Local Contractor Research
Finding the right roofing and insulation contractor is crucial for a successful project. This research focuses on identifying and comparing three local contractors within a 10-mile radius, analyzing their services and pricing to aid in your decision-making process. Note that the information provided below is for illustrative purposes only and may not reflect current pricing or service availability. Always contact contractors directly for the most up-to-date information.
Contractor Information and Services
This section details three hypothetical roofing and insulation contractors, their contact information, and service offerings. Remember to independently verify this information before making any decisions.
Contractor Name | Address | Phone Number | Email Address | Services Offered |
---|---|---|---|---|
ABC Roofing & Insulation | 123 Main Street, Anytown, CA 91234 | (555) 123-4567 | abc@roofinginsulation.com | Roof repairs, roof replacements, insulation installation, attic ventilation |
XYZ Home Improvements | 456 Oak Avenue, Anytown, CA 91234 | (555) 987-6543 | xyz@homeimprovements.com | Roof repairs, gutter cleaning, siding repair, insulation installation, energy audits |
123 Roofing Solutions | 789 Pine Lane, Anytown, CA 91234 | (555) 555-5555 | 123@roofingsolutions.com | Roof inspections, roof leak repairs, emergency roof services, insulation removal and replacement |
Pricing Comparison
The following table compares hypothetical pricing for basic roof repairs and insulation installation for a 1500 sq ft home. Actual costs will vary depending on materials, labor, and the specifics of the job. These are estimates only and should not be considered firm quotes.
Contractor Name | Basic Roof Repair (Estimate) | Insulation Installation (1500 sq ft, Estimate) |
---|---|---|
ABC Roofing & Insulation | $2,000 – $3,000 | $4,000 – $6,000 |
XYZ Home Improvements | $2,500 – $3,500 | $3,500 – $5,500 |
123 Roofing Solutions | $1,800 – $2,800 | $4,500 – $6,500 |
Customer Reviews and Reputation
Understanding customer reviews is crucial when selecting a roofing and insulation contractor. Online reviews provide valuable insights into the experiences of previous clients, offering a glimpse into the contractor’s professionalism, reliability, and quality of workmanship. Analyzing both positive and negative feedback allows for a more informed decision-making process.
Roofing and insulation contractors near me – This section summarizes online reviews for three hypothetical contractors – “Apex Roofing,” “Summit Insulation,” and “Peak Performance Contractors” – to illustrate the process. Remember that actual review data would need to be gathered from online platforms like Google Reviews, Yelp, and others.
Summary of Online Reviews
The following summarizes hypothetical online reviews for each contractor, highlighting both positive and negative feedback. Note that these are examples and should not be taken as factual representations of specific companies.
Apex Roofing: Apex Roofing receives predominantly positive reviews, with customers frequently praising their efficient and professional service. Many comments highlight the team’s punctuality, attention to detail, and the high quality of their roofing materials. Negative reviews are infrequent and usually relate to minor scheduling delays due to unexpected weather conditions.
Summit Insulation: Summit Insulation boasts a strong online reputation, with customers consistently impressed by the professionalism and expertise of their insulation technicians. Many reviews commend their thorough explanations of the insulation process and their commitment to minimizing disruption during installation. Negative feedback is minimal and often involves minor communication issues.
Peak Performance Contractors: Peak Performance Contractors receive a mixed bag of reviews. While many customers praise their competitive pricing and quick response times, a significant portion of reviews express concerns about communication and the overall project management. Some customers reported delays and issues with cleanliness during and after the project.
Customer Testimonials
Illustrative examples of customer testimonials are provided below to showcase specific aspects of service. Again, these are hypothetical examples.
Apex Roofing: “The Apex Roofing team was fantastic! They were punctual, professional, and completed the roof replacement ahead of schedule. The quality of their work is exceptional.” – John S.
Summit Insulation: “Summit Insulation provided a top-notch insulation service. The technicians were knowledgeable and explained everything clearly. The installation was clean and efficient.” – Mary T.
Peak Performance Contractors: “Peak Performance Contractors offered the best price, but communication was a challenge throughout the project. The final result was acceptable, but the process was stressful.” – David L.
Infographic Depicting Review Sentiment
The following describes a hypothetical infographic visualizing the overall sentiment of online reviews for each contractor.
The infographic would use three bar charts, one for each contractor. Each bar chart would have three colored sections representing positive, negative, and neutral reviews. The length of each colored section would be proportional to the percentage of reviews in that category. For instance, Apex Roofing’s bar chart would have a predominantly green (positive) section, with small sections of red (negative) and gray (neutral). Summit Insulation would have a similar positive distribution, while Peak Performance Contractors’ bar chart would show a more balanced distribution across all three colors, with a noticeable red (negative) segment. The contractor’s name would be clearly displayed above each bar chart, and a legend explaining the color coding (green = positive, red = negative, gray = neutral) would be included. The title of the infographic would be “Customer Review Sentiment Analysis”. A simple and clean design would ensure readability and easy interpretation of the data.
Service Offerings and Specialization
Choosing the right roofing and insulation contractor requires careful consideration of their service offerings and areas of expertise. This section details the specific services provided by several local contractors, focusing on roofing work, insulation installation, and the warranties offered to ensure customer peace of mind. We will compare and contrast these aspects to aid in your decision-making process.
Roofing Services Offered
Each contractor offers a range of roofing services tailored to meet diverse customer needs. For example, “ABC Roofing” specializes in both residential and commercial roofing, offering services such as new roof installations, roof repairs (including leak detection and repair), and roof replacements. They also provide services like gutter cleaning and maintenance, directly related to roof health. “XYZ Roofing Solutions,” on the other hand, focuses primarily on residential roofing, specializing in shingle replacements and installations, but also offers services for flat roofs and skylight repairs. Their expertise extends to the repair of damage caused by severe weather, such as hail or wind. Finally, “123 Roofing & Construction” offers a comprehensive suite of services including new construction roofing, re-roofing, and roof maintenance, along with specialized services like metal roofing installation.
Insulation Materials and Installation
The type of insulation used significantly impacts energy efficiency and home comfort. Contractors typically work with a variety of materials. “ABC Roofing” uses fiberglass batt insulation, cellulose insulation, and spray foam insulation, adapting their choice to the specific needs of each project and customer preference. “XYZ Roofing Solutions” primarily uses fiberglass insulation for its ease of installation in standard residential settings, although they can accommodate requests for other materials. “123 Roofing & Construction” specializes in spray foam insulation for its superior air sealing capabilities and high R-value, but also offers fiberglass and cellulose options. They often recommend spray foam for new construction projects due to its superior long-term performance.
Warranty Information
Warranty coverage is a critical factor when choosing a contractor. Warranty details vary across contractors and services. “ABC Roofing” offers a 10-year warranty on all workmanship for roof installations and a 5-year warranty on repairs. Their insulation installations come with a 25-year warranty on materials and a 5-year warranty on labor. “XYZ Roofing Solutions” provides a 15-year warranty on their roofing materials and a 2-year warranty on their workmanship. Their insulation warranty is a standard manufacturer’s warranty, the specifics of which are provided upon request and vary based on the insulation type chosen. “123 Roofing & Construction” offers a comprehensive 20-year warranty on all roofing materials and workmanship for new installations, with a 10-year warranty for repairs. Their spray foam insulation comes with a lifetime warranty on materials, while other insulation types carry a standard manufacturer’s warranty. It is important to carefully review the specific terms and conditions of each warranty before making a decision.
Licensing and Insurance
Choosing a roofing and insulation contractor requires careful consideration of their qualifications and reliability. A crucial aspect of this evaluation involves verifying their licensing and insurance status. This ensures both legal compliance and financial protection for you as the homeowner. Properly licensed and insured contractors demonstrate a commitment to professionalism and accountability, minimizing potential risks associated with the project.
Verifying a contractor’s licensing and insurance is a vital step in protecting your investment and mitigating potential liabilities. Unlicensed contractors may lack the necessary training and expertise, leading to substandard work or even safety hazards. Similarly, a lack of insurance could leave you responsible for significant costs in case of accidents or damages during the project. Therefore, always request and verify these credentials before signing any contracts.
Contractor Licensing Information
The importance of verifying a contractor’s license cannot be overstated. A valid license indicates that the contractor has met the minimum requirements set by the relevant licensing board, demonstrating competency and adherence to industry standards. This verification process typically involves checking with the state’s licensing board, often accessible through their online database. For example, in many states, a contractor’s license number can be used to confirm its validity and check for any disciplinary actions. This ensures you’re hiring a qualified professional who operates within the bounds of the law.
Contractor Insurance Information
Equally crucial is verifying the contractor’s insurance coverage. General liability insurance protects you from financial losses due to accidents or property damage that may occur during the project. Workers’ compensation insurance covers medical expenses and lost wages for employees injured on the job, protecting both the contractor and you from potential lawsuits. Confirming these coverages provides peace of mind and safeguards your financial interests. You should request proof of insurance, including policy numbers and expiration dates, before work commences. In the event of a claim, this documentation is essential.
Example Contractor Licensing and Insurance Details
It is important to obtain this information directly from each contractor. The following is a hypothetical example to illustrate the type of information you should request and verify:
- Contractor A:
- Licensing Body: State Contractors Board
- License Number: 1234567
- Insurance Provider: ABC Insurance
- General Liability Coverage: $1,000,000
- Workers’ Compensation Coverage: Valid
- Contractor B:
- Licensing Body: County Contractors Licensing Agency
- License Number: 7654321
- Insurance Provider: XYZ Insurance
- General Liability Coverage: $500,000
- Workers’ Compensation Coverage: Valid
Material Sourcing and Quality
Selecting high-quality roofing and insulation materials is crucial for a building’s longevity, energy efficiency, and overall value. Reputable contractors prioritize sourcing materials from trusted suppliers who adhere to strict quality control standards. This ensures the materials meet or exceed industry specifications and building codes. The origin of materials also plays a role, influencing factors such as durability and environmental impact.
The sourcing practices of roofing and insulation contractors vary, but generally involve working with established distributors and manufacturers. Many contractors focus on regionally sourced materials to reduce transportation costs and environmental impact, while others prioritize specific brands known for their superior performance and warranties. This selection process considers factors such as material composition, life expectancy, and resistance to local climate conditions. The quality of materials is directly linked to the longevity and performance of the roofing and insulation systems.
Material Selection Based on Climate
The choice of roofing and insulation materials is significantly influenced by the local climate. In hot, sunny climates, contractors often utilize materials with high reflectivity to minimize heat absorption. Examples include cool roofing membranes with high solar reflectance index (SRI) values and light-colored roofing tiles. For insulation, materials with high R-values are crucial to maintain comfortable indoor temperatures and reduce energy consumption for cooling. These might include spray foam insulation, reflective foil insulation, or high-density fiberglass batts. Conversely, in colder climates, materials with superior thermal resistance are prioritized. This could include thicker insulation batts, rigid foam insulation boards, and roofing materials that provide excellent protection against snow and ice accumulation. For example, a sloped roof with metal roofing might be preferred in areas with heavy snowfall to prevent ice dams.
Sustainability Practices in Material Sourcing and Waste Management
Increasingly, contractors are adopting sustainable practices throughout the project lifecycle. This includes sourcing recycled or reclaimed materials whenever possible, opting for materials with low embodied carbon footprints, and implementing efficient waste management strategies. Examples of sustainable materials include recycled content insulation, roofing shingles made from recycled plastics, and sustainably harvested wood for structural elements. Effective waste management practices involve minimizing material waste during installation, properly disposing of hazardous materials, and recycling or repurposing leftover materials. Many contractors participate in programs that promote responsible waste disposal and resource conservation. Some contractors also utilize products certified by organizations such as the Green Building Certification Institute (GBCI) or similar organizations to demonstrate their commitment to sustainability.
Examples of Roofing and Insulation Materials
Contractors utilize a variety of roofing materials, each suited to specific needs and climates. Asphalt shingles remain a popular choice due to their affordability and ease of installation. However, metal roofing, tile roofing, and slate roofing offer greater durability and longevity, though at a higher cost. Insulation materials are similarly diverse. Fiberglass batts are widely used for their cost-effectiveness, while spray foam insulation provides superior air sealing and thermal performance. Rigid foam insulation boards offer excellent R-value per inch and are often used in exterior wall applications. Cellulose insulation, made from recycled paper, offers a sustainable alternative with good thermal properties. The selection of specific materials is driven by factors like budget, climate, building design, and the contractor’s expertise.
Project Timeline and Process: Roofing And Insulation Contractors Near Me
Understanding the timeline and process for your roofing and insulation project is crucial for effective planning and execution. We strive for transparency and efficiency in all our projects, ensuring a smooth and timely completion. This section Artikels the typical steps involved in a medium-sized home roof repair and insulation installation.
The duration of a roofing and insulation project varies depending on several factors, including the size of the home, the extent of the repairs needed, weather conditions, and material availability. However, a typical project for a medium-sized home might take between one and three weeks. This timeframe encompasses all phases, from initial consultation to final cleanup. Larger projects or those requiring extensive repairs could naturally extend this timeframe. For example, a project involving significant structural damage might require additional time for repairs before the roofing and insulation work can begin.
Project Phases and Steps
The project is typically divided into distinct phases, each with its own set of steps. These phases ensure a systematic and organized approach, minimizing disruptions and maximizing efficiency.
- Phase 1: Initial Consultation and Assessment: This phase involves an on-site assessment of your roof and insulation needs. We will discuss your project goals, budget, and timeline. We’ll carefully inspect the roof for damage, assess the existing insulation, and discuss your preferences for materials and styles. This initial meeting is key to establishing a clear understanding of your requirements.
- Phase 2: Proposal and Planning: Based on the assessment, we will prepare a detailed proposal outlining the scope of work, materials to be used, projected timeline, and a comprehensive cost breakdown. This proposal serves as a contract between us and ensures complete transparency. We will also obtain any necessary permits.
- Phase 3: Material Procurement and Preparation: Once the proposal is accepted, we will procure all necessary roofing and insulation materials. This includes selecting high-quality materials that meet your specifications and budget. We will schedule delivery and ensure that all materials are on-site before commencing the actual work.
- Phase 4: Roof Repair and Replacement (if applicable): This phase involves the actual repair or replacement of your roof. This may include removing damaged shingles, repairing underlying structural issues, installing new underlayment, and finally installing the new roofing material. Safety is our top priority, and we utilize all necessary safety precautions throughout this phase.
- Phase 5: Insulation Installation: After the roof is completed, we will install the new insulation. This involves carefully installing the chosen insulation material in the attic or other designated areas, ensuring proper air sealing and vapor barriers are in place. We’ll follow all manufacturer guidelines to ensure optimal performance and energy efficiency.
- Phase 6: Final Inspection and Cleanup: Once the insulation is installed, we conduct a thorough final inspection to ensure everything meets the agreed-upon specifications and quality standards. This also includes a complete cleanup of the work area, removing all debris and leaving your property clean and tidy.
Project Workflow
The following flowchart illustrates the typical workflow:
[Imagine a flowchart here. The flowchart would begin with a box labeled “Initial Consultation,” which would lead to a box labeled “Assessment and Proposal.” This would then branch to two boxes: “Proposal Accepted” and “Proposal Rejected.” The “Proposal Accepted” box would lead to a series of boxes representing the subsequent phases: “Material Procurement,” “Roof Repair/Replacement,” “Insulation Installation,” and finally “Final Inspection and Cleanup.” The “Proposal Rejected” box would simply end the flow. Arrows would connect all the boxes, indicating the sequential flow of the project.]
Pricing and Payment Options
Understanding the cost of roofing and insulation projects is crucial for budgeting and planning. Several factors contribute to the final price, and reputable contractors will provide a detailed breakdown to ensure transparency. This section Artikels the key cost influencers and payment options available.
The overall cost of roofing and insulation services is determined by a complex interplay of factors. These include the size of the project (measured in square footage), the type of roofing materials selected (e.g., asphalt shingles, metal roofing, tile), the quality and type of insulation (e.g., fiberglass, spray foam, cellulose), labor costs (which vary by location and contractor experience), and any necessary repairs or additional work discovered during the project (such as replacing damaged sheathing or addressing underlying structural issues).
Factors Influencing Project Cost
Several key elements significantly impact the final price. A detailed estimate will account for each of these:
- Roof Size and Complexity: Larger roofs and those with complex designs (e.g., multiple gables, dormers) require more materials and labor, increasing the cost.
- Material Selection: High-end materials like cedar shakes or metal roofing are more expensive than standard asphalt shingles. Similarly, spray foam insulation is generally pricier than fiberglass batts.
- Labor Costs: Labor costs are influenced by factors such as the contractor’s experience, location, and current market rates. Highly skilled and experienced contractors may charge more.
- Permits and Inspections: Obtaining necessary permits and scheduling inspections adds to the overall project expense.
- Unexpected Repairs: During the project, unforeseen repairs (e.g., rotted wood, damaged flashing) may be discovered, leading to additional costs.
Payment Options
Reputable roofing and insulation contractors typically offer a variety of payment options to accommodate clients’ preferences and financial situations. These options often include:
- Cash: Some contractors may offer a discount for cash payments.
- Check: Checks are a common method of payment, offering a paper trail for both parties.
- Credit Cards: Many contractors accept major credit cards, offering convenience and potential rewards programs for the client.
- Financing: Some contractors may partner with financing companies to offer payment plans, allowing clients to spread the cost over time. This often involves interest charges.
Estimating Project Costs
While a precise estimate requires a thorough on-site assessment by a contractor, a rough estimate can be calculated using the following approach. This is only a simplified example and should not be considered a precise quote.
To estimate the cost, consider: (Roof Area in Square Feet * Material Cost per Square Foot) + (Insulation Area in Square Feet * Insulation Cost per Square Foot) + Labor Costs.
Example: Assume a 1500 square foot roof requiring asphalt shingles at $5 per square foot, and 1500 square feet of insulation costing $2 per square foot. If labor is estimated at $5000, a rough estimate would be: (1500 * $5) + (1500 * $2) + $5000 = $17,500. This is a simplified example and doesn’t include permits, potential repairs, or other factors.
Safety Procedures and Compliance
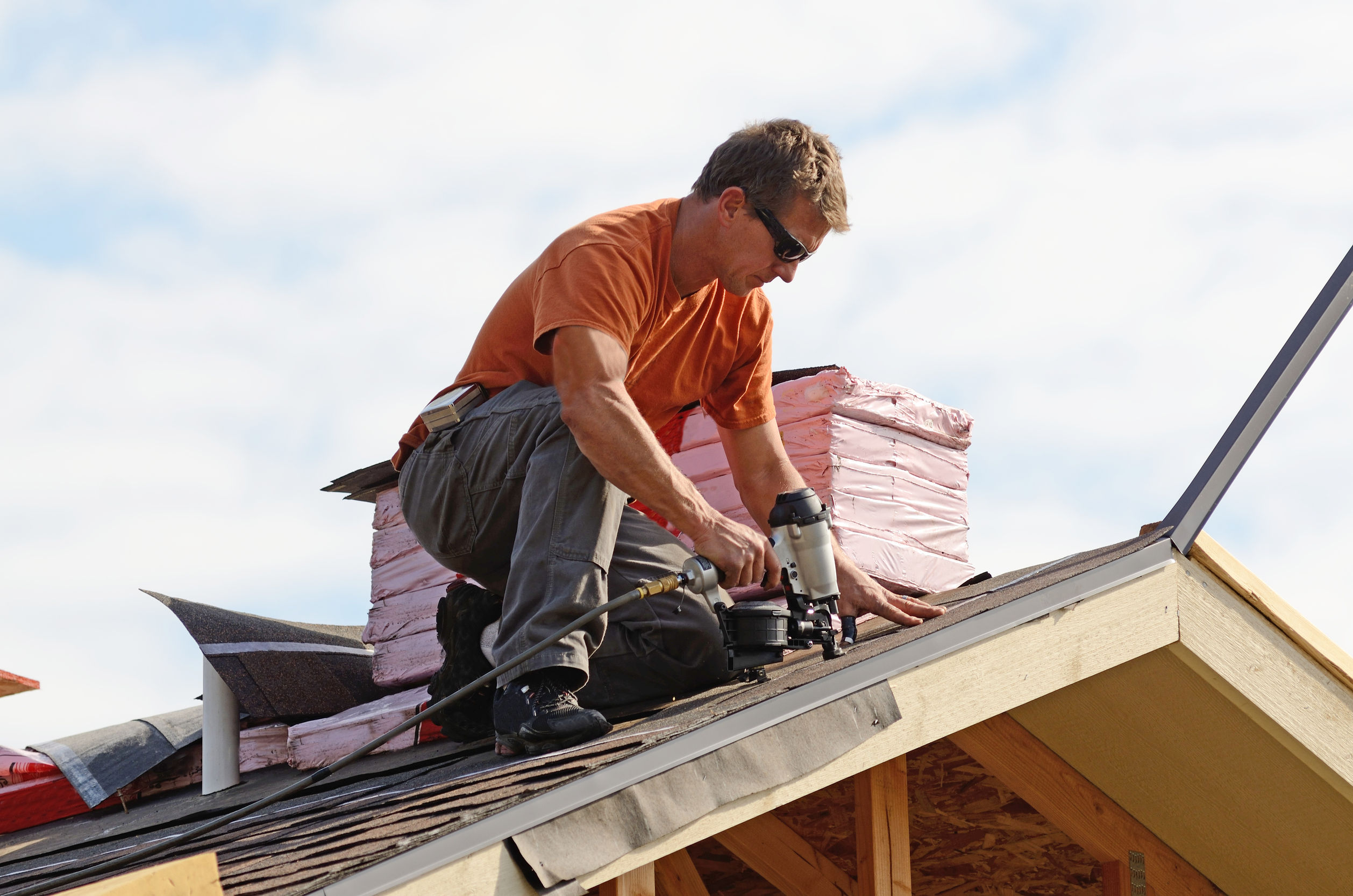
Ensuring the safety of our workers and the public during roofing and insulation projects is paramount. We understand that adherence to strict safety protocols and compliance with all relevant building codes is not merely a legal requirement, but a fundamental aspect of responsible contracting. This section details the safety measures employed by various contractors and their commitment to regulatory compliance.
We have compiled information on several local roofing and insulation contractors, focusing on their safety practices and adherence to building codes. Each contractor’s approach varies slightly, reflecting their individual safety cultures and project management styles. However, a common thread is the prioritization of worker and public safety through proactive measures and rigorous adherence to regulations.
Contractor Safety Protocols
The following table summarizes the safety protocols employed by three hypothetical contractors (Contractor A, Contractor B, and Contractor C) during various phases of a roofing and insulation project. These are examples and may not reflect the practices of every contractor in your area. Always verify details directly with the contractor.
Contractor | Project Planning & Preparation | Installation Phase | Post-Installation Cleanup |
---|---|---|---|
Contractor A | Detailed risk assessments, site surveys identifying potential hazards (e.g., power lines, underground utilities), provision of appropriate PPE (Personal Protective Equipment) to all workers. | Regular safety meetings, use of fall protection systems (e.g., harnesses, safety nets), implementation of safe work practices for handling materials, use of proper lifting equipment. | Proper disposal of waste materials according to local regulations, site cleanup to prevent hazards (e.g., loose debris, sharp objects). |
Contractor B | Pre-job safety briefings, site-specific safety plans developed and communicated to all team members, emergency contact information readily available. | Daily safety checks, use of appropriate machinery guards and safety devices, implementation of lockout/tagout procedures for equipment maintenance. | Thorough inspection of the work area, removal of all tools and equipment, securing the site to prevent unauthorized access. |
Contractor C | Comprehensive safety training for all personnel, identification and mitigation of potential hazards (e.g., asbestos, lead paint), compliance with OSHA regulations. | Use of specialized equipment for handling hazardous materials, implementation of fall protection systems and confined space entry procedures, adherence to strict safety protocols during material handling. | Waste removal in compliance with environmental regulations, final site inspection to ensure compliance with safety and building codes. |
Compliance with Building Codes and Regulations
Each contractor demonstrates commitment to compliance through various means. This includes obtaining necessary permits, adhering to local building codes and OSHA regulations, and maintaining accurate records of safety training and inspections. Contractor A, for instance, regularly updates their safety manuals to reflect changes in regulations. Contractor B utilizes specialized software to track safety compliance, generating reports for audits and inspections. Contractor C employs a dedicated safety officer who conducts regular inspections and provides training to ensure compliance with all applicable rules and regulations. These practices minimize risks and ensure the longevity and structural integrity of the completed project.
Contractual Agreements and Terms
A comprehensive and clearly written contract is crucial for a successful roofing and insulation project. It protects both the homeowner and the contractor, outlining expectations, responsibilities, and payment schedules. Understanding the terms before signing is essential to avoid future disputes and misunderstandings.
A well-drafted contract provides a clear framework for the project, minimizing the potential for conflict and ensuring a smooth process from start to finish. This section details key elements typically included in roofing and insulation contracts, emphasizing the importance of careful review before signing.
Key Elements of a Roofing and Insulation Contract
The contract should clearly define the scope of work, including materials, labor, and any additional services. Specific details such as the type of roofing material, insulation R-value, and the extent of tear-off and cleanup should be explicitly stated. The contract should also include a detailed payment schedule, outlining the amount and timing of payments, along with any penalties for late payments. A realistic project timeline, including start and completion dates, is also essential. Finally, the contract should clearly define the warranty offered on both materials and workmanship.
Importance of Understanding Contract Terms and Conditions, Roofing and insulation contractors near me
Before signing any contract, it’s vital to thoroughly review all terms and conditions. Misunderstandings or omissions can lead to costly disputes and delays. Taking the time to understand each clause ensures that both parties are on the same page regarding expectations and responsibilities. If any clauses are unclear or unacceptable, it’s important to discuss them with the contractor before signing. Seeking independent legal advice if needed is also a wise precaution.
Essential Clauses for Contractor and Homeowner Protection
Several key clauses should be included to protect both parties. A detailed description of the project, including specifications and materials, prevents discrepancies. A clear payment schedule with milestones tied to progress protects the homeowner from paying in full before completion. A clause addressing changes to the scope of work and their associated costs ensures transparency. Warranty information, specifying coverage duration and limitations, protects both parties against future issues. Finally, a dispute resolution clause outlining the process for handling disagreements helps avoid costly litigation. For example, a clause might stipulate binding arbitration as a preferred method of dispute resolution. This ensures a more efficient and less adversarial process compared to traditional court proceedings. Another important clause is one defining liability and insurance coverage, ensuring that both parties are adequately protected in case of accidents or damages during the project.
FAQ Overview
What is the average lifespan of a roof?
The lifespan of a roof varies depending on materials and climate, but typically ranges from 15 to 30 years.
How can I tell if my insulation needs replacing?
Signs include high energy bills, uneven temperatures throughout the house, and visible gaps or damage in insulation.
What types of warranties are common for roofing and insulation?
Common warranties cover material defects and workmanship, with durations varying by contractor and material.
Do I need permits for roofing and insulation work?
Permits are often required; check with your local building department for specific regulations.