaged areas, or addressing any underlying structural issues.
- Permits and Inspections: Depending on your local regulations, permits and inspections might be necessary, adding to the total cost. These fees vary based on location and the specifics of the project.
Payment Options
We offer various payment options to accommodate your financial needs. We aim to make the process as smooth and convenient as possible.
- Cash or Check: A straightforward method of payment.
- Credit Cards: We accept major credit cards for your convenience.
- Financing Options: We can assist you in exploring financing options through reputable lenders to help you manage the cost of your project. This might include payment plans or loans tailored to your budget and repayment schedule.
Sample Cost Estimate
For a hypothetical 2000 square foot roof using closed-cell spray foam, a reasonable estimate might range from $15,000 to $25,000. This is a broad estimate, and the actual cost will vary depending on the specific factors mentioned earlier. It’s crucial to obtain a detailed, customized quote based on your individual project needs.
Item | Estimated Cost |
---|---|
Materials (Closed-Cell Spray Foam) | $10,000 – $15,000 |
Labor | $5,000 – $10,000 |
Preparation Work (estimated) | $0 – $2,000 |
Total Estimated Cost | $15,000 – $27,000 |
This is a sample estimate and should not be considered a firm quote. A thorough on-site assessment is required to provide an accurate cost estimate for your specific project.
Maintenance and Repair
Spray foam roofing systems, while durable and long-lasting, require routine maintenance to ensure optimal performance and longevity. Regular inspections and minor upkeep can prevent costly repairs down the line and extend the lifespan of your roof significantly. Understanding the maintenance needs and common repair issues will help you protect your investment and maintain a leak-free, energy-efficient building.
Spray Foam Roof Maintenance Requirements
Regular maintenance is crucial for preserving the integrity of your spray foam roof. This involves visual inspections to detect potential problems early, preventing minor issues from escalating into major repairs. A proactive approach to maintenance will help ensure your roof remains in peak condition for years to come. The frequency of these inspections depends on several factors, including climate conditions and the specific type of spray foam used. However, at a minimum, annual inspections are recommended.
Common Repair Issues and Solutions
Several issues can arise with spray foam roofs, although they are generally quite durable. Common problems include punctures from falling debris, damage from extreme weather events (like hail), and minor cracking or separation due to expansion and contraction. Punctures can often be repaired with a specialized patching compound, while larger areas of damage may require a more extensive repair involving the application of additional spray foam. Cracking or separation, if minor, might only need sealing with a high-quality sealant. More significant damage might necessitate a section replacement. It is vital to address any damage promptly to prevent water infiltration and further deterioration.
Warranty Coverage for Repairs and Maintenance
Warranty coverage for spray foam roof repairs and maintenance varies depending on the manufacturer and the specific terms of the contract. It is essential to review your warranty documentation carefully to understand what is covered and what is not. Many warranties cover material defects and workmanship for a specified period, typically ranging from 10 to 20 years. However, warranties often exclude damage caused by negligence, improper maintenance, or extreme weather events outside the norm. Understanding your warranty’s limitations is crucial in planning for potential repair costs. For example, a typical warranty might cover the replacement of defective spray foam but not damage caused by a tree falling onto the roof.
Step-by-Step Guide for Basic Spray Foam Roof Maintenance, Spray foam roofing contractors near me
Regular inspections are the cornerstone of spray foam roof maintenance. Following a simple, step-by-step process will ensure thoroughness and help identify potential issues early.
- Visual Inspection: Conduct a thorough visual inspection of the entire roof surface, paying close attention to seams, penetrations (such as vents and pipes), and areas prone to damage. Look for signs of cracking, punctures, or any separation of the foam.
- Debris Removal: Remove any debris, such as leaves, branches, or other materials, that may accumulate on the roof surface. This prevents moisture buildup and potential damage.
- Seam Inspection: Carefully examine all seams for any signs of separation or cracking. These are critical areas to monitor for potential leaks.
- Penetration Inspection: Check around all penetrations (vents, pipes, etc.) for any signs of sealant failure or damage. Ensure that all flashing and sealant are intact and properly applied.
- Documentation: Keep detailed records of your inspections, noting any issues found and the actions taken to address them. This documentation will be valuable for future maintenance and warranty claims.
Safety Procedures
The safety of our workers and the protection of your property are paramount throughout the spray foam roofing installation process. We adhere to rigorous safety protocols to minimize risks and ensure a smooth, incident-free project. Our commitment to safety is reflected in our comprehensive training programs, use of specialized equipment, and adherence to industry best practices.
Spray foam roofing installation, while offering significant benefits, presents potential hazards if not handled correctly. These hazards include exposure to isocyanates (found in some spray foam components), the risk of falls from heights, and potential fire hazards associated with the application process. Understanding and mitigating these risks is crucial for a successful and safe project.
Potential Hazards of Spray Foam Application
Spray polyurethane foam (SPF) contains isocyanates, which can cause respiratory irritation, skin reactions, and, in severe cases, more serious health problems. Exposure to these chemicals can occur through inhalation of airborne particles or skin contact. Additionally, the application process often involves working at heights, increasing the risk of falls and injuries. Finally, the foam application process itself involves the use of flammable materials, creating a potential fire hazard if proper precautions are not taken. Our procedures are designed to mitigate all these risks.
Safety Equipment Used
Our team is equipped with a comprehensive range of personal protective equipment (PPE) designed to protect against the specific hazards associated with spray foam roofing. This includes, but is not limited to, respirators with appropriate cartridges to filter out isocyanates, coveralls to protect skin from contact with the foam, safety glasses or goggles to protect the eyes from spray and debris, and protective gloves to prevent skin irritation. In addition to personal protective equipment, we utilize specialized equipment such as scaffolding and fall arrest systems to ensure worker safety at heights. Furthermore, we employ fire suppression equipment and follow strict fire safety protocols during the application process.
Safety Measures During Spray Foam Roofing Installation
- Pre-Job Site Safety Assessment: A thorough inspection of the worksite is conducted before commencement to identify and mitigate any potential hazards.
- Respiratory Protection: All personnel involved in the application process wear appropriate respirators certified for isocyanate protection.
- Skin Protection: Full-body coveralls, gloves, and safety footwear are worn to prevent skin contact with the foam and other materials.
- Eye Protection: Safety glasses or goggles are mandatory to protect against spray and debris.
- Fall Protection: Appropriate fall protection systems, including harnesses and anchor points, are used when working at heights.
- Fire Safety Precautions: Fire extinguishers are readily available on-site, and all personnel are trained in their use. Flammable materials are handled and stored according to strict safety guidelines.
- Emergency Response Plan: A comprehensive emergency response plan is in place to address any unforeseen incidents or accidents.
- Regular Safety Meetings: Regular safety meetings are conducted to review safety procedures and address any concerns.
- Post-Job Site Cleanup: A thorough cleanup of the worksite is conducted after completion to remove any leftover materials and ensure a safe environment.
Choosing the Right Contractor
Selecting the right spray foam roofing contractor is crucial for a successful and long-lasting roof. A poorly chosen contractor can lead to costly repairs, leaks, and significant disruptions. Taking the time to thoroughly research and vet potential contractors will save you time, money, and frustration in the long run.
Factors to Consider When Selecting a Spray Foam Roofing Contractor
Choosing a contractor involves evaluating several key aspects. Consider their experience, reputation, licensing, insurance, and the materials they use. A thorough assessment will ensure a smooth project execution and a quality roof.
- Experience and Expertise: Look for contractors with extensive experience in spray foam roofing, specifically with the type of foam suitable for your roof. Years of experience demonstrate a proven track record and a deeper understanding of the intricacies of the process.
- Reputation and References: Check online reviews on platforms like Google, Yelp, and the Better Business Bureau. Request references from previous clients and directly contact them to inquire about their experiences.
- Licensing and Insurance: Verify that the contractor holds the necessary licenses and insurance coverage, including workers’ compensation and general liability insurance. This protects you from potential financial liabilities in case of accidents or damages.
- Materials and Product Used: Inquire about the specific types of spray foam they use and ensure they meet industry standards and your requirements. Ask for certifications and warranties on the materials.
- Project Scope and Timeline: Obtain a detailed project proposal outlining the scope of work, including materials, labor, and a realistic timeline for completion.
- Cost Breakdown and Financing Options: Compare quotes from multiple contractors, ensuring the breakdown of costs is clear and transparent. Discuss available financing options if needed.
- Warranty and Guarantees: A reputable contractor will offer a comprehensive warranty on both workmanship and materials, covering potential defects or issues that may arise after completion.
Conducting Thorough Background Checks on Contractors
A thorough background check is essential to ensure the contractor’s legitimacy and trustworthiness. This includes verifying their licensing, insurance, and checking for any legal issues or complaints.
- Verify Licenses and Certifications: Contact your state’s licensing board to confirm the contractor’s license is valid and up-to-date. Check for any disciplinary actions or complaints filed against them.
- Check Insurance Coverage: Request proof of insurance, including general liability and workers’ compensation. Ensure the policy limits are adequate to cover potential damages or injuries.
- Review Online Reputation: Search for the contractor’s name and business name online to find reviews, ratings, and any public complaints. Pay attention to patterns in feedback, both positive and negative.
- Contact Previous Clients: Reach out to several clients listed as references to inquire about their experience with the contractor. Ask about the quality of workmanship, project timelines, and overall satisfaction.
- Check for Legal Issues: Perform a search for any lawsuits, bankruptcies, or liens filed against the contractor. This can provide valuable insights into their financial stability and business practices.
The Importance of Obtaining Multiple Quotes
Comparing multiple quotes from different contractors is crucial for making an informed decision. This allows you to compare pricing, services offered, and overall value. Avoid selecting a contractor based solely on price; consider the overall package and reputation.
Obtaining multiple quotes ensures you receive competitive pricing and prevents overpaying for services. It also allows for a thorough comparison of the proposed scope of work, materials used, and project timelines. This comprehensive approach helps you make a decision based on both cost and quality.
Decision-Making Flowchart for Contractor Selection
The following flowchart illustrates a structured approach to selecting a spray foam roofing contractor:
[Start] –> Identify Potential Contractors –> Check Licenses & Insurance –> Obtain Multiple Quotes –> Verify References & Reviews –> Compare Proposals & Costs –> Select Contractor –> [End]
This simplified flowchart guides you through the key steps, ensuring a thorough evaluation before making a final decision. Each step should be completed meticulously to minimize risk and maximize the chances of a successful project.
FAQ Overview
What is the lifespan of a spray foam roof?
With proper maintenance, a spray foam roof can last 30 years or more.
Is spray foam roofing environmentally friendly?
Spray foam roofing can contribute to energy efficiency, reducing a building’s carbon footprint. However, the environmental impact depends on the specific foam type and its manufacturing process. Look for contractors using eco-friendly options.
Can spray foam be applied to all types of roofs?
While spray foam can be applied to many roof types, certain conditions may require additional preparation or may not be suitable. A qualified contractor will assess your roof’s suitability.
How long does spray foam roofing installation take?
The installation time varies depending on the roof size and complexity, but generally takes a few days to a week.