Common Residential Flat Roof Problems
Flat roofs, while offering advantages like usable rooftop space and a sleek aesthetic, are susceptible to a variety of issues that can lead to costly repairs. Understanding the common causes of flat roof leaks and the signs of damage is crucial for proactive maintenance and preventing significant structural problems. This section details the most prevalent problems encountered with residential flat roofs.
Five Frequent Causes of Flat Roof Leaks
Several factors contribute to the majority of flat roof leaks in residential buildings. These factors often interact, exacerbating the damage. Understanding these root causes is key to effective repair and prevention.
- Poor Installation: Improper installation is a leading cause of leaks. This includes inadequate flashing around penetrations (such as chimneys, vents, and skylights), insufficient sealing of seams, and incorrect slope for proper water drainage. A poorly installed roof will be prone to leaks from the outset.
- Ponding Water: Flat roofs require a slight slope to facilitate water runoff. If the roof is not properly sloped or if debris blocks drains, water can pond on the surface. This prolonged exposure to water weakens the roofing membrane and underlying layers, eventually leading to leaks.
- Damaged Flashing: Flashing, the metal material used to seal around penetrations and edges, is crucial for preventing water ingress. Damage to flashing, caused by age, weathering, or improper installation, creates vulnerable points for leaks. Cracks and gaps in flashing are common entry points for water.
- Aging and Degradation of Roofing Membrane: All roofing materials degrade over time due to exposure to the elements. UV radiation, temperature fluctuations, and moisture cause the roofing membrane to become brittle, cracked, and porous, increasing its susceptibility to leaks. This is particularly true for older roofs that have not undergone regular maintenance.
- Root Intrusion: Roots from nearby trees or plants can penetrate the roofing membrane, causing significant damage and leaks. Roots can lift and crack the membrane, creating pathways for water to enter the building. This is a problem particularly prevalent with roofs that have vegetation growing close to their edges.
Typical Signs of Flat Roof Damage
Recognizing the signs of flat roof damage early on is crucial for preventing extensive and costly repairs. Damage can manifest visually or through functional issues impacting the building’s interior.
- Visible Cracks and Holes: Obvious cracks or holes in the roofing membrane are clear indicators of damage. These can be caused by aging, impact, or root intrusion.
- Blistering or Bubbles: Blisters or bubbles on the roof surface suggest moisture trapped beneath the roofing membrane. This can lead to further deterioration and eventual leaks.
- Sagging or Depressions: Sagging or depressions in the roof indicate structural problems or water damage that has weakened the underlying support structure.
- Water Stains on Ceilings or Walls: Water stains on interior ceilings or walls are a strong indication of a leak in the flat roof above. The location of the stain can help pinpoint the area of the roof requiring attention.
- Mold or Mildew Growth: Mold or mildew growth in the attic or on interior walls suggests prolonged water intrusion, potentially stemming from a flat roof leak. This is a serious issue that needs immediate attention.
Common Flat Roof Materials and Susceptibility to Damage
Different flat roofing materials have varying lifespans and susceptibilities to damage. Choosing the right material for your climate and budget is essential.
Material | Susceptibility to Damage | Lifespan (Years) |
---|---|---|
Built-up Roofing (BUR) | Moderate to High (susceptible to ponding water and UV degradation) | 15-20 |
Modified Bitumen | Moderate (more durable than BUR, but still susceptible to punctures and UV degradation) | 20-30 |
Single-Ply Membranes (TPO, EPDM, PVC) | Low to Moderate (highly durable, but can be damaged by punctures and extreme temperature fluctuations) | 20-30+ |
Repair Methods for Different Roof Materials
Flat roof repair techniques vary significantly depending on the roofing material used. Understanding the specific properties of each material is crucial for successful and long-lasting repairs. This section will compare and contrast repair methods for three common flat roofing materials: EPDM (ethylene propylene diene monomer), TPO (thermoplastic polyolefin), and built-up roofing (BUR). We will also provide step-by-step guidance for common repair scenarios.
Repair Techniques for EPDM, TPO, and Built-Up Roofing Systems
EPDM, TPO, and BUR systems each require different approaches to repair. EPDM, a rubber membrane, is often repaired using specialized adhesives and patches of the same material. TPO, a thermoplastic membrane, can be repaired using heat welding or adhesives, depending on the size and location of the damage. BUR, consisting of multiple layers of asphalt and felt, necessitates more involved repairs that often involve removing and replacing damaged sections. The choice of repair method depends heavily on the extent of the damage and the specific characteristics of the roofing system. For minor punctures, a simple patch might suffice, while larger tears or significant damage may require more extensive repairs, potentially involving the removal and replacement of damaged sections. Proper preparation of the surface is critical for all three materials to ensure a strong and lasting bond.
Patching a Small Puncture in a Single-Ply Membrane Roof
Repairing a small puncture in a single-ply membrane (such as EPDM or TPO) is a relatively straightforward process. This process assumes the underlying structure is not damaged.
- Clean the Area: Thoroughly clean the area surrounding the puncture, removing any debris, dirt, or loose material. Use a stiff brush and a suitable cleaning solvent recommended by the manufacturer of the roofing material. Allow the area to dry completely.
- Prepare the Patch: Cut a patch of roofing material slightly larger than the damaged area. For EPDM, a suitable adhesive will be necessary. For TPO, a heat welding tool might be used, depending on the type of TPO membrane and manufacturer’s recommendations.
- Apply Adhesive (EPDM): Apply a generous amount of the appropriate EPDM adhesive to both the patch and the surrounding area of the roof. Follow the manufacturer’s instructions carefully.
- Apply Heat (TPO): If using a TPO membrane and heat welding, carefully apply heat according to the manufacturer’s instructions. Ensure a proper seal is achieved.
- Apply Patch: Carefully press the patch onto the damaged area, ensuring complete contact. Use a roller to firmly adhere the patch and remove any air bubbles.
- Allow to Cure: Allow the adhesive to cure completely before applying any weight or traffic to the repaired area. The curing time will vary depending on the adhesive and environmental conditions.
Repairing Damaged Flashing Around Chimneys and Vents
Flashing is critical for preventing water penetration around roof penetrations. Damage to flashing requires prompt repair to avoid leaks. The repair process differs slightly depending on the roofing material.
Step | EPDM | TPO | Built-Up |
---|---|---|---|
1. Assessment and Preparation | Inspect the damaged area; clean and dry thoroughly. | Inspect the damaged area; clean and dry thoroughly. | Inspect the damaged area; carefully remove loose or damaged materials. |
2. Removal of Damaged Flashing | Carefully remove the damaged EPDM flashing, ensuring a clean edge. | Carefully remove the damaged TPO flashing, ensuring a clean edge. | Carefully remove the damaged built-up flashing, potentially involving removal of multiple layers. |
3. Surface Preparation | Clean and prime the surface for adhesion. | Clean and prime the surface for adhesion. | Clean and prime the surface, ensuring a stable base for new flashing. |
4. Installation of New Flashing | Apply appropriate adhesive and install new EPDM flashing, ensuring a watertight seal. | Use heat welding or adhesive to install new TPO flashing, ensuring a watertight seal. | Install new layers of felt and asphalt, carefully overlapping each layer to create a watertight seal. |
5. Final Inspection | Inspect the repair for any gaps or imperfections. | Inspect the repair for any gaps or imperfections. | Inspect the repair for any gaps or imperfections; ensure proper drainage. |
Assessing Roof Damage and Necessary Repairs
Accurately assessing the damage to a flat roof is crucial for planning effective and cost-efficient repairs. A thorough inspection, coupled with an understanding of the roof’s materials and the extent of the damage, will guide the selection of the appropriate repair method. Ignoring even minor issues can lead to more extensive and expensive problems down the line.
A systematic approach to inspection and repair planning ensures that the work is completed correctly and efficiently, preventing future leaks and structural damage. This section will Artikel the steps involved in this crucial process.
Flat Roof Inspection Checklist
A comprehensive inspection is essential to identify all areas requiring attention. This checklist provides a structured approach to ensure no damage is overlooked. Remember to prioritize safety; always use appropriate safety equipment when inspecting a roof.
- Overall Condition: Check for general signs of wear and tear, such as discoloration, sagging, or ponding water.
- Membrane Integrity: Examine the roofing membrane for cracks, punctures, blisters, or delamination. Pay close attention to seams and flashings.
- Drainage System: Inspect gutters, downspouts, and drains for clogs, damage, or proper functionality. Ensure that water flows freely away from the roof.
- Flashing: Carefully examine all flashing around chimneys, vents, skylights, and walls for any signs of rust, deterioration, or gaps.
- Insulation: If accessible, check the insulation for moisture damage or deterioration. Damp insulation is a significant indicator of a leak.
- Vegetation: Remove any vegetation growing on the roof, as it can damage the membrane and cause water retention.
- Structural Components: Check for any signs of structural damage to the roof deck, such as rot, warping, or pest infestation.
Determining the Appropriate Repair Method
The choice of repair method depends heavily on the type and extent of the damage identified during the inspection. This flowchart provides a visual guide to aid in decision-making. Remember that consulting with a qualified roofing professional is always recommended for complex repairs.
Tools and Equipment for Flat Roof Repairs
The specific tools required will vary depending on the type of repair. However, a basic toolkit should include the following items. Always ensure that tools are in good working order and that appropriate safety precautions are followed.
- Safety Equipment: Hard hat, safety harness, and fall protection system are crucial for working at heights.
- Measuring Tools: Measuring tape, level, and chalk line for accurate measurements and marking.
- Cutting Tools: Utility knife, tin snips, and possibly a circular saw for cutting roofing materials.
- Application Tools: Putty knife, trowel, roller, and brushes for applying sealants, adhesives, and coatings.
- Cleaning Tools: Broom, stiff brush, and pressure washer for cleaning the roof surface before repairs.
- Other Tools: Hammer, screwdriver, pliers, and a ladder (or scaffolding) for access.
Cost Estimation for Flat Roof Repairs
Accurately estimating the cost of flat roof repairs is crucial for budgeting and planning. Several factors significantly impact the final price, making it essential to understand these variables before beginning any project. A clear understanding will allow homeowners to make informed decisions and avoid unexpected expenses.
Factors Influencing Flat Roof Repair Costs
Several key factors influence the overall cost of residential flat roof repairs. These include the extent of the damage, the type of roofing material, labor costs in your region, the accessibility of the roof, and the need for specialized equipment or materials. For instance, a small leak repair will naturally cost less than a complete roof replacement. Similarly, repairing a TPO membrane will likely differ in cost from repairing a built-up roofing system (BUR). Accessibility also plays a role; a roof easily reached from ground level will be cheaper to repair than one requiring scaffolding or specialized equipment.
Cost Comparison of Different Repair Methods
The following table compares the approximate costs of various flat roof repair methods. These are estimates and can vary significantly depending on the factors mentioned previously. Always obtain multiple quotes from reputable contractors for accurate pricing specific to your situation.
Repair Method | Cost per Square Foot (USD) | Typical Scenario |
---|---|---|
Patching Minor Leaks | $2 – $10 | Small punctures, minor cracks |
Seam Repair | $5 – $20 | Repairing separated seams in single-ply membranes |
Partial Roof Replacement (Section) | $10 – $30 | Replacing damaged sections of the roof |
Full Roof Replacement | $15 – $50+ | Complete tear-off and installation of a new roofing system |
Cost Breakdown Examples for Various Repair Scenarios
To illustrate the cost variations, consider these examples:
Small Leak Repair: A small puncture in a TPO membrane might require only a patch and sealant. Labor costs might be around $100-$200, with materials costing approximately $50. The total cost would be in the range of $150-$250. This is a simplified example; actual costs will vary based on location and contractor.
Large Area Damage: Significant damage, such as extensive water damage or a large area of deteriorated membrane, will require more extensive repairs. This might involve removing and replacing a substantial section of the roof. A 200-square-foot repair could cost between $2,000 and $6,000, depending on the materials and labor involved. This scenario highlights the importance of prompt attention to roof damage to prevent escalating costs.
Preventative Maintenance for Flat Roofs
Regular maintenance is crucial for extending the lifespan of your flat roof and preventing costly repairs. Proactive care can significantly reduce the likelihood of leaks, structural damage, and premature deterioration. By implementing a preventative maintenance plan, you can ensure your roof remains in optimal condition for years to come, saving you both time and money.
Regular inspection and prompt attention to minor issues are key components of a successful preventative maintenance strategy. Neglecting small problems can often lead to more extensive and expensive repairs down the line. A well-maintained flat roof will not only protect your home but also contribute to its overall value.
Regular Maintenance Tasks
A comprehensive preventative maintenance program should include several key tasks performed on a regular schedule. These tasks are designed to identify potential problems early and address them before they escalate into major issues. Failing to perform these routine checks can lead to significant and costly damage.
- Annual Inspections: A thorough visual inspection should be conducted at least once a year, preferably in both spring and fall. This involves checking for signs of wear and tear, such as cracks, blisters, punctures, or loose seams. Pay close attention to areas around flashings, vents, and skylights, as these are common points of failure.
- Debris Removal: Regularly remove debris, such as leaves, branches, and dirt, from the roof surface. Accumulated debris can trap moisture, leading to ponding and damage to the roofing membrane. This is particularly important in areas with significant tree cover or heavy rainfall.
- Cleaning: Gently clean the roof surface with a soft brush and water to remove dirt, algae, and moss. Avoid using harsh chemicals, as these can damage the roofing material. For stubborn stains, consult a professional roofing contractor for appropriate cleaning methods.
- Seam Inspection and Repair: Pay close attention to the seams of the roofing membrane, as these are vulnerable to cracking and separation. Minor cracks can be repaired with appropriate sealant, while larger cracks may require professional attention.
Proper Roof Drainage Maintenance
Effective drainage is essential for preventing water damage to a flat roof. Properly functioning drainage systems prevent water from pooling on the roof surface, which can lead to leaks, structural damage, and premature aging of the roofing membrane. Regular maintenance of the drainage system is crucial to ensure its long-term efficiency.
- Gutter and Downspout Cleaning: Clean gutters and downspouts at least twice a year, removing leaves, debris, and other obstructions. Clogged gutters and downspouts can lead to water overflow and damage to the roof and surrounding areas. A clogged downspout may require specialized tools or professional assistance for clearing.
- Inspection of Drainage Slopes: Ensure that the roof has a proper slope to facilitate drainage. A flat roof should have a slight slope (typically 1/4 inch per foot) to prevent water from pooling. Any irregularities in the slope should be addressed by a qualified roofing professional.
- Drainage System Repair: Repair any cracks or damage to the drainage system promptly. Minor repairs can often be done with sealant, but significant damage may require professional replacement of damaged components.
Preventing Common Flat Roof Problems
Proactive maintenance can significantly reduce the occurrence of common flat roof problems. By addressing potential issues before they become major problems, you can save money and extend the life of your roof. Regular monitoring and preventative measures can significantly improve the longevity and performance of the roof system.
- Prevent Ponding Water: Regularly check for ponding water on the roof surface. Ponding water can cause significant damage to the roofing membrane. If ponding occurs, address the underlying drainage issues promptly.
- Address Leaks Immediately: Repair any leaks as soon as they are detected. Small leaks can quickly escalate into larger problems if left unattended. Early detection and repair can prevent extensive water damage and costly repairs.
- Protect from UV Exposure: UV exposure can degrade the roofing membrane over time. Consider using a reflective coating or other UV protection measures to extend the life of your roof. A reflective coating can significantly reduce the impact of UV radiation.
- Regularly Inspect Flashing: Flashing around chimneys, vents, and skylights is crucial for preventing leaks. Regularly inspect flashing for damage and repair or replace as needed. Proper flashing installation and maintenance are critical for preventing water penetration.
Choosing a Contractor for Flat Roof Repair
Selecting the right contractor is crucial for a successful and long-lasting flat roof repair. A poorly chosen contractor can lead to inadequate repairs, increased costs, and future problems. Careful consideration of several key factors will help ensure you find a reliable and competent professional.
Choosing a qualified and reputable contractor involves evaluating their experience, licensing, insurance, and customer reviews. Different types of contracts offer varying levels of protection and detail, and understanding these differences is vital to protecting your investment. Asking the right questions before committing to a contract is also essential to avoid potential misunderstandings and disputes.
Key Qualities of a Reliable Contractor
Finding a reliable contractor requires careful assessment of several key characteristics. These include verifiable experience in flat roof repair, appropriate licensing and insurance coverage, and positive customer feedback. A thorough vetting process helps mitigate risks and ensures a positive outcome. For example, a contractor with demonstrable experience in repairing roofs similar to yours, coupled with valid licensing and comprehensive insurance, significantly reduces the likelihood of encountering issues. Additionally, checking online reviews and testimonials from previous clients provides valuable insights into their work quality and customer service.
Comparison of Contractor Contract Types
Several types of contracts exist for flat roof repairs, each offering a different level of detail and protection. Fixed-price contracts specify a total cost upfront, while time-and-materials contracts charge based on labor and materials used. Cost-plus contracts add a percentage markup to the actual costs incurred. A fixed-price contract provides budget certainty, while a time-and-materials contract offers flexibility but potentially higher costs. A cost-plus contract may be necessary for complex projects with unforeseen challenges, but it requires careful monitoring to prevent cost overruns. The best contract type depends on the complexity of the repair and the client’s risk tolerance. For example, a simple repair might be suitable for a fixed-price contract, whereas a large-scale renovation might benefit from a time-and-materials or cost-plus approach.
Questions to Ask Potential Contractors
Before hiring a contractor, it is essential to gather comprehensive information to ensure a smooth and successful repair process. This includes verifying their experience, licensing, and insurance, as well as obtaining detailed quotes and understanding their warranty policies. Asking about their approach to the specific type of roof damage and materials used further enhances understanding and builds confidence in their capabilities. Clarifying the payment schedule and dispute resolution process protects your financial interests and provides clarity on the entire process. For instance, asking about their experience with your specific roof type (e.g., EPDM, TPO, built-up roofing) helps ensure they possess the necessary expertise. Inquiring about their process for handling unexpected issues and potential cost overruns provides a clear picture of their professionalism and transparency.
Understanding Warranties and Guarantees: Residential Flat Roof Repair
Warranties and guarantees are crucial aspects of any flat roof repair project, offering protection against faulty workmanship or materials. Understanding the different types available and the claims process can significantly impact your investment and peace of mind. This section details the various warranty types, the claims procedure, and the potential consequences of choosing a contractor without proper coverage.
Types of Warranties for Flat Roof Repairs and Materials
Several types of warranties may apply to flat roof repairs and materials. Manufacturers typically offer warranties on their products, covering defects in materials or manufacturing for a specified period. These are usually limited warranties, meaning they cover only specific defects and may require adherence to certain conditions, such as proper installation. Contractors, on the other hand, often provide workmanship warranties, covering their labor for a specific duration. These warranties ensure the repair work is performed to a certain standard and will last for a stated time. The duration and coverage of both manufacturer and workmanship warranties can vary significantly, ranging from a few years to several decades, depending on the materials used and the contractor’s reputation. Some contractors may offer combined warranties covering both materials and labor. It’s vital to carefully review the specific terms and conditions of each warranty before signing any contracts.
Filing a Warranty Claim for Faulty Workmanship or Materials
The process of filing a warranty claim generally begins with contacting the party responsible for the warranty – either the manufacturer or the contractor. It is crucial to document the problem thoroughly, including detailed photographs and descriptions of the damage, the date of the initial repair, and any relevant communication with the contractor or manufacturer. Most warranties require the claimant to provide written notification within a specified timeframe of discovering the defect. The warranty provider will then usually investigate the claim, possibly sending an inspector to assess the damage. If the claim is approved, the warranty provider will either repair the damage, replace the faulty materials, or provide financial compensation, depending on the terms of the warranty. Failure to comply with the warranty’s terms and conditions may result in the claim being denied. For example, if a manufacturer’s warranty specifies that proper maintenance is required, neglecting this could void the warranty.
Implications of Choosing a Contractor Without a Proper Warranty
Opting for a contractor without a proper warranty exposes homeowners to significant financial risks. If the repair work is substandard or the materials are defective, the homeowner bears the full cost of rectifying the problem. This can involve substantial expenses, potentially exceeding the initial repair cost. Without a warranty, the homeowner has limited recourse if the contractor is unwilling or unable to address the issue. Furthermore, the lack of a warranty can affect the resale value of the property. Potential buyers are less likely to purchase a home with known roof issues that lack warranty protection, potentially leading to a lower sale price. Therefore, selecting a reputable contractor with comprehensive warranties is a critical step in protecting your investment and ensuring long-term peace of mind.
Safety Precautions During Flat Roof Repair
Working on a flat roof presents unique safety challenges due to the height and the potential for falls. Proper safety measures are crucial to prevent accidents and ensure the well-being of those involved in the repair process. Ignoring safety protocols can lead to serious injuries or fatalities. This section details the necessary equipment and procedures for safe flat roof repair.
Necessary Safety Equipment for Flat Roof Repair, Residential flat roof repair
Appropriate safety equipment is paramount when working at heights. Failure to use this equipment can result in serious injury or death. The following list Artikels essential items:
- Fall Protection System: This includes a full-body harness, a strong anchor point securely attached to the roof structure (not to chimneys or skylights), and a lanyard or shock-absorbing lifeline to prevent falls. The anchor point must be capable of supporting at least 5,000 pounds.
- Safety Helmet: A hard hat protects against falling objects, such as tools or debris.
- Safety Shoes: Steel-toed boots with slip-resistant soles provide protection against punctures and slips on the roof surface.
- Gloves: Appropriate gloves should be worn to protect hands from cuts, abrasions, and chemical exposure, depending on the materials used in the repair.
- Eye Protection: Safety glasses or goggles protect eyes from debris and flying objects during the repair process.
- High-Visibility Clothing: Brightly colored clothing enhances visibility, especially when working in poor lighting conditions.
- Ladder or Scaffolding: Stable and properly secured access to the roof is essential. Ladders should be placed on a stable, level surface and extend at least three feet above the roofline. Scaffolding provides a safer and more stable working platform for extensive repairs.
Safety Procedures During Flat Roof Repair
Following established safety procedures significantly reduces the risk of accidents. A comprehensive safety plan should be developed and followed by all workers involved.
- Pre-Job Inspection: Thoroughly inspect the roof before starting any work to identify potential hazards such as weak areas, damaged sections, or obstacles.
- Proper Fall Protection: Always use a fall protection system that meets OSHA standards. Ensure the anchor point is securely attached and the system is correctly adjusted and inspected regularly.
- Safe Access and Egress: Use a stable ladder or scaffolding to access and leave the roof. Never jump or climb precariously.
- Secure Tools and Materials: Keep tools and materials securely fastened to prevent them from falling. Use tool lanyards to tether tools to the worker’s harness.
- Weather Conditions: Avoid working on the roof during inclement weather such as rain, snow, or high winds. Wet surfaces are extremely slippery and increase the risk of falls.
- Communication: Maintain clear communication between workers on the roof and those on the ground. Use a designated signal system if necessary.
- Emergency Plan: Establish a clear emergency plan in case of an accident, including procedures for contacting emergency services and providing first aid.
Potential Hazards and Mitigation Strategies
Flat roof repairs involve several potential hazards that need to be addressed proactively.
- Falls: The primary hazard is falls from height. Mitigation involves using appropriate fall protection equipment and adhering to safe work practices.
- Exposure to Hazardous Materials: Some roofing materials contain hazardous substances. Mitigation involves using appropriate personal protective equipment (PPE), following manufacturer’s instructions, and proper disposal of waste materials.
- Exposure to the Elements: Sun exposure, extreme temperatures, and inclement weather can pose risks. Mitigation includes scheduling work during cooler parts of the day, using sunscreen, and avoiding work during storms.
- Sharp Objects and Debris: Broken pieces of roofing materials can cause cuts and injuries. Mitigation includes wearing appropriate gloves and eye protection and carefully handling debris.
- Electrical Hazards: Working near electrical lines or equipment poses an electrical shock risk. Mitigation involves contacting utility companies to de-energize lines if necessary and maintaining a safe distance from energized equipment.
Legal and Regulatory Considerations
Repairing a flat roof, even on a residential property, involves navigating a legal and regulatory landscape designed to ensure safety and structural integrity. Understanding these requirements is crucial for homeowners and contractors alike to avoid potential problems and ensure the longevity and safety of the repaired roof. Ignoring these regulations can lead to significant financial penalties and legal repercussions.
Residential flat roof repair – Compliance with building codes and obtaining the necessary permits are paramount aspects of any flat roof repair project. These regulations vary by location, reflecting local climate conditions, building materials commonly used, and other regional factors. Failing to meet these requirements can result in unsafe repairs, structural damage, and potential liability issues.
Relevant Building Codes and Regulations
Building codes are legal requirements that dictate minimum standards for construction and maintenance, including roofing. These codes address aspects such as the type of materials permitted, the slope of the roof (even for flat roofs, a slight slope is usually required), the insulation requirements, and the overall structural integrity of the roof system. For example, the International Building Code (IBC) and local amendments provide comprehensive guidelines on roofing systems, specifying requirements for waterproofing membranes, flashing, and drainage. A homeowner should consult their local building department to ascertain the specific codes applicable to their property. These codes often mandate regular inspections and may specify the qualifications of individuals who can perform repairs.
Importance of Obtaining Necessary Permits
Before commencing any flat roof repairs, it is essential to obtain the necessary permits from the local building authority. Permit applications typically require detailed plans of the proposed repairs, including materials to be used and the scope of work. The local authority reviews these plans to ensure compliance with building codes and regulations. Obtaining a permit protects the homeowner from potential legal repercussions and demonstrates compliance with the law. Furthermore, a permit often provides a record of the work performed, which can be beneficial in the event of future disputes or insurance claims. Failure to obtain a permit can lead to fines, stop-work orders, and even legal action to force compliance.
Consequences of Non-Compliance with Building Codes
Non-compliance with building codes in flat roof repairs can have several serious consequences. These can include:
- Fines and Penalties: Building departments can impose substantial fines for violations, particularly for repeated or serious offenses.
- Stop-Work Orders: The building authority can issue a stop-work order, halting the repair project until compliance is achieved. This can lead to project delays and increased costs.
- Legal Action: In some cases, non-compliance can lead to legal action, potentially resulting in court orders to rectify the violations and further penalties.
- Insurance Issues: If damage occurs due to non-compliant repairs, insurance claims may be denied or significantly reduced.
- Structural Damage and Safety Hazards: Improper repairs can compromise the structural integrity of the roof, leading to leaks, collapses, and other safety hazards, potentially causing injury or property damage.
Environmental Impact of Flat Roof Repair Materials
Choosing materials for flat roof repair has significant environmental implications, impacting resource depletion, manufacturing processes, and end-of-life disposal. Understanding the lifecycle environmental impact of different roofing materials is crucial for making informed, sustainable choices. This section examines the environmental performance of common flat roofing materials and explores sustainable practices for repair and disposal.
The environmental impact of flat roofing materials varies considerably depending on their composition and manufacturing process. Factors to consider include energy consumption during production, embodied carbon (the total carbon emissions associated with a product’s entire lifecycle), the use of recycled content, and the material’s durability and longevity. Furthermore, the potential for material degradation and its impact on the surrounding environment must be considered.
Comparison of Environmental Impacts of Different Flat Roofing Materials
Several common flat roofing materials offer different environmental profiles. Modified bitumen membranes, for example, often utilize petroleum-based products, contributing to greenhouse gas emissions during manufacturing and transportation. Their longevity can offset this impact somewhat, but their end-of-life disposal presents challenges. In contrast, single-ply membranes like TPO (thermoplastic polyolefin) or EPDM (ethylene propylene diene monomer) often boast higher recycled content and lower embodied carbon compared to modified bitumen. However, their durability and the potential for UV degradation should also be considered. Finally, green roofing systems using vegetation and soil offer significant environmental benefits, reducing urban heat island effects, improving air quality, and managing stormwater runoff. However, their higher initial cost and specialized installation requirements must be factored into the overall assessment.
Sustainable Practices for Flat Roof Repair and Maintenance
Minimizing waste and extending the lifespan of existing roofing systems are key aspects of sustainable flat roof repair. This involves prioritizing repairs over complete replacements whenever feasible. Regular inspections and preventative maintenance can help identify and address minor issues before they escalate into major repairs, significantly extending the roof’s lifespan and reducing the need for material replacements. Selecting durable, long-lasting materials with high recycled content can further reduce the overall environmental impact. For example, choosing a TPO membrane with a significant percentage of recycled content can minimize the demand for virgin materials.
Disposal Methods for Old Roofing Materials
Responsible disposal of old roofing materials is critical for environmental protection. Many roofing materials contain hazardous substances, and improper disposal can contaminate soil and water resources. Local regulations dictate the appropriate disposal methods for different materials. Often, modified bitumen membranes require specialized disposal at licensed landfills, while some single-ply membranes may be recyclable. Checking with local waste management authorities is essential to ensure compliance with regulations and to explore recycling options. Furthermore, careful removal techniques can minimize material breakage and waste generation, contributing to a more environmentally responsible disposal process.
Long-Term Solutions for Flat Roof Issues
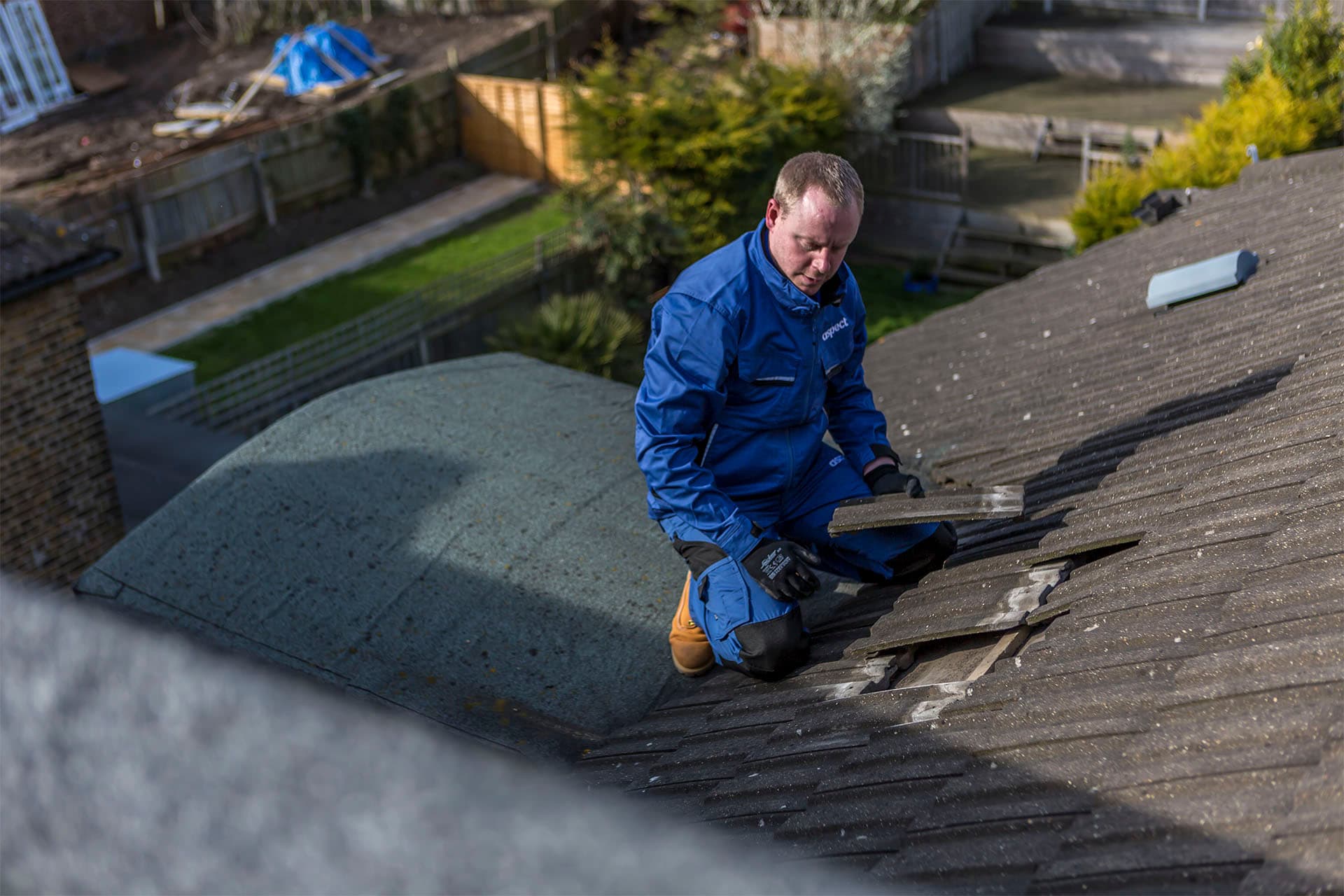
Addressing flat roof problems reactively, through repairs only when damage is evident, is costly and often leads to more extensive and expensive repairs in the future. A proactive approach, focusing on preventative maintenance and strategic long-term solutions, is significantly more beneficial in the long run, extending the lifespan of the roof and saving money. This section explores strategies for preventing future problems and Artikels examples of effective long-term solutions.
Proactive maintenance significantly reduces the likelihood of major flat roof repairs. Regular inspections, prompt addressing of minor issues, and employing durable materials contribute to a roof’s longevity. The cost savings from preventative measures far outweigh the expense of extensive repairs necessitated by neglect. For example, a small leak promptly repaired might cost a few hundred dollars, while ignoring it could lead to costly structural damage requiring thousands of dollars in repairs.
Preventative Maintenance Strategies
A comprehensive preventative maintenance program involves regular inspections (at least twice a year, more frequently in harsh climates), prompt cleaning of debris and vegetation, and timely repairs of minor damage like cracks or loose flashing. Regularly inspecting the roof for signs of ponding water, which can lead to premature wear, is crucial. Furthermore, ensuring proper drainage is vital. Clogged gutters and downspouts can lead to water accumulation, causing damage to the roof membrane.
Benefits of Proactive Maintenance Versus Reactive Repairs
Proactive maintenance offers several advantages over reactive repairs. It extends the lifespan of the roof, reducing the frequency of major repairs. It also minimizes the risk of costly water damage to the building’s interior. Finally, proactive maintenance provides peace of mind, knowing that the roof is well-maintained and less likely to fail unexpectedly. A building owner who proactively maintains their flat roof might spend a few hundred dollars annually on inspections and minor repairs, whereas a reactive approach could lead to tens of thousands of dollars in emergency repairs after a major storm causes significant damage.
Long-Term Solutions for Recurring Flat Roof Issues
Recurring issues, such as ponding water or consistent leaks in the same area, often indicate underlying problems requiring more than just surface-level repairs. These issues may necessitate a more comprehensive approach, potentially involving replacing sections of the roofing membrane, improving drainage systems, or even completely re-roofing the building. For example, a persistently leaking area might indicate a failure in the underlying insulation, requiring its replacement before a new membrane is applied. Similarly, inadequate slope can cause ponding water, necessitating the installation of a proper drainage system. Addressing these underlying causes ensures a long-term solution that prevents future problems.
FAQ Section
What is the average lifespan of a flat roof?
The lifespan of a flat roof varies depending on the material, climate, and maintenance, but generally ranges from 15 to 30 years.
How can I tell if my flat roof needs repair?
Signs include leaks, sagging, blistering, ponding water, and visible cracks or damage to the roofing membrane.
Can I repair my flat roof myself?
Minor repairs like patching small punctures are sometimes DIY-able, but larger repairs are best left to professionals for safety and warranty reasons.
What type of warranty should I expect from a contractor?
Look for warranties covering both materials and workmanship, ideally for a minimum of 5-10 years.