Types of Insulation for Metal Building Roofs
Choosing the right insulation for your metal building roof is crucial for maintaining a comfortable interior temperature and reducing energy costs. Several factors influence this decision, including climate, budget, and the building’s intended use. This section will explore various insulation types, comparing their performance and installation methods.
Insulation Material Comparison
The selection of insulation material depends heavily on its R-value, cost, and ease of installation. The following table provides a comparison of common insulation types for metal building roofs. Remember that R-values can vary slightly depending on the manufacturer and thickness of the product.
Material | R-Value per inch | Pros | Cons |
---|---|---|---|
Spray Polyurethane Foam (SPF) | 6.0 – 7.0 | Excellent air sealing, high R-value, conforms to irregular surfaces, reduces thermal bridging | Higher initial cost, requires specialized equipment and trained installers, potential for VOC emissions (check for low-VOC options) |
Extruded Polystyrene (XPS) Foam Boards | 5.0 | High R-value, relatively inexpensive, easy to install, durable, resistant to moisture | Can be brittle, susceptible to damage during installation, may require additional vapor barrier |
Expanded Polystyrene (EPS) Foam Boards | 3.5 – 4.0 | Lightweight, inexpensive, easy to handle and install | Lower R-value than XPS, less durable, more susceptible to moisture damage |
Fiberglass Batt Insulation | 3.0 – 3.8 | Relatively inexpensive, readily available, good thermal performance | Lower R-value compared to foam insulation, requires careful installation to avoid gaps, can settle over time |
Mineral Wool Insulation | 3.0 – 4.0 | Good thermal and acoustic performance, fire-resistant, sustainable | More expensive than fiberglass, can be itchy to handle, requires careful installation |
Insulation Installation Methods
Proper installation is critical for maximizing the effectiveness of any insulation. Different materials require different techniques.
Insulation for metal building roof – The following Artikels the installation methods for three common types:
- Spray Polyurethane Foam (SPF): SPF is sprayed onto the roof deck, filling all gaps and cracks. Professional installation is essential due to the specialized equipment and safety precautions required. Proper preparation of the surface is crucial for optimal adhesion and performance.
- Rigid Foam Boards (XPS or EPS): These boards are typically installed directly onto the roof deck, overlapping seams and securing them with adhesive and fasteners. A vapor barrier may be necessary depending on the climate and building design. Careful attention should be paid to sealing all edges and gaps to prevent air leakage.
- Loose-Fill Insulation (e.g., cellulose or mineral wool): Loose-fill insulation is poured or blown into the cavity between the roof deck and the metal roofing. This method is effective for filling irregular spaces but requires careful attention to ensure even distribution and adequate depth.
Thermal Performance Comparison Visualization
A bar graph would effectively illustrate the thermal performance of various insulation types under different climate conditions. The horizontal axis would represent the insulation type (SPF, XPS, EPS, Fiberglass, Mineral Wool). The vertical axis would represent the R-value. Multiple bars for each insulation type could show performance in different climates (e.g., hot and dry, cold and humid). Higher bars would represent better thermal performance (higher R-value). Colors could be used to distinguish between climate conditions (e.g., red for hot and dry, blue for cold and humid). Data points would be derived from manufacturers’ specifications and relevant building codes. For example, a taller red bar for SPF compared to EPS would indicate that SPF performs better in hot and dry climates. A similar comparison could be made for other climates.
Factors Affecting Insulation Choice: Insulation For Metal Building Roof
Selecting the right insulation for a metal building roof involves careful consideration of several key factors. The optimal choice depends on a complex interplay of climate, building use, and long-term cost implications. Ignoring these factors can lead to reduced energy efficiency, increased maintenance costs, and ultimately, a less comfortable and less cost-effective building.
Climate’s Influence on Insulation Selection
Climate significantly impacts insulation needs. Regions with extreme temperature variations, whether hot summers or frigid winters, require higher R-values (a measure of thermal resistance) than those with moderate climates. High humidity areas necessitate insulation with good moisture resistance to prevent mold and mildew growth. For example, a metal building in Phoenix, Arizona, will require significantly more robust insulation than one in Seattle, Washington, due to the drastic difference in average temperatures and solar radiation. The choice might involve thicker insulation or a material with superior thermal performance in Arizona, while a focus on moisture control might be prioritized in Seattle’s damp climate. Coastal regions may require insulation with superior resistance to salt spray corrosion.
Insulation Choice Based on Building Use
The intended use of the building dictates the insulation requirements. A warehouse storing temperature-sensitive goods will need a higher level of insulation than a simple storage shed. Similarly, an office building requiring climate control for occupant comfort will necessitate a different insulation strategy than a workshop where temperature fluctuations are less critical. Residential applications often prioritize comfort and noise reduction, leading to different insulation choices compared to commercial spaces where energy efficiency might be the primary concern. For example, a cold storage facility would demand high R-value insulation to maintain consistently low temperatures, potentially using polyurethane foam, while a residential conversion might favor fiberglass batt insulation for its cost-effectiveness and ease of installation, coupled with additional soundproofing materials.
Long-Term Cost Savings and Insulation Options
While initial costs vary across insulation types, long-term savings associated with energy efficiency must be considered. High-performance insulation, although often more expensive upfront, significantly reduces heating and cooling costs over the building’s lifespan. This translates to substantial return on investment (ROI) over time. For instance, a building owner might choose spray polyurethane foam (SPF) insulation despite its higher initial cost due to its superior R-value and air-sealing capabilities, resulting in lower energy bills and reduced maintenance compared to less effective but cheaper options like mineral wool. Regular maintenance, such as inspecting for damage and addressing moisture issues, is crucial for extending the lifespan of any insulation and maximizing its cost-effectiveness. Neglecting maintenance can lead to premature failure, negating any long-term savings.
Installation Methods and Best Practices
Proper installation of rigid foam insulation on a metal roof is crucial for maximizing energy efficiency and the longevity of the building. This involves careful planning, attention to detail, and adherence to safety regulations. Incorrect installation can lead to reduced insulation effectiveness, increased energy costs, and potential structural damage.
Installing rigid foam insulation requires a methodical approach to ensure a seamless and effective thermal barrier. This section Artikels the steps involved, emphasizing best practices for preventing thermal bridging and air leaks, and highlighting the importance of safety.
Rigid Foam Insulation Installation Steps
The following steps provide a guide for installing rigid foam insulation on a metal roof. Remember to always consult the manufacturer’s instructions for your specific product.
- Preparation: Begin by thoroughly cleaning the metal roof surface. Remove any debris, dirt, or loose materials that could interfere with adhesion. Ensure the roof surface is dry before proceeding. This step is vital for optimal bonding of the insulation.
- Measurement and Cutting: Accurately measure the areas to be insulated. Cut the rigid foam insulation boards to the required size using a sharp utility knife or a specialized foam cutting tool. Precise cutting minimizes waste and ensures a snug fit.
- Vapor Barrier Installation (if applicable): If a vapor barrier is required (depending on climate and building design), install it before applying the insulation. Overlap seams by at least 6 inches and seal them with appropriate tape. The vapor barrier should be installed smoothly to prevent wrinkles or gaps.
- Insulation Placement: Carefully position the rigid foam insulation boards onto the roof, ensuring a tight fit between each board. Stagger the seams of adjacent boards to avoid creating continuous lines that could compromise insulation performance. This helps minimize thermal bridging.
- Fastening: Secure the insulation boards to the metal roof using appropriate fasteners. The type of fastener will depend on the insulation thickness and the metal roof type. Avoid over-tightening, which could damage the insulation or the roof. The fasteners should be spaced according to manufacturer recommendations to prevent sagging.
- Sealant Application: Seal any gaps or seams between insulation boards with a compatible sealant. This prevents air infiltration and moisture penetration, ensuring the insulation’s effectiveness. A high-quality sealant is crucial for long-term performance.
- Final Inspection: Conduct a thorough inspection of the completed insulation installation to ensure there are no gaps, air leaks, or improperly secured boards. Addressing any issues promptly is essential for maintaining insulation integrity.
Best Practices for Preventing Thermal Bridging and Air Leaks
Thermal bridging and air leaks significantly reduce the effectiveness of insulation. These best practices minimize these issues.
To minimize thermal bridging, ensure continuous insulation coverage, avoiding gaps or breaks in the insulation layer. Use appropriately sized and spaced fasteners. Staggering the seams of insulation boards also helps reduce thermal bridging points. Properly sealing all gaps and seams with a high-quality sealant is essential to prevent air leaks. The use of closed-cell foam insulation minimizes thermal bridging compared to open-cell foam.
Safety Equipment and Procedures
Safety is paramount during insulation installation. Working at heights requires specific safety precautions.
Always use appropriate personal protective equipment (PPE), including hard hats, safety harnesses, and fall protection systems when working on a roof. Wear gloves to protect against cuts and skin irritation from the insulation material and fasteners. Eye protection is crucial to prevent debris from causing eye injuries. Follow all manufacturer instructions and local safety regulations. Ensure the work area is properly secured to prevent falls and accidents. If working with spray foam insulation, proper respiratory protection is crucial due to potential exposure to isocyanates.
Addressing Moisture and Condensation
Metal building roofs, due to their conductive nature, are susceptible to significant temperature fluctuations. These fluctuations, combined with variations in ambient humidity, create ideal conditions for moisture buildup and condensation. Proper insulation plays a crucial role in mitigating these risks, protecting the building structure and its contents from potential water damage and the resulting issues like mold growth and structural degradation. Understanding the interaction between insulation, vapor barriers, and moisture is essential for effective roof design and construction.
The formation of condensation on a metal roof is a complex process influenced by several factors, including the temperature difference between the inside and outside air, the relative humidity of the interior air, and the thermal properties of the roof assembly. When warm, humid interior air comes into contact with a colder roof surface (especially in winter or during periods of significant temperature change), the moisture in the air condenses, forming droplets. This can lead to water accumulation, potentially dripping into the building or causing damage to the insulation itself. Effective insulation reduces the temperature differential across the roof, minimizing the potential for condensation.
Vapor Barriers and Their Placement
Vapor barriers are designed to control the movement of moisture vapor through the building envelope. Their strategic placement within the insulation system is critical for preventing moisture from entering the insulation and potentially condensing within it. In most climates, the vapor barrier should be placed on the warm side of the insulation, meaning the side facing the heated interior of the building. This prevents moisture from the interior air from penetrating the insulation. Incorrect placement can lead to trapped moisture within the insulation, reducing its effectiveness and potentially causing damage. For example, placing a vapor barrier on the exterior side of the insulation in a cold climate could trap moisture from the outside air, leading to ice buildup and potential damage during freezing temperatures. In hot and humid climates, careful consideration is needed to balance the need for moisture control with the need for adequate ventilation to prevent overheating.
Moisture Handling Capabilities of Different Insulation Types
Different insulation types exhibit varying degrees of resistance to moisture. For instance, closed-cell spray polyurethane foam (SPF) has excellent moisture resistance due to its dense, impermeable structure. It acts as both an insulator and a vapor barrier, reducing the need for a separate vapor barrier in some cases. Open-cell SPF, while still a good insulator, is more permeable to moisture and typically requires a separate vapor barrier. Fiberglass batts, on the other hand, are relatively permeable and are more vulnerable to moisture damage; therefore, a vapor barrier is highly recommended with this type of insulation. Mineral wool insulation also requires a vapor barrier, although some types have slightly better moisture resistance than fiberglass. The choice of insulation should always consider the local climate and the building’s specific needs regarding moisture control. For example, in a consistently humid climate, a closed-cell spray foam insulation would be a preferable choice over fiberglass batts, which would be more suitable for drier climates with a well-placed vapor barrier.
Energy Efficiency and Cost Savings
Proper roof insulation in metal buildings offers significant long-term energy cost savings by reducing the amount of energy needed to heat and cool the structure. This translates to lower utility bills and a positive return on investment over the lifespan of the building. The level of savings depends on factors such as climate, building size, existing insulation, and the type of insulation chosen.
Investing in effective roof insulation is a strategic move towards enhanced energy efficiency and substantial cost reductions. The reduction in energy consumption directly translates to lower operational expenses, leading to a more financially sustainable building operation. This section will explore the quantifiable benefits through specific examples and demonstrate the financial return on investment.
Energy Consumption Comparison: Insulated vs. Uninsulated Roof
The following table illustrates a hypothetical comparison of energy consumption for a 5,000 square foot metal building in a region with moderate climate conditions (average annual temperature of 60°F) over a year. The figures are estimations based on average energy costs and typical energy consumption rates. Actual savings will vary depending on specific factors.
Energy Consumption | Uninsulated Roof (kWh) | Insulated Roof (kWh) | Difference (kWh) |
---|---|---|---|
Heating | 150,000 | 75,000 | 75,000 |
Cooling | 120,000 | 60,000 | 60,000 |
Total Annual Consumption | 270,000 | 135,000 | 135,000 |
Assuming an average electricity cost of $0.15 per kilowatt-hour (kWh), the annual savings with proper insulation would be $20,250 ($0.15/kWh * 135,000 kWh).
Payback Period for Insulation Investments, Insulation for metal building roof
The payback period for an insulation investment represents the time it takes for the energy savings to offset the initial cost of the insulation materials and installation. This period varies depending on several factors, including the type and thickness of insulation, the cost of installation labor, and energy prices.
Let’s consider two scenarios:
Scenario 1: A basic fiberglass insulation installation costing $10,000. With an annual energy saving of $20,250 (as calculated above), the payback period is approximately 6 months ($10,000 / $20,250). This scenario assumes high energy savings.
Scenario 2: A more expensive spray foam insulation installation costing $25,000. Assuming a slightly lower annual energy saving of $15,000 due to potentially higher initial costs, the payback period is approximately 1 year and 8 months ($25,000 / $15,000). This scenario shows a longer payback period but still represents a worthwhile investment over the building’s lifespan.
Note: These are simplified examples. A comprehensive cost-benefit analysis should consider factors such as insulation lifespan, potential changes in energy prices, and the building’s expected lifespan. Consulting with an energy efficiency expert is recommended for accurate projections.
Environmental Impact of Insulation Materials
Choosing insulation for a metal building roof involves considering not only its thermal performance and cost but also its environmental impact. The life cycle of insulation materials, from manufacturing to disposal, significantly contributes to a building’s overall carbon footprint. Understanding the embodied carbon and recyclability of different options is crucial for making sustainable choices.
The environmental impact of insulation is multifaceted, encompassing energy consumption during manufacturing, transportation, and installation, as well as the material’s end-of-life management. A comprehensive Life Cycle Assessment (LCA) considers all these stages to evaluate the overall environmental burden. Different insulation types exhibit varying levels of impact across these stages.
Embodied Carbon in Insulation Materials
Embodied carbon refers to the greenhouse gas emissions associated with the manufacturing, transportation, and installation of a building material. Different insulation materials have significantly different embodied carbon footprints. For example, extruded polystyrene (XPS) and expanded polystyrene (EPS) insulation generally have higher embodied carbon compared to mineral wool (rock wool or glass wool) due to their reliance on fossil fuels in their manufacturing process. Conversely, materials like cellulose insulation, made from recycled paper, typically have a lower embodied carbon footprint. The exact figures vary depending on the specific manufacturing processes and transportation distances involved. For instance, a study might show that the embodied carbon of XPS is approximately 50% higher than that of recycled cellulose insulation per unit of thermal performance. This emphasizes the importance of considering not just the material’s R-value, but also its associated emissions.
Recyclability and End-of-Life Management of Insulation
The recyclability of insulation materials plays a crucial role in minimizing their environmental impact. Some materials, such as certain types of mineral wool, are more readily recyclable than others, like some rigid foam insulations. The availability of recycling programs and infrastructure also influences the practical feasibility of recycling. For example, some regions have established programs for recycling glass wool, while others may lack the infrastructure for processing certain types of foam insulation. The end-of-life management of insulation that cannot be recycled often involves landfill disposal, contributing to waste generation and potentially leaching harmful substances into the environment. The selection of recyclable materials significantly reduces the environmental burden associated with waste disposal.
Life Cycle Assessment Comparison of Insulation Options
A comprehensive life cycle assessment (LCA) allows for a comparison of the total environmental impact of different insulation materials across their entire life cycle. Such assessments consider various factors, including resource depletion, energy consumption, greenhouse gas emissions, air and water pollution, and waste generation. While a precise numerical comparison requires specific data relevant to the manufacturing processes and regional contexts, general trends emerge from numerous LCA studies. These studies consistently indicate that materials with lower embodied carbon and higher recyclability, such as cellulose insulation and certain types of mineral wool, often exhibit a more favorable overall environmental profile compared to materials with high embodied carbon and limited recyclability, such as some expanded and extruded polystyrene insulations. The results of such studies provide valuable insights to inform sustainable building material selection.
Maintenance and Longevity of Insulation Systems
Proper maintenance significantly impacts the lifespan and effectiveness of roof insulation in metal buildings. Understanding the expected lifespan of various materials and implementing a regular inspection schedule are crucial for maximizing energy efficiency and minimizing long-term costs. Neglecting maintenance can lead to premature degradation, reduced thermal performance, and potentially costly repairs.
Expected Lifespan of Insulation Materials
The lifespan of roof insulation varies considerably depending on the material, installation quality, and environmental conditions. While manufacturers often provide estimates, these are under ideal circumstances. Actual lifespan can be shorter due to exposure to moisture, temperature fluctuations, and UV radiation. For instance, polyurethane foam, known for its high R-value and excellent insulating properties, typically boasts a lifespan exceeding 50 years when properly installed and protected from moisture. Fiberglass batt insulation, on the other hand, while more economical, generally has a shorter lifespan, ranging from 15 to 30 years, depending on its density and protection from the elements. Mineral wool insulation also falls within a similar range, its lifespan affected by factors like density and moisture exposure.
Inspection and Maintenance Guidelines
Regular inspection of roof insulation is essential for early detection of problems. A visual inspection should be performed at least annually, checking for signs of damage such as water staining, pest infestation, or compression. Areas prone to moisture accumulation, such as around penetrations or near the eaves, should receive particular attention. During inspections, look for signs of sagging, which can indicate compression or inadequate support. If any damage is detected, prompt repairs are crucial to prevent further deterioration and maintain the insulation’s effectiveness. For example, minor tears in fiberglass batts might be patched with appropriate sealant, while more significant damage may necessitate replacement of affected sections. Moisture intrusion is a major concern; if evidence of moisture is found, addressing the source of the leak is paramount before attempting repairs to the insulation. Professional assessment might be needed for extensive damage or complex situations. Documenting each inspection with photos or notes is beneficial for tracking the condition of the insulation over time.
Building Codes and Regulations
Metal building roof insulation is subject to a complex web of building codes and regulations that vary significantly by region, often influenced by local climate conditions and energy efficiency targets. These regulations are crucial for ensuring the safety, structural integrity, and energy performance of buildings, and non-compliance can lead to significant penalties. Understanding these codes is essential for both builders and building owners.
Building codes often dictate minimum insulation R-values required for roofs based on climate zone. For instance, areas with colder winters will necessitate higher R-values to minimize heat loss, while warmer climates may have less stringent requirements. Additionally, regulations may specify acceptable insulation materials, installation methods, and fire safety standards. These requirements can impact the overall project budget and timeline, as certain materials or installation techniques might be more expensive or time-consuming than others. Furthermore, local jurisdictions might have unique stipulations regarding moisture control, ventilation, and the use of specific materials to address local environmental concerns.
Relevant Building Codes and Their Impact
Building codes relevant to roof insulation are typically found within the International Building Code (IBC), International Energy Conservation Code (IECC), and local amendments. The IBC addresses structural requirements, including the load-bearing capacity of the roof system when insulation is added. The IECC focuses on energy efficiency, specifying minimum insulation R-values based on climate zone and building type. Local jurisdictions often adopt and amend these codes to reflect specific regional needs and priorities. For example, a coastal region might have stricter requirements regarding moisture resistance and wind uplift resistance, whereas a region prone to wildfires may have stricter fire-rated insulation requirements. These local amendments can significantly alter the choice of insulation material and installation methods. A builder working on a project must meticulously research and understand all applicable codes at both the national and local levels to ensure compliance. Failure to do so can result in project delays, costly modifications, and potential legal issues.
Examples of Regional Variations in Codes
Consider two hypothetical regions: Region A, a cold, northern climate, and Region B, a warm, southern climate. Region A’s building code might mandate a minimum R-value of R-49 for roof insulation, while Region B’s code might only require R-30. This difference reflects the varying needs for heat retention. Furthermore, Region A’s code might specify the use of certain high-performance insulation materials, such as closed-cell spray foam, to minimize air infiltration and maximize thermal performance. Region B, on the other hand, might allow for a wider range of materials, potentially including less expensive options like fiberglass batts, provided they meet the minimum R-value requirement and other relevant fire safety and moisture control standards. This illustrates how climate and regional priorities directly influence the selection and installation of insulation materials. Consultations with local building inspectors and thorough reviews of regional codes are vital to ensure project compliance.
Case Studies of Successful Insulation Projects
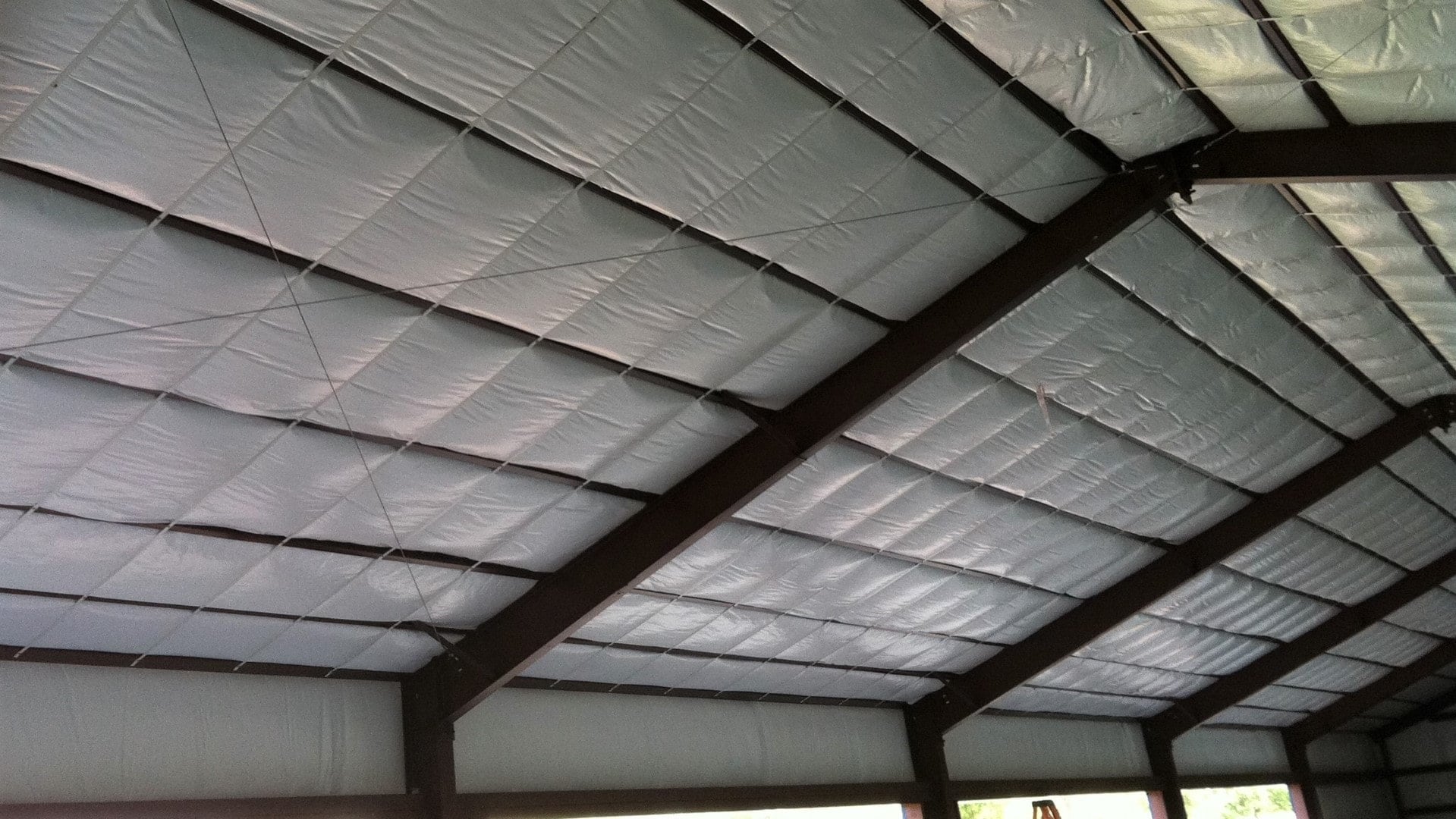
This section presents two case studies illustrating the successful implementation of metal building roof insulation projects. These examples highlight the challenges encountered, the solutions adopted, and the positive outcomes achieved in terms of energy efficiency, cost savings, and improved building performance. Both projects demonstrate the importance of careful planning, appropriate material selection, and skilled installation in optimizing insulation effectiveness.
Case Study 1: Cold Storage Facility Insulation Upgrade
This project involved a large cold storage facility with an existing metal roof exhibiting significant heat transfer. The facility experienced high energy costs due to inefficient insulation and frequent equipment malfunctions resulting from temperature fluctuations. The primary challenge was to upgrade the insulation without disrupting ongoing operations. The solution involved the installation of a closed-cell spray polyurethane foam (SPF) insulation system. SPF was chosen for its high R-value, excellent air-sealing capabilities, and ability to be applied directly to the existing roof deck without requiring significant disassembly. The installation was completed in phases to minimize operational disruption. The results were dramatic: energy consumption decreased by 35%, leading to substantial annual cost savings. Furthermore, temperature stability improved significantly, reducing equipment wear and tear and minimizing product spoilage. The improved insulation also contributed to a more comfortable working environment for employees.
Case Study 2: Manufacturing Plant Roof Retrofit
A manufacturing plant with a corrugated metal roof suffered from excessive heat gain during summer months, impacting worker productivity and increasing air conditioning costs. The existing insulation was outdated and insufficient. The primary challenge was to select an insulation that could withstand the high temperatures and potential for UV degradation while being cost-effective and easy to install. The solution implemented involved the installation of a high-performance fiberglass batts insulation system, combined with a reflective roof coating. Fiberglass batts were chosen for their thermal performance and cost-effectiveness, while the reflective coating further reduced solar heat gain. The installation was relatively straightforward, involving the placement of the batts between the purlins and the application of the coating over the insulation. The results showed a 20% reduction in cooling costs and a noticeable improvement in indoor comfort levels. The reflective coating also extended the lifespan of the roof by protecting it from UV damage.
Query Resolution
What is the best insulation for a cold climate?
High R-value insulation like spray foam or rigid foam boards are best suited for cold climates due to their superior thermal resistance.
How often should I inspect my roof insulation?
Regular inspections, ideally annually, are recommended to check for signs of damage, moisture, or settling.
Can I install roof insulation myself?
While possible for some types, professional installation is often recommended for optimal results and to ensure adherence to building codes.
What is the typical lifespan of roof insulation?
The lifespan varies depending on the material, but most insulation types last for 20-30 years with proper installation and maintenance.