Types of Conservatory Roof Insulation
Choosing the right insulation for your conservatory roof is crucial for maintaining a comfortable temperature year-round, reducing energy bills, and protecting your furniture and plants from damage. The effectiveness of insulation is largely determined by its thermal properties and material composition. Several options exist, each with its own advantages and disadvantages. This section details the key characteristics of popular conservatory roof insulation materials.
Comparison of Conservatory Roof Insulation Materials
The table below compares common insulation materials based on their thermal performance (R-value), cost, and overall pros and cons. R-value represents the material’s resistance to heat flow; a higher R-value indicates better insulation. Cost estimates are approximate and can vary based on supplier and quantity.
Material | R-Value (per inch) | Cost (per square meter, approximate) | Pros & Cons |
---|---|---|---|
Solid Foam (Polyurethane or Polyisocyanurate) | 5-7 | £20-£40 | Pros: High R-value, relatively inexpensive, easy to install. Cons: Can be susceptible to damage, less durable than some other options, potential for off-gassing of chemicals. |
Cellular Polycarbonate | 0.8-1.5 (depending on thickness and type) | £30-£60 | Pros: Lightweight, relatively inexpensive, allows for light transmission. Cons: Lower R-value compared to other options, can be less effective in extreme temperatures, may require additional insulation layers for optimal performance. |
Vacuum Insulated Panels (VIPs) | >10 | £80-£150 | Pros: Extremely high R-value, thin profile, excellent thermal performance. Cons: High cost, more complex installation, potential for damage during handling. |
Mineral Wool (Rock or Glass Wool) | 2.5-4 | £15-£30 | Pros: Good thermal performance, relatively inexpensive, environmentally friendly (some types). Cons: Can be bulky, requires additional vapor barrier, may require specialized installation. |
Thermal Properties and Heat Transfer Resistance
The effectiveness of insulation in preventing heat transfer is directly related to its R-value. Materials with higher R-values offer greater resistance to heat flow, leading to better temperature regulation within the conservatory. For example, vacuum insulated panels (VIPs), with their extremely low thermal conductivity, significantly reduce heat loss in winter and heat gain in summer compared to cellular polycarbonate, which has a considerably lower R-value. This difference in R-value translates to significant energy savings and improved comfort. The choice of material should consider the climate and the desired level of thermal performance.
Lifespan and Maintenance Requirements of Insulation Types
The lifespan and maintenance requirements of different insulation materials vary considerably. Regular maintenance, such as cleaning or minor repairs, can extend the lifespan of most insulation types.
Material | Lifespan (years) | Maintenance Requirements |
---|---|---|
Solid Foam | 20-30 | Minimal; occasional inspection for damage. |
Cellular Polycarbonate | 15-25 | Regular cleaning to remove dirt and debris; may require occasional replacement of damaged panels. |
Vacuum Insulated Panels | 25-50 | Minimal; avoid puncturing or damaging the panels. |
Mineral Wool | 20-30 | Regular inspection for moisture damage; replacement may be needed if moisture ingress occurs. |
Installation Methods and Techniques
Proper installation is crucial for maximizing the effectiveness of conservatory roof insulation. A poorly installed system will compromise its thermal performance, leading to energy waste and discomfort. The methods employed vary depending on the chosen insulation material, but the overarching goal remains the same: to create a continuous, airtight barrier that prevents heat transfer.
Best insulation for conservatory roof – The following sections detail the installation process for solid foam insulation and compare different approaches for various materials.
Solid Foam Insulation Installation
Solid foam boards, such as polyurethane or polyisocyanurate, offer excellent thermal performance and are relatively straightforward to install. Careful attention to detail during installation is key to ensuring a successful outcome. The following steps Artikel a typical installation process:
- Preparation: Thoroughly clean the roof structure, removing any debris or loose materials. Ensure the surface is dry and free from dust or contaminants that could affect adhesion.
- Measurement and Cutting: Accurately measure the areas to be insulated and cut the foam boards to size, allowing for a snug fit. Use a sharp utility knife or specialized foam cutting tool for clean cuts to minimize waste and ensure proper fitting.
- Adhesive Application: Apply a high-quality adhesive specifically designed for foam insulation to the back of the boards. Follow the manufacturer’s instructions regarding application rate and drying time. Ensure even coverage to promote strong bonding.
- Board Placement: Carefully position the foam boards onto the roof structure, pressing firmly to ensure complete adhesion. Start from one edge and work your way across, maintaining consistent pressure to avoid air gaps.
- Securing (Optional): For added security, especially in areas exposed to high winds or potential movement, mechanical fasteners such as screws or nails can be used to secure the boards. Ensure fasteners are appropriate for the foam type and roof structure.
- Joint Sealing: Seal all joints and gaps between the foam boards using a compatible sealant. This is crucial for creating an airtight barrier and preventing thermal bridging. A closed-cell spray foam is often used for this purpose due to its excellent sealing properties.
- Vapor Barrier (If Necessary): Depending on the climate and the presence of a vapor barrier elsewhere in the conservatory, an additional vapor barrier may be necessary. This should be installed over the insulation to prevent moisture buildup.
Best Practices for Airtight Installation
Achieving a seamless and airtight installation is paramount to preventing heat loss and maximizing the insulation’s effectiveness. The following best practices should be followed:
- Minimize Gaps: Pay meticulous attention to detail when cutting and fitting the insulation boards. Even small gaps can significantly compromise thermal performance.
- Proper Sealant Selection: Use a high-quality, compatible sealant designed for use with the chosen insulation material. Ensure the sealant is appropriately applied to fill all gaps and joints completely.
- Continuous Barrier: Ensure the insulation creates a continuous barrier without any breaks or interruptions. This is especially important around penetrations such as pipes or wiring.
- Careful Handling: Handle the insulation boards carefully to avoid damage that could compromise their integrity and airtightness.
- Professional Installation (Consideration): For complex roof structures or if unsure about any aspect of the installation process, consider engaging a qualified professional installer to ensure a high-quality, airtight result.
Comparison of Installation Methods
Installation methods vary depending on the insulation material. For example, while solid foam boards are typically adhered and secured mechanically, loose-fill insulation like cellulose or mineral wool is poured or blown into the cavity. Spray foam insulation requires specialized equipment and expertise for proper application. Each method has its advantages and disadvantages in terms of cost, ease of installation, and thermal performance. A professional assessment of the conservatory’s specific needs is recommended to determine the most suitable method and material.
Factors Affecting Insulation Performance
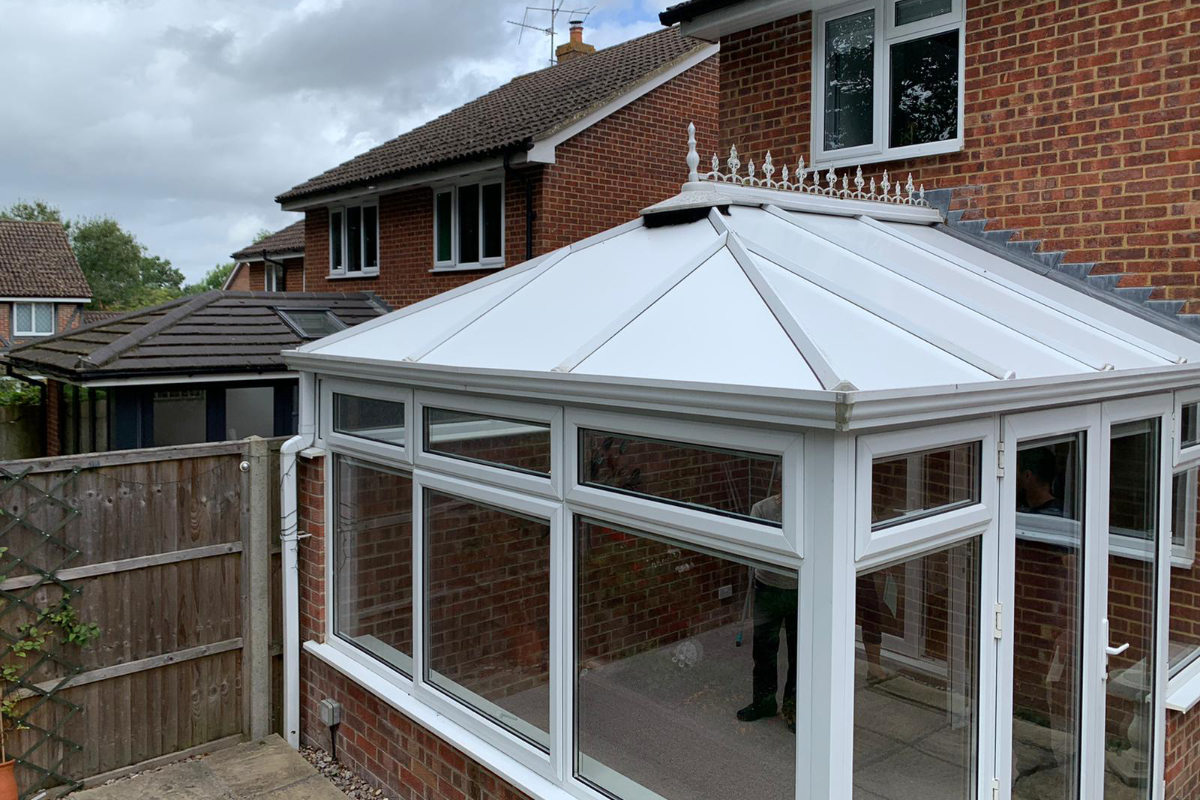
The effectiveness of conservatory roof insulation isn’t solely dependent on the type of insulation material used. Several interconnected factors significantly influence its overall performance, impacting energy efficiency and comfort levels within the conservatory. Understanding these factors is crucial for achieving optimal results and maximizing the return on investment in insulation.
Climate, roof design, window type, air leaks, and ventilation all play a crucial role in determining how well your conservatory roof insulation performs. A poorly insulated roof, regardless of the material used, can lead to significant heat loss in winter and heat gain in summer, resulting in higher energy bills and discomfort.
Climate Influence on Insulation Performance, Best insulation for conservatory roof
The local climate significantly impacts the effectiveness of conservatory roof insulation. In regions with harsh winters and extreme temperature fluctuations, a high-performance insulation system is crucial to maintain a comfortable indoor temperature. For example, in areas with heavy snowfall and freezing temperatures, a thicker layer of insulation with a high R-value (a measure of thermal resistance) is needed to prevent heat loss. Conversely, in warmer climates, the primary concern might shift to preventing excessive heat gain, requiring insulation with good solar reflectance properties. The choice of insulation material and its thickness should be tailored to the specific climatic conditions of the location.
Roof Design’s Impact on Insulation Effectiveness
The design of the conservatory roof itself is another major factor. The pitch of the roof, the presence of any dormers or skylights, and the overall construction method all affect insulation performance. Steeper pitched roofs, for example, can be more challenging to insulate effectively due to the increased surface area and potential for air leaks. Skylights and dormers, while adding aesthetic appeal, can become points of significant heat loss or gain if not properly insulated. The construction materials used in the roof structure itself – such as timber versus metal – also impact heat transfer. Metal frames, for example, conduct heat more readily than timber, requiring additional attention to insulation around these components.
Window Type and its Effect on Insulation
The type of windows installed in the conservatory roof has a substantial influence on overall insulation performance. Double-glazed or triple-glazed units offer significantly better insulation than single-glazed windows. The type of glazing (e.g., low-E glass, which reflects heat back into the room) and the quality of the window frame (e.g., the use of thermally-broken frames to minimize heat transfer through the frame itself) are also important considerations. Poorly sealed or inefficient windows can negate the benefits of even the best roof insulation. For example, a conservatory with high-performance roof insulation but single-glazed windows will still experience significant heat loss in winter.
Air Leaks and Drafts: Their Impact on Insulation
Air leaks and drafts drastically reduce the effectiveness of any insulation system. Even small gaps or cracks in the roof structure, around windows, or in the joints between insulation panels can allow significant amounts of heated or cooled air to escape, negating the benefits of the insulation. This is particularly true for poorly fitted insulation or insufficient sealing around penetrations (such as pipes or electrical wiring). The resulting air infiltration leads to increased energy consumption and reduced comfort levels. A well-sealed roof is paramount for optimal insulation performance.
Ventilation’s Role in Insulation Efficiency and Condensation Prevention
Proper ventilation is crucial for maintaining insulation efficiency and preventing condensation. While insulation prevents heat transfer, it also needs to allow for moisture control. Lack of ventilation can lead to the build-up of moisture within the roof structure, resulting in the formation of condensation, which can damage the insulation and lead to mold growth. A well-ventilated conservatory roof allows moisture to escape, preventing these issues. This can be achieved through strategically placed vents or by incorporating breathable insulation materials that allow moisture to pass through while still providing effective thermal insulation. The balance between adequate insulation and sufficient ventilation is key to a healthy and energy-efficient conservatory.
Cost Considerations and ROI
Investing in conservatory roof insulation is a significant decision, impacting both upfront costs and long-term energy efficiency. Understanding the various cost factors and potential return on investment (ROI) is crucial for making an informed choice. This section details the typical cost ranges for different insulation materials and installation methods, compares initial investment with long-term energy savings, and provides a method for calculating your ROI.
Typical Costs of Conservatory Roof Insulation
The cost of insulating a conservatory roof varies considerably depending on the chosen material, the size of the roof, the complexity of the installation, and the contractor’s rates. Solid polycarbonate roofing panels, for example, are typically more expensive upfront than insulating a glass roof, but they offer superior insulation properties, potentially offsetting the higher initial cost over time. Similarly, retrofitting insulation to an existing glass roof will usually cost more than installing insulation during a new build.
Cost Comparison of Insulation Options
The table below provides a comparative overview of the initial investment and estimated annual energy savings for various insulation options. These figures are estimates and may vary based on location, energy prices, and the specific product used. It’s crucial to obtain quotes from multiple installers for your specific project.
Insulation Type | Typical Installation Cost (Example: UK, 2023, average sized conservatory) | Estimated Annual Energy Savings |
---|---|---|
Solid Polycarbonate Roof Panels (replacement) | £3,000 – £6,000 | £150 – £300 |
Internal Insulation (e.g., thermal blankets) | £500 – £1,500 | £50 – £150 |
External Insulation (e.g., sprayed foam) | £1,000 – £3,000 | £100 – £250 |
Vacuum Insulated Glazing (new glazing installation) | £2,000 – £5,000 | £100 – £250 |
Calculating Return on Investment (ROI)
Calculating the ROI for conservatory roof insulation helps determine the financial viability of the project. The formula for ROI is straightforward:
ROI = (Net Savings / Initial Investment) x 100%
Where:
* Net Savings: The total energy savings over the expected lifespan of the insulation, minus the cost of any maintenance or repairs.
* Initial Investment: The total cost of the insulation materials and installation.
For example, consider a homeowner who invests £2,000 in internal insulation, resulting in annual energy savings of £100. Over a 10-year period, the net savings would be £1,000 (£100/year * 10 years). The ROI would then be:
ROI = (£1,000 / £2,000) x 100% = 50%
This indicates a 50% return on their initial investment over 10 years. It is important to note that this is a simplified calculation and actual ROI may vary based on several factors. Longer lifespans of the insulation will increase the overall ROI.
Energy Efficiency and Sustainability
Insulating your conservatory roof effectively contributes significantly to both the energy efficiency of your home and its overall environmental sustainability. By reducing heat loss in winter and heat gain in summer, you can lessen your reliance on heating and cooling systems, leading to lower energy bills and a smaller carbon footprint. The choice of insulation material plays a crucial role in achieving these goals.
Proper roof insulation minimizes the amount of energy required to maintain a comfortable indoor temperature. This translates directly to reduced energy consumption from both fossil fuel-based and renewable energy sources. Furthermore, the selection of sustainable insulation materials can further enhance the environmental benefits of your project.
Sustainable and Eco-Friendly Insulation Materials
Several insulation materials offer excellent thermal performance while minimizing their environmental impact. These materials often prioritize recycled content, renewable resources, and low embodied energy – the energy consumed in manufacturing and transporting the product.
- Sheep’s wool: A natural, renewable, and biodegradable insulator with excellent thermal properties and moisture-regulating capabilities. Its production process generally has a lower environmental impact compared to synthetic materials.
- Cellulose insulation: Made from recycled paper, this material provides good thermal resistance and is a sustainable alternative to traditional fiberglass insulation. Its production reduces landfill waste and conserves resources.
- Hemp insulation: A rapidly renewable resource, hemp insulation offers good thermal performance and excellent sound absorption. It’s a sustainable and biodegradable option with low embodied energy.
- Recycled denim insulation: This innovative material repurposes old denim jeans, transforming waste into a valuable insulation product. It offers good thermal properties and contributes to a circular economy.
Impact of Roof Insulation on Carbon Emissions and Energy Consumption
The impact of effective conservatory roof insulation on reducing carbon emissions and energy consumption is substantial. A well-insulated conservatory reduces the need for heating in winter and cooling in summer, thereby lowering the demand on energy grids. This reduced energy demand translates directly to fewer greenhouse gas emissions associated with energy production, particularly from fossil fuel sources. For example, a typical UK household might see a reduction of several hundred kilograms of CO2 emissions annually by improving conservatory roof insulation. The specific reduction will depend on factors such as the size of the conservatory, the existing insulation levels, and the climate.
Energy-Efficient Homes through Insulation Choices
Choosing the right insulation for your conservatory roof is a key step towards creating a more energy-efficient home. By minimizing heat transfer through the roof, you create a more stable and comfortable indoor environment, reducing the need for frequent adjustments to heating and cooling systems. This leads to significant energy savings over the lifetime of your home, reducing your environmental impact and lowering your utility bills. For instance, a family in a colder climate might save hundreds of pounds annually on heating costs by upgrading their conservatory roof insulation. This savings increases the return on investment (ROI) associated with the insulation project and provides a tangible benefit to the homeowner.
Noise Reduction Benefits: Best Insulation For Conservatory Roof
A well-insulated conservatory roof significantly reduces noise pollution, creating a more peaceful and relaxing environment. The effectiveness of noise reduction depends heavily on the type of insulation used and its installation. Different materials offer varying degrees of sound absorption and attenuation, impacting the overall quietude of your conservatory.
Effective insulation acts as a barrier, preventing external sounds from penetrating the conservatory. This is crucial in areas with significant traffic noise, nearby construction sites, or other sources of unwanted sound. By absorbing and blocking sound waves, insulation dramatically improves the acoustic comfort of the space, making it ideal for relaxation, reading, or even working from home.
Sound Insulation Properties of Different Materials
The ability of a material to reduce noise is measured by its sound transmission class (STC) rating. Higher STC ratings indicate better sound insulation. For example, solid materials like brick or concrete generally have higher STC ratings than more porous materials. However, the performance of insulation within a conservatory roof system is also dependent on the air gaps and other components of the roof structure.
Common conservatory roof insulation materials exhibit different acoustic properties. Solid polycarbonate panels, while offering good thermal insulation, often have lower STC ratings compared to insulated glass units (IGUs). IGUs, with their air or gas-filled spaces between panes of glass, generally offer superior sound insulation due to the damping effect of the trapped air or gas. Similarly, insulation materials such as mineral wool, which has a fibrous structure, effectively absorbs sound waves, contributing to improved noise reduction. Rigid foam insulation, such as polyurethane or polyisocyanurate, also offers decent sound insulation properties, although perhaps not as effectively as mineral wool in some applications.
Noise Reduction from External Sources
The effectiveness of insulation in reducing noise pollution depends on the frequency and intensity of the external sounds. Lower-frequency sounds, such as those from traffic or construction, are more difficult to attenuate than higher-frequency sounds. However, a well-designed and properly installed insulation system, incorporating multiple layers of materials with varying densities, can significantly reduce the overall noise level from various external sources.
For instance, a conservatory located near a busy road might benefit from a combination of insulated glass units and mineral wool insulation within the roof structure. The IGUs will help reduce high-frequency noise from passing vehicles, while the mineral wool will absorb lower-frequency sounds and vibrations. This multi-layered approach creates a more effective sound barrier, resulting in a quieter conservatory environment.
Comparison of Noise Reduction Capabilities
A direct comparison of noise reduction capabilities requires considering the STC rating of the materials used, along with the overall design of the conservatory roof. While precise figures are difficult to provide without specifying the exact materials and construction, we can make general observations.
Generally, insulated glass units (IGUs) tend to offer better sound insulation than solid polycarbonate panels. Mineral wool insulation typically demonstrates superior sound absorption capabilities compared to rigid foam insulation. However, the combination of different materials and the overall construction of the roof structure play a crucial role in the final noise reduction achieved. A well-designed system incorporating multiple layers of insulation can significantly outperform a system relying solely on a single material, even if that material has a high STC rating.
Dealing with Condensation and Moisture
Condensation and moisture are significant concerns in conservatory roofs, particularly those with inadequate insulation. High humidity levels inside the conservatory, coupled with temperature differences between the warm interior and the cooler exterior surfaces, can lead to condensation, mold growth, and potential structural damage. Choosing the right insulation and employing effective moisture management strategies are crucial for a healthy and comfortable conservatory environment.
Different insulation materials exhibit varying capacities for managing condensation and moisture. Materials with high vapor permeability, such as certain types of wood fiber insulation, allow moisture to pass through more readily, reducing the likelihood of condensation buildup on the interior surface of the roof. In contrast, materials with low vapor permeability, like expanded polystyrene (EPS) or polyurethane foam, act as a vapor barrier, preventing moisture from entering the insulation layer but potentially trapping moisture already present within the roof structure. The ideal choice depends on the specific climate and the existing construction of the conservatory roof.
Vapor Barrier Effectiveness in Preventing Moisture Damage
A vapor barrier is a crucial element in preventing moisture damage to the conservatory roof structure and insulation. Its primary function is to control the movement of water vapor, preventing it from migrating into the insulation and causing dampness, mold, and rot. A properly installed vapor barrier should be placed on the warm side of the insulation, typically on the interior side of the conservatory roof. This prevents warm, moist air from penetrating the insulation layer. Different materials can serve as effective vapor barriers, including polyethylene sheeting, aluminum foil, and specialized vapor barrier membranes. The effectiveness of the vapor barrier is directly tied to its proper installation; any gaps or tears can significantly compromise its performance, leading to moisture intrusion. A continuous and airtight vapor barrier is essential for optimal protection.
Methods for Preventing Condensation and Mold Growth
Several methods can be employed to prevent condensation and mold growth in insulated conservatory roofs. Adequate ventilation is paramount. This can be achieved through strategically placed vents, trickle vents in windows, or even the use of an extractor fan to remove excess moisture from the air. Properly sealing any gaps or cracks in the roof structure will prevent air leakage, reducing the likelihood of condensation forming on cold surfaces. Regular cleaning and maintenance are also crucial. Removing any accumulated dust or debris will improve airflow and prevent the growth of mold. Finally, ensuring the conservatory is adequately heated, particularly during colder months, can minimize the temperature difference between the interior and exterior surfaces, thereby reducing condensation.
Managing Moisture with Different Insulation Types
The choice of insulation material significantly impacts moisture management. For example, mineral wool insulation, while providing excellent thermal performance, can absorb moisture. Therefore, a robust vapor barrier is crucial with this type of insulation. In contrast, closed-cell spray foam insulation has excellent moisture resistance, acting as its own vapor barrier in many cases. However, if moisture is already present within the roof structure before insulation installation, it could potentially be trapped by the closed-cell foam, leading to problems. Understanding the properties of each insulation material and its interaction with moisture is essential for making informed decisions.
Maintenance and Lifespan
Proper maintenance is crucial for maximizing the lifespan and performance of your conservatory roof insulation. Regular checks and minor upkeep can prevent significant problems and ensure your insulation continues to provide effective energy savings and comfort for years to come. Neglecting maintenance can lead to reduced efficiency, costly repairs, and premature replacement.
Regular Maintenance Schedule for Conservatory Roof Insulation
A simple yet effective maintenance schedule can significantly extend the life of your conservatory roof insulation. This schedule should be tailored to the specific type of insulation installed, but some general practices apply to most systems.
Inspection and Cleaning
Regular visual inspections are key to identifying potential problems early. At least twice a year, preferably in spring and autumn, thoroughly inspect the entire roof area for any signs of damage, such as cracks, holes, or water damage. Pay close attention to areas around seams and joints. Remove any accumulated debris, such as leaves, twigs, or dust, using a soft brush or vacuum cleaner with a suitable attachment. For some insulation types, a gentle pressure wash may be appropriate, but always check the manufacturer’s recommendations first to avoid damaging the material.
Addressing Common Problems
Several issues can compromise the effectiveness of conservatory roof insulation. Prompt attention to these problems is crucial to prevent further damage and maintain optimal performance.
Moisture and Condensation
Moisture is a significant threat to many insulation materials. Condensation can occur due to temperature differences between the inside and outside of the conservatory, leading to mold growth and reduced insulation effectiveness. Proper ventilation is crucial to mitigate this. Regularly check for signs of dampness or mold, and address any issues promptly. If condensation is persistent, consider installing a dehumidifier or improving ventilation.
Pest Infestations
Some insulation materials can attract pests, such as rodents or insects. Regular inspections can help detect any signs of infestation early. If pests are found, professional pest control may be necessary. Choose environmentally friendly pest control methods to avoid damaging the insulation material.
Structural Damage
Over time, the conservatory roof structure itself might sustain damage, impacting the insulation. Regular checks for structural issues, such as cracks or loose fittings, are important. Addressing structural problems promptly prevents further damage and ensures the insulation remains effective.
Typical Lifespan of Various Insulation Types
The lifespan of conservatory roof insulation varies significantly depending on the material used, installation quality, and maintenance practices.
Solid Roof Insulation
Solid roof systems, often incorporating materials like polyurethane foam, typically have a lifespan of 20-30 years or more with proper maintenance. This is because the material itself is very durable and resistant to degradation.
Polycarbonate Roof Insulation
Polycarbonate panels, often used in conservatory roofs, are durable but can degrade over time due to UV exposure. Their lifespan is typically 15-25 years, depending on the quality of the panels and the amount of sunlight exposure. Regular cleaning and the application of UV-resistant coatings can extend their lifespan.
Glass Roof Insulation
Glass roofs often incorporate insulating glass units (IGUs) with a lifespan of 10-20 years. Factors like the quality of the sealant and the overall construction significantly influence their lifespan. Replacement may be required sooner if the sealant fails, leading to energy loss and condensation.
Regulatory Compliance and Building Codes
Insulating your conservatory roof requires adherence to various building regulations and safety standards to ensure structural integrity, energy efficiency, and occupant safety. These regulations vary depending on your location, so it’s crucial to consult local authorities and building control departments for specific requirements. Failure to comply can lead to significant penalties and even necessitate costly remedial work.
Building regulations concerning conservatory roof insulation often focus on thermal performance, fire safety, and structural stability. They may specify minimum U-values (a measure of thermal transmittance) for the roof structure, requiring the use of appropriate insulation materials and installation techniques to achieve these standards. Furthermore, regulations may dictate the type of insulation permitted, particularly in relation to fire safety, and stipulate requirements for ventilation to prevent moisture build-up and potential damage.
Relevant Building Codes and Regulations
Building regulations concerning conservatory roof insulation are primarily aimed at ensuring the structure meets minimum energy efficiency standards and poses no safety risks. These standards are typically Artikeld in national building codes and local planning regulations. For example, in many regions, Part L of the Building Regulations in England and Wales specifies minimum standards for energy efficiency in new buildings and extensions, including conservatories. Similar regulations exist in other countries, often incorporating requirements related to thermal performance, airtightness, and fire safety. Specific requirements will vary based on factors such as the age of the property and the type of conservatory being installed. Checking with local building control is essential to ensure compliance.
Safety Standards During Installation
Safe installation practices are paramount during conservatory roof insulation projects. This involves employing qualified and experienced installers who understand the proper handling and application of insulation materials. Safety considerations include the use of appropriate personal protective equipment (PPE) such as gloves, eye protection, and respiratory masks, particularly when working with materials that may release dust or fibres. Working at height often necessitates the use of safety harnesses and scaffolding to prevent falls. Adherence to safe working practices minimises the risk of accidents and injuries during the installation process. Moreover, ensuring the structural integrity of the roof during and after insulation is crucial to prevent future problems.
Penalties for Non-Compliance
Non-compliance with building regulations related to conservatory roof insulation can result in a range of penalties. These may include enforcement notices requiring remedial work to bring the structure up to code. Failure to comply with an enforcement notice can lead to further penalties, including substantial fines. In severe cases, legal action may be taken, potentially resulting in court orders and significant financial repercussions. It is therefore vital to ensure all work is carried out to the required standards and that appropriate certifications are obtained. The costs associated with rectifying non-compliant work can far exceed the initial cost of ensuring compliance.
Choosing the Right Insulation for Specific Needs
Selecting the appropriate insulation for your conservatory roof is crucial for maximizing energy efficiency, comfort, and longevity. The best choice depends on a combination of factors, including your budget, the climate you live in, and your desired level of performance. Careful consideration of these factors will ensure you achieve the best possible results for your specific situation.
Choosing the right insulation involves a careful assessment of your needs and priorities. This process helps to narrow down the options and select the most cost-effective and efficient solution for your conservatory. The following sections provide guidance on this process.
Budget Considerations and Insulation Material Selection
Budget significantly impacts insulation material selection. Lower-cost options like foil-backed insulation or cellular polycarbonate panels might be suitable for those on a tighter budget. However, these options may offer less thermal performance than more expensive materials such as rigid polyurethane foam or sheep’s wool. Higher-budget projects can explore premium options providing superior insulation and longevity, potentially resulting in greater long-term savings on energy bills. For example, a homeowner with a limited budget might opt for a less expensive, but still effective, reflective foil insulation, while a homeowner with a larger budget might choose high-performance polyurethane foam for superior thermal resistance.
Climate and Insulation Performance
Climate plays a crucial role in determining insulation needs. In colder climates, higher R-values (a measure of thermal resistance) are essential to minimize heat loss. Conversely, in warmer climates, the focus may shift towards materials that provide good thermal resistance alongside effective vapor permeability to prevent moisture build-up. For instance, a conservatory in a cold, snowy region might benefit from thick, high-R-value rigid foam insulation, whereas a conservatory in a hot, humid climate might be better suited to a material that allows for better moisture ventilation, such as a breathable insulation like sheep’s wool.
Decision-Making Flowchart for Conservatory Roof Insulation Selection
The following flowchart provides a step-by-step guide to selecting the appropriate insulation:
Start | Assess Budget | High Budget? / \ Yes No | | Choose High-Performance Insulation (e.g., Polyurethane Foam) Choose Cost-Effective Insulation (e.g., Foil Insulation) | | Assess Climate Assess Climate | | Cold Climate? Cold Climate? / \ / \ Yes No Yes No | | | | Choose High R-Value Insulation Choose Moderate R-Value Insulation Choose High R-Value Insulation Choose Moderate R-Value Insulation | | | | Consider Moisture Consider Moisture | | | | Choose Appropriate Material Choose Appropriate Material Choose Appropriate Material Choose Appropriate Material | Install Insulation | End
Assessing Specific Needs of a Conservatory Roof Before Insulation Selection
Before selecting insulation, a thorough assessment of the conservatory roof is necessary. This involves evaluating factors such as the existing roof structure, the presence of any existing insulation, the size and shape of the roof, the desired level of thermal performance, and any potential moisture issues. For example, an older conservatory with a weak structure might require a lighter insulation material to avoid adding excessive weight, while a new conservatory with a strong structure might allow for the use of heavier, more effective insulation. Careful consideration of these factors ensures the chosen insulation is both effective and compatible with the existing structure.
FAQs
What is the R-value, and why is it important?
R-value measures a material’s resistance to heat flow. A higher R-value indicates better insulation, meaning less heat loss in winter and less heat gain in summer.
Can I install conservatory roof insulation myself?
While some insulation types are DIY-friendly, complex installations might require professional help to ensure proper fit and prevent future issues. Consider your skill level and the complexity of your roof design.
How often should I inspect my conservatory roof insulation?
Regular inspections (at least annually) can identify potential problems like damage, moisture buildup, or pest infestations, allowing for timely repairs and preventing more significant issues.
What are the potential penalties for not complying with building regulations?
Penalties vary by location but can include fines, stop-work orders, and even legal action. Always check local building codes before starting any insulation project.