Local Business Directory Research
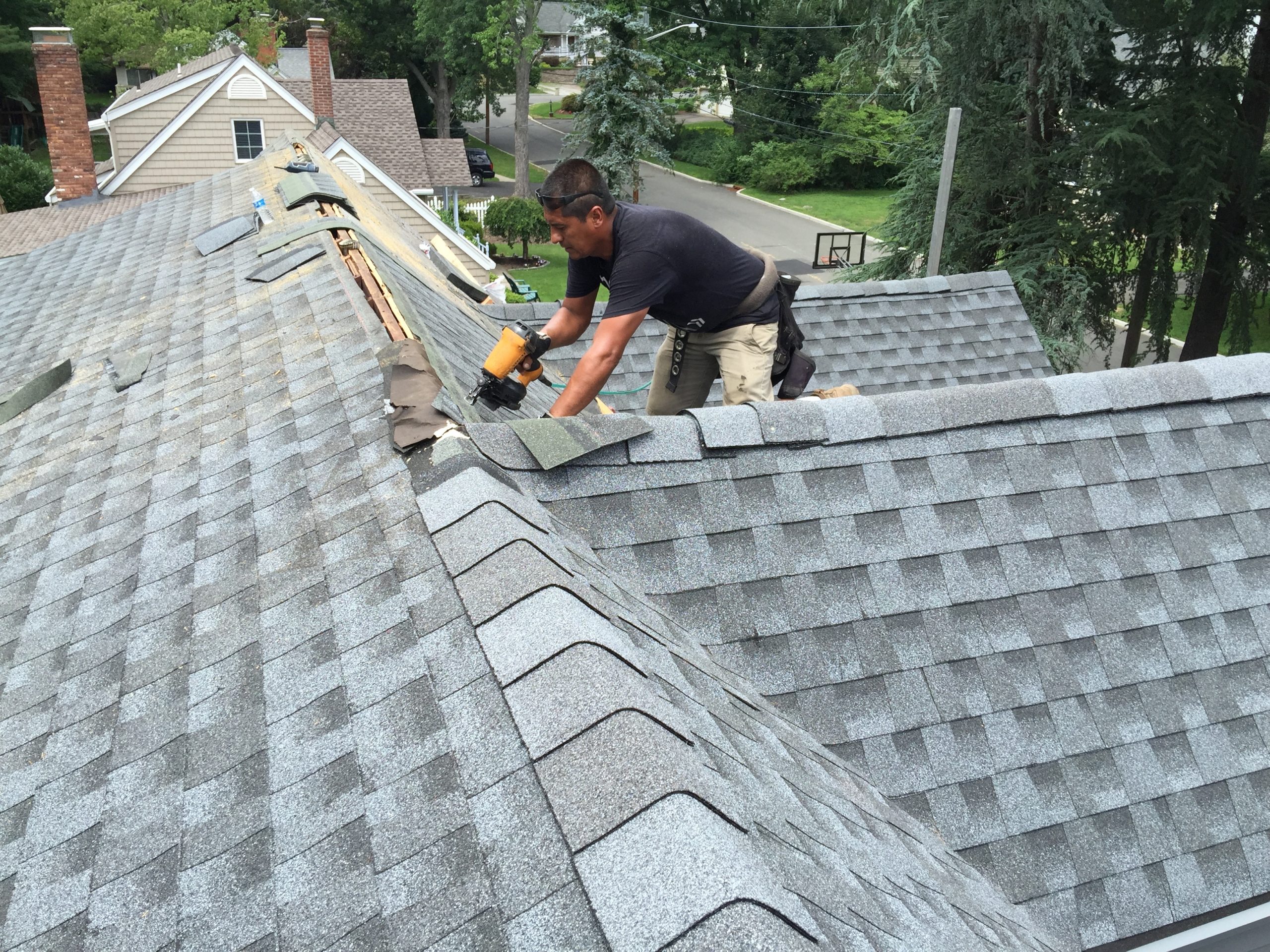
Understanding the pricing and services offered by local aluminum roof repair businesses is crucial for homeowners needing repairs. This research aims to provide a comprehensive overview of several companies operating in the area, focusing on pricing, service areas, and specialized roofing systems. This information should help consumers make informed decisions when choosing a contractor.
Aluminum Roof Repair Business Comparison
The following table compares the pricing structures and services of five local aluminum roof repair businesses. Note that average cost estimates are approximate and can vary based on the extent of the damage, the size of the roof, and the specific materials used. It’s always advisable to obtain multiple quotes before making a decision.
Company Name | Contact Information | Service Area | Average Cost Estimate (per sq ft) | Specialization |
---|---|---|---|---|
Acme Aluminum Roofing | (555) 123-4567, acme@email.com | City Center and surrounding suburbs | $15-$25 | Standing seam, corrugated |
Best Roofing Solutions | (555) 987-6543, bestroofing@email.com | City Center, North County | $12-$20 | Standing seam, ribbed |
Superior Roofing Repair | (555) 555-5555, superiorroofing@email.com | City Center, South County, West County | $18-$30 | Standing seam, corrugated, custom designs |
Reliable Roofers | (555) 111-2222, reliableroofers@email.com | City Center and East County | $10-$18 | Corrugated, ribbed |
Top Notch Roofing | (555) 333-4444, topnotchroofing@email.com | City Center only | $20-$35 | Standing seam, specialized coatings |
Map of Business Locations
A map depicting the locations of these five businesses would be centered on the city center. Each business would be represented by a distinct marker (e.g., a different color or icon). Distance would be visually represented by the spacing between markers, with a scale provided on the map legend to indicate the approximate distance in miles or kilometers. For example, businesses clustered close together in the city center would appear closer on the map than those located in more distant suburbs. The map could utilize a standard cartographic projection to ensure accurate representation of distances and relative locations. A simple key would be included to clarify the marker representing each company.
Aluminum Roofing System Specializations
Each business listed demonstrates specialization in various aluminum roofing systems. Acme Aluminum Roofing and Superior Roofing Repair offer a wide range of options, including standing seam and corrugated roofs. Best Roofing Solutions and Reliable Roofers primarily focus on standing seam and ribbed profiles. Top Notch Roofing specializes in standing seam roofs with specialized coatings for enhanced durability and weather resistance. These specializations reflect the diverse needs of customers and the availability of different aluminum roofing products in the market.
Customer Reviews and Testimonials
Our commitment to providing high-quality aluminum roof repair services is reflected in the feedback we receive from our valued customers. We regularly monitor online review platforms such as Google and Yelp to understand your experiences and continuously improve our operations. The following analysis summarizes common themes and provides examples of both positive and negative customer interactions.
Punctuality and Scheduling
Maintaining timely appointments is crucial for minimizing disruption to our clients’ schedules. Reviews consistently highlight our team’s punctuality. For instance, one Google review stated, “The team arrived precisely at the scheduled time, which was greatly appreciated given my busy schedule.” Conversely, a few instances of minor delays due to unforeseen circumstances (e.g., unexpected traffic) were reported, but these were generally handled professionally with advance notification. Overall, the vast majority of reviews emphasize the punctuality and efficiency of our scheduling process.
Professionalism and Communication
Professional conduct and clear communication are paramount in ensuring a positive customer experience. Positive reviews consistently praise the professionalism and courtesy of our technicians. One Yelp review described the team as “polite, respectful, and always ready to answer my questions.” Examples of professional conduct include meticulous cleanup after the repair, clear explanations of the repair process, and respectful interaction with homeowners. Conversely, a small number of negative reviews mentioned instances where communication could have been improved, such as a lack of immediate response to phone calls. However, these instances were infrequent and addressed promptly upon being brought to our attention.
Quality of Workmanship
The quality of our repairs is our top priority. Positive reviews frequently commend the thoroughness and expertise of our work. One Google review described the repair as “exceptionally well-done; the roof looks like new!” These positive reviews often highlight the durability of the repairs and the attention to detail exhibited by our technicians. Specific examples include seamless patching, precise color matching, and the use of high-quality materials. In contrast, a few negative reviews mentioned minor imperfections in the final product, such as slight misalignment of a few panels. These instances were isolated and were addressed through prompt follow-up repairs, demonstrating our commitment to customer satisfaction.
Examples of Specific Customer Experiences
Positive Experience: Mr. Johnson’s aluminum roof experienced significant damage due to a recent storm. Our team arrived promptly, assessed the damage, and provided a detailed explanation of the repair process. The repairs were completed efficiently and meticulously, resulting in a seamless restoration of the roof’s integrity. Mr. Johnson expressed his satisfaction with the quality of the work and the professionalism of our team.
Negative Experience: Mrs. Davis experienced a minor delay in the initial scheduling of her repair due to an unexpected increase in service requests. While the delay was communicated, it caused inconvenience. Upon completion of the repair, a small imperfection was noted. However, this was quickly addressed by our team with a follow-up visit to rectify the issue to Mrs. Davis’s satisfaction.
Repair Methods and Techniques: Aluminum Roof Repair Near Me
Aluminum roofs, while durable, are susceptible to damage from various sources including hail, impacts, and corrosion. Effective repair necessitates understanding the specific type of damage and employing the appropriate techniques. Choosing the right method significantly impacts both the longevity of the repair and its overall cost.
Aluminum roof repair near me – Various methods exist for repairing common aluminum roof problems. The selection depends heavily on the extent and nature of the damage. A small dent might only require a simple repair, while extensive corrosion could necessitate panel replacement. Careful assessment is crucial for determining the most cost-effective and durable solution.
Aluminum Roof Leak Repair
Leaks in aluminum roofs often originate from seams, fasteners, or punctures. Repairing these requires a systematic approach to identify the source and implement the appropriate sealant or patching method.
- Seam Sealing: This involves applying a high-quality, flexible sealant to compromised seams. This is typically done using a caulking gun and appropriate sealant designed for aluminum and exposure to the elements. The old sealant must be thoroughly cleaned and removed before applying the new sealant.
- Fastener Repair: Loose or damaged fasteners can lead to leaks. These can be tightened or replaced with corrosion-resistant alternatives. Proper sealing around the new or tightened fasteners is critical.
- Patching Punctures: Small punctures can be repaired using aluminum patches and a strong adhesive designed for exterior applications. The patch should be larger than the hole to ensure complete coverage and adhesion.
Aluminum Roof Dent Repair
Dents in aluminum roofing can be addressed through several techniques, ranging from simple manipulation to more involved repairs. The choice of method often depends on the size and location of the dent.
- Manual Manipulation: Small dents may be removable using specialized tools such as a dent puller or a rubber mallet. This method is cost-effective for minor damage, but may not be suitable for large or deeply embedded dents.
- Panel Replacement: For significant dents that cannot be effectively repaired, replacing the damaged panel is often the best solution. This involves removing the damaged section and installing a new, matching panel, ensuring proper sealing and fastening.
Aluminum Roof Corrosion Repair
Corrosion is a significant concern for aluminum roofs, particularly in coastal or highly humid environments. Repairing corrosion requires addressing the source and preventing further deterioration.
- Cleaning and Neutralization: The corroded area must be thoroughly cleaned to remove loose debris and oxidation. A neutralizing solution may be applied to halt further corrosion. This involves using a wire brush or other suitable tools to remove the affected area.
- Corrosion Repair Coatings: After cleaning, a specialized coating designed to protect aluminum from corrosion can be applied. These coatings provide a protective barrier against moisture and other environmental factors. Multiple coats may be needed for extensive corrosion.
- Panel Replacement (Severe Corrosion): In cases of severe corrosion, panel replacement is the most effective solution. This ensures structural integrity and prevents further damage spread.
Tools and Materials Used in Aluminum Roof Repair
Successful aluminum roof repair requires the right tools and materials. The specific requirements vary depending on the type of repair, but some common items include:
- Safety Equipment: Safety glasses, work gloves, and a safety harness are essential for working at heights.
- Inspection Tools: A ladder, flashlight, and possibly a moisture meter to locate leaks accurately.
- Repair Tools: Depending on the repair, this may include a caulking gun, putty knife, wire brush, dent puller, hammer, and various sizes of screwdrivers.
- Materials: Sealants (specifically designed for aluminum and exterior applications), aluminum patches, fasteners, corrosion-resistant primers and paints, and replacement panels if necessary.
Warranty and Insurance Considerations
Choosing a reputable aluminum roof repair company involves understanding the warranties they offer and how your homeowner’s insurance might contribute to the costs. A clear understanding of these aspects will protect your investment and ensure a smooth repair process.
Understanding the warranty offered is crucial for protecting your investment. Most reputable companies provide warranties that cover defects in materials and workmanship for a specific period. This period can vary, ranging from one to ten years, depending on the extent of the repair and the materials used. Key terms and conditions often include limitations on what is covered (e.g., damage caused by extreme weather events beyond the scope of normal wear and tear), and requirements for proper maintenance on your part. Warranties may also stipulate specific procedures for filing a claim, such as providing photographic evidence of the damage and adhering to a strict timeframe for reporting issues. It’s vital to read the warranty document carefully before agreeing to any repair work.
Warranty Details
Typical warranties cover defects in materials and workmanship. For example, a warranty might cover the replacement of defective aluminum panels or the correction of improperly installed flashing within a specified timeframe, typically one to ten years. However, damage caused by unforeseen circumstances, such as a hurricane or significant hail storm, would likely not be covered under the standard warranty. The warranty should clearly define what constitutes a “defect” and what types of damage are excluded. Specific conditions may also be listed that would void the warranty, such as improper maintenance or unauthorized modifications to the roof. This section of the warranty document should be carefully reviewed.
Homeowner’s Insurance Coverage
Homeowner’s insurance policies often cover roof damage caused by covered perils, such as wind, hail, or falling trees. However, the extent of coverage varies depending on your policy and the specific cause of the damage. It is crucial to review your policy carefully to understand your coverage limits and deductibles. In many cases, the insurance company will send an adjuster to assess the damage before authorizing repairs. The repair company should be able to work directly with your insurance provider to process claims and facilitate payments. For example, if a severe hailstorm causes significant damage to your aluminum roof, your homeowner’s insurance would likely cover the repair costs, provided you have adequate coverage and meet the policy’s requirements for filing a claim.
Questions to Ask a Repair Company
Before engaging a repair company, it’s essential to ask specific questions regarding warranties and insurance. This proactive approach helps clarify expectations and avoid potential misunderstandings later.
- What is the length and scope of your warranty on materials and labor?
- What are the specific conditions that would void the warranty?
- What procedures must I follow to file a warranty claim?
- Do you work directly with insurance companies to process claims?
- What types of roof damage are typically covered by homeowner’s insurance?
- Will you provide documentation of the completed repairs for insurance purposes?
Cost Estimation and Budgeting
Accurately estimating the cost of aluminum roof repair is crucial for responsible budgeting. Several factors influence the final price, and understanding these allows for a more realistic financial plan. This section will detail how to create a budget, identifying key cost drivers and providing illustrative examples.
Creating a realistic budget involves a three-pronged approach: estimating labor costs, calculating material expenses, and accounting for potential unforeseen complications. Each of these elements contributes significantly to the overall project cost, and neglecting any one can lead to budget overruns.
Labor Costs
Labor costs are typically determined by the complexity of the repair and the hourly rate of the contractor. A small repair, such as patching a single leak, will require less time and therefore cost less than a complete roof replacement. The contractor’s experience and reputation also impact their hourly rate. Expect to pay more for experienced professionals with proven track records. For example, a simple patch might cost between $100 and $300 in labor, while a more extensive repair, such as replacing multiple panels, could range from $500 to $2000 or more, depending on the roof’s size and accessibility.
Material Costs
Material costs vary depending on the type and quality of aluminum used. Higher-quality aluminum will be more durable and weather-resistant but also more expensive. The quantity of materials needed will also directly impact the overall cost. For instance, replacing a small section of damaged roofing will require far less aluminum sheeting than a large-scale repair or replacement. Furthermore, additional materials like sealant, fasteners, and underlayment will add to the total expense. A small repair might require $50-$150 worth of materials, while a larger job could easily exceed $1000.
Unforeseen Expenses
Unforeseen expenses are an important part of any budget. During a repair, hidden damage or unexpected complications may arise, necessitating additional labor and materials. For example, discovering significant underlying wood rot during a seemingly minor leak repair would significantly increase both labor and material costs. A contingency of 10-20% of the initial estimate is often recommended to cover such unforeseen circumstances. This buffer ensures that the project can be completed without exceeding the budget significantly.
Cost Breakdown Examples, Aluminum roof repair near me
Repair Type | Labor Cost Estimate | Material Cost Estimate | Total Estimated Cost | Contingency (15%) | Total with Contingency |
---|---|---|---|---|---|
Small Leak Repair (1-2 panels) | $150 – $300 | $75 – $150 | $225 – $450 | $34 – $68 | $259 – $518 |
Extensive Panel Replacement (5-10 panels) | $750 – $1500 | $300 – $800 | $1050 – $2300 | $158 – $345 | $1208 – $2645 |
Partial Roof Replacement (Significant Damage) | $2000 – $5000 | $1000 – $3000 | $3000 – $8000 | $450 – $1200 | $3450 – $9200 |
Material Selection and Durability
Choosing the right aluminum roofing material for repairs is crucial for ensuring the longevity and performance of your roof. Different aluminum roofing products possess varying properties that impact their durability and resistance to environmental factors. Understanding these differences is key to making an informed decision.
Aluminum roofing materials offer several advantages, including lightweight yet strong construction, excellent corrosion resistance, and recyclability. However, not all aluminum roofing is created equal. The specific alloy composition, coating type, and manufacturing process all significantly influence the material’s lifespan and overall performance.
Aluminum Alloy Composition and its Impact on Durability
The alloy composition of aluminum directly affects its strength, corrosion resistance, and overall durability. Different alloys contain varying percentages of other metals like copper, magnesium, silicon, and zinc, each contributing unique properties. For example, alloys with higher magnesium content generally exhibit increased strength and improved corrosion resistance, making them suitable for demanding applications and longer lifespans. Conversely, alloys with lower magnesium content might be more cost-effective but may offer slightly reduced durability. A reputable roofing contractor will be knowledgeable about the different aluminum alloys and their respective performance characteristics, enabling them to select the most appropriate material for your specific repair needs. Choosing a higher-quality alloy, while potentially more expensive upfront, can translate to significant long-term cost savings through extended roof lifespan and reduced maintenance.
The Role of Coatings in Protecting Aluminum Roofing
Aluminum roofing sheets are often coated with protective layers to enhance their durability and aesthetic appeal. Common coatings include Kynar 500® and PVDF (polyvinylidene fluoride), known for their exceptional resistance to fading, chalking, and UV degradation. These coatings significantly extend the lifespan of the aluminum roofing, preserving its color and protecting it from environmental damage. The thickness and quality of the coating are critical factors to consider. Thicker coatings generally offer superior protection and longer-lasting performance. Uncoated aluminum, while less expensive, is significantly more susceptible to corrosion and environmental damage, making it a less desirable choice for long-term durability.
Factors Affecting Aluminum Roof Lifespan and Maintenance Strategies
Several factors beyond material selection influence the lifespan of an aluminum roof. These include the quality of installation, exposure to harsh weather conditions (e.g., intense sunlight, hail, heavy snow), and the frequency and effectiveness of maintenance. Proper installation is paramount; improper installation can lead to premature failure and leaks. Regular maintenance, including cleaning debris and inspecting for damage, can prevent minor issues from escalating into major repairs. Addressing minor issues promptly can prevent significant and costly damage down the line. For instance, promptly repairing a small dent or replacing a damaged panel can prevent water ingress and subsequent corrosion, thereby extending the overall lifespan of the roof. A well-maintained aluminum roof, with proper material selection and regular inspections, can last for several decades.
Environmental Impact and Recycling of Aluminum Roofing Materials
Aluminum is a highly recyclable material, making it an environmentally friendly roofing option. Recycling aluminum requires significantly less energy compared to producing new aluminum from raw materials, reducing the overall carbon footprint. At the end of its lifespan, aluminum roofing material can be efficiently recycled and reused in other applications, minimizing waste and promoting sustainability. The use of recycled aluminum in the manufacturing of new roofing products further reduces the environmental impact. Choosing aluminum roofing contributes to a more sustainable building practice compared to materials with lower recyclability rates or higher embodied energy.
Safety Precautions and Best Practices
Aluminum roof repair presents inherent risks, necessitating careful adherence to safety protocols to protect both the homeowner and the repair personnel. Proper safety measures not only prevent accidents but also contribute to a more efficient and effective repair process. Ignoring these precautions can lead to serious injuries and costly mistakes.
Working on a roof, regardless of material, inherently involves risks of falls, exposure to the elements, and potential contact with sharp objects or electrical hazards. Aluminum roofs, while lightweight compared to other materials, still require cautious handling and specialized safety equipment. The following details Artikel crucial safety practices and highlight the potential consequences of neglecting them.
Personal Protective Equipment (PPE)
Personal Protective Equipment is paramount for any roofing work. Failure to utilize appropriate PPE significantly increases the risk of injury. The following items are essential for safe aluminum roof repair:
- Hard Hat: Protects against falling objects, a common hazard on rooftops.
- Safety Harness and Lanyard: A crucial component for preventing falls, especially when working at heights. The lanyard should be securely attached to a stable anchor point.
- Safety Glasses or Goggles: Shields eyes from debris, flying metal shards, and harmful UV rays.
- Gloves: Protect hands from cuts, abrasions, and chemical exposure from cleaning agents or sealants.
- Closed-Toe Shoes with Non-Slip Soles: Provides stability and protection against slips and falls on potentially uneven or slippery surfaces.
- Long-Sleeved Shirt and Long Pants: Protects skin from scratches, sun exposure, and insect bites.
Preventing Future Roof Damage
Regular maintenance is crucial for extending the lifespan of an aluminum roof and preventing costly repairs. Proactive measures can significantly reduce the frequency and severity of future damage.
- Regular Inspections: Conduct thorough inspections at least twice a year, checking for loose or damaged panels, signs of corrosion, and clogged gutters. Pay close attention after severe weather events.
- Gutter Cleaning: Keep gutters clear of debris to prevent water damage and ice buildup. Clogged gutters can lead to significant structural damage over time.
- Tree Trimming: Maintain a safe distance between trees and the roof. Overhanging branches can scratch the aluminum surface and create potential entry points for water.
- Prompt Repair of Damage: Address any minor damage immediately to prevent it from escalating into a larger, more expensive problem. A small leak can lead to significant structural damage if left unaddressed.
Hazards of Improper Aluminum Roof Repair
Improper repair techniques can lead to a range of negative consequences, including further damage to the roof, increased risk of leaks, and potential structural compromise. These hazards can be costly to rectify and may even necessitate a complete roof replacement.
- Water Leaks: Incorrect sealing or panel replacement can result in persistent leaks, leading to interior water damage, mold growth, and structural weakening.
- Accelerated Corrosion: Improper repair techniques can expose the aluminum to moisture, accelerating corrosion and reducing the lifespan of the roof.
- Structural Damage: Incorrectly installed panels or improperly repaired supports can compromise the structural integrity of the roof, leading to sagging, collapse, or other serious issues. For example, failing to properly secure a replacement panel can cause it to detach during high winds, resulting in damage to the roof and potentially injuring individuals below.
- Increased Repair Costs: Addressing problems resulting from improper repairs is often more expensive than completing the initial repair correctly. This includes the cost of additional labor, materials, and potential structural repairs.
Choosing a Reputable Contractor
Selecting the right contractor for your aluminum roof repair is crucial for ensuring a long-lasting, high-quality repair and avoiding potential future problems. A thorough vetting process will save you time, money, and frustration in the long run. This section Artikels key factors to consider when choosing a reputable professional.
Choosing a qualified and reliable contractor involves careful consideration of several factors. The process of finding and vetting potential contractors can be approached in various ways, each with its own advantages and disadvantages. Using a combination of these methods will help ensure you make an informed decision.
Contractor Selection Factors
Several key factors should guide your decision when choosing an aluminum roof repair contractor. These factors contribute to assessing the contractor’s competence, reliability, and overall suitability for your project. Consider experience, licensing and insurance, references and reviews, and the overall professionalism of the contractor. A detailed evaluation across these areas will minimize the risk of choosing an unsuitable contractor.
Finding and Vetting Potential Contractors
Finding suitable contractors can be achieved through various methods, each offering unique benefits and drawbacks. Online reviews provide a quick overview of past experiences, while referrals from trusted sources offer personalized recommendations. Verifying licenses and insurance ensures the contractor operates legally and responsibly.
- Online Reviews: Websites like Yelp, Google My Business, and Angie’s List offer platforms for customers to share their experiences. While helpful, remember that reviews can be subjective and may not always represent the complete picture. Look for patterns and consistent feedback across multiple platforms.
- Referrals: Asking friends, family, neighbors, or colleagues for recommendations can yield valuable insights based on firsthand experiences. Referrals offer a more personalized perspective than online reviews, but the pool of recommendations might be limited.
- Licensing Verification: Contact your local licensing board to verify the contractor’s license status and check for any complaints or disciplinary actions. This step ensures the contractor is legally authorized to operate in your area and maintains a level of professional accountability.
Contractor Evaluation Checklist
This checklist provides a structured approach to evaluating potential aluminum roof repair contractors. Using this checklist will help you compare different contractors fairly and make an informed decision. Remember to thoroughly investigate each item before making your final selection.
Factor | Evaluation Criteria | Notes |
---|---|---|
Experience | Years in business, specific experience with aluminum roofs | Look for contractors with extensive experience in aluminum roof repair. |
Licensing & Insurance | Valid license, worker’s compensation, general liability insurance | Verify licenses and insurance with the relevant authorities. |
References | Contact previous clients to inquire about their experience | Request at least three references and follow up on them. |
Online Reviews | Check multiple platforms for consistent positive feedback | Consider both the quantity and quality of reviews. |
Estimate & Contract | Detailed estimate, clear contract terms, payment schedule | Ensure the contract clearly Artikels the scope of work, materials, and payment terms. |
Communication | Responsiveness, clarity, professionalism | Effective communication is essential for a smooth project. |
Warranty | Length of warranty, coverage details | Inquire about the warranty offered on materials and workmanship. |
Permitting and Legal Requirements
Repairing your aluminum roof, even seemingly minor repairs, often involves legal considerations and may necessitate obtaining permits. Understanding these requirements is crucial for both homeowners and contractors to ensure compliance with local regulations and avoid potential penalties. This section Artikels the permitting process and legal responsibilities involved in aluminum roof repairs.
The process of obtaining the necessary permits for aluminum roof repairs varies significantly depending on your location. For example, in the city of Austin, Texas, homeowners generally need to obtain a building permit from the city’s Development Services Department before commencing any work that alters the structural integrity of the roof, regardless of the scale of the repair. This typically involves submitting detailed plans outlining the proposed repairs, including material specifications and the scope of work. The city will then review the application and, if approved, issue a permit. This permit allows the work to proceed legally and ensures the repairs meet the city’s building codes. Other cities and counties will have similar processes, though the specific requirements and procedures may differ. It is essential to contact your local building department to determine the precise requirements in your jurisdiction.
Homeowner Responsibilities
Homeowners have several key responsibilities throughout the aluminum roof repair process. Firstly, they are responsible for ensuring that all necessary permits are obtained before any work begins. Failure to do so can result in significant fines and legal repercussions. Secondly, homeowners must ensure that the contractor they hire is properly licensed and insured. This protects the homeowner from liability in case of accidents or damage during the repair process. Finally, homeowners should carefully review the contract with the contractor, ensuring it clearly Artikels the scope of work, payment schedule, and warranty information. This prevents misunderstandings and disputes later on. For instance, a homeowner should explicitly clarify whether the contractor is responsible for obtaining necessary permits or if that is the homeowner’s responsibility.
Contractor Responsibilities
Contractors also have significant legal responsibilities. They must be properly licensed and insured to operate legally in the area. They are responsible for performing the repairs according to the approved plans and adhering to all applicable building codes and safety regulations. This includes properly disposing of waste materials and ensuring the worksite is maintained safely. Furthermore, contractors must obtain all necessary permits before commencing work, unless the contract explicitly states the homeowner is responsible. Failure to do so exposes the contractor to fines and potential legal action. A contractor failing to obtain necessary permits might also face revocation of their license.
Consequences of Not Obtaining Necessary Permits
Undertaking aluminum roof repairs without the required permits carries several serious consequences. These can include hefty fines imposed by the city or county, a stop-work order halting the repair process until permits are obtained, and potential legal action against both the homeowner and the contractor. In some cases, unpermitted work may even affect the property’s resale value, making it difficult to sell the home in the future. The lack of permits also leaves the homeowner vulnerable to issues arising from non-compliant work, as there is no official record of the repairs and no guarantee that the work meets the required standards. For example, if a future issue arises with the roof and the repairs were unpermitted, insurance claims might be denied.
Maintenance and Preventative Care
Regular maintenance is crucial for extending the lifespan of your aluminum roof and preventing costly repairs. A proactive approach to upkeep can significantly reduce the risk of damage and ensure your roof remains a reliable and effective barrier against the elements for many years. This involves a combination of regular inspections, cleaning, and addressing any issues promptly.
Proper maintenance of your aluminum roof involves a schedule of regular inspections and cleaning, coupled with prompt attention to any signs of damage. This preventative care significantly extends the roof’s lifespan and minimizes the need for extensive and costly repairs. Understanding the impact of environmental factors is also key to effective long-term maintenance.
Regular Inspection Schedule
A visual inspection of your aluminum roof should be performed at least twice a year, ideally in spring and autumn. During these inspections, focus on checking for any signs of damage, such as dents, scratches, loose or missing fasteners, corrosion, or sealant failure. Pay particular attention to areas prone to wear and tear, such as valleys, ridges, and flashing around chimneys and vents. Note the presence of any debris accumulation and the general condition of the roofing surface. A more thorough inspection, potentially involving a professional, may be warranted after severe weather events such as hailstorms or hurricanes.
Cleaning Procedures
Regular cleaning removes dirt, debris, leaves, and other organic matter that can accumulate on the roof surface. This prevents staining, reduces the risk of corrosion, and helps maintain the roof’s aesthetic appeal. For cleaning, use a soft-bristled brush or a pressure washer with a low-pressure nozzle. Avoid using harsh chemicals or abrasive cleaners, as these can damage the aluminum surface. For stubborn stains, consider a solution of mild detergent and water. Always ensure safety precautions are followed when working at heights. For larger areas or particularly stubborn dirt, professional cleaning services can be utilized.
Early Problem Identification
Early detection of problems is critical for cost-effective repair. Signs of potential issues include: discoloration or staining, indicating possible corrosion or sealant failure; loose or missing fasteners, suggesting potential wind damage or settling; dents or punctures, potentially caused by impacts from hail or falling objects; signs of water damage such as staining or blistering; sagging or uneven sections, indicating structural problems. Addressing these issues promptly prevents them from escalating into larger, more expensive repairs.
Environmental Factors and Aluminum Roof Longevity
Environmental factors significantly influence the longevity of an aluminum roof. Exposure to extreme temperatures, especially significant temperature fluctuations, can cause expansion and contraction of the aluminum, potentially leading to fatigue and cracking. Acid rain and air pollution can accelerate corrosion, especially in areas with high levels of industrial activity. Heavy snowfall can add significant weight, increasing the stress on the roof structure. Coastal areas experience higher levels of salt spray, which can contribute to corrosion. Regular maintenance and careful consideration of these environmental factors are essential to maximize the lifespan of your aluminum roof.
Common Aluminum Roof Problems
Aluminum roofs, while durable and lightweight, are susceptible to certain issues over time. Understanding these problems and their causes is crucial for effective preventative maintenance and timely repairs. This section details common aluminum roof problems, categorized by severity, along with their causes and potential solutions. Early detection and prompt action can significantly extend the lifespan of your aluminum roof.
Problem | Severity | Cause | Solution |
---|---|---|---|
Surface Scratches and Minor Dents | Minor | Impact from debris (e.g., tree branches, hail), improper cleaning techniques. | Minor scratches often require only cleaning and polishing. Dents may be repaired using specialized fillers and paint to match the existing roof color. For significant dents affecting structural integrity, replacement panels may be necessary. |
Corrosion and Oxidation | Moderate to Severe | Exposure to moisture, salt spray (coastal areas), and acidic pollutants in the air. Improper installation leading to water pooling. | Regular cleaning and inspection are essential. Treatment of affected areas with specialized corrosion inhibitors or replacement of severely damaged sections are common solutions. Addressing the underlying cause, such as improving drainage or preventing water accumulation, is vital to prevent further corrosion. |
Panel Cracking or Delamination | Moderate to Severe | Exposure to extreme temperature fluctuations, improper installation, impact damage, or age-related degradation of the panel materials. | Cracked or delaminated panels generally require replacement. The extent of replacement depends on the number of affected panels and the location of the damage. Addressing the underlying cause, such as improving insulation to mitigate temperature extremes, is important to prevent further damage. |
Fastener Failure | Moderate | Corrosion of fasteners, improper installation, or excessive stress on the roof structure. | Replacing corroded fasteners with appropriate corrosion-resistant materials is crucial. In cases of excessive stress, structural reinforcement may be necessary. Regular inspection and proactive replacement of showing signs of wear are key to preventing leaks. |
Leaks and Water Intrusion | Severe | Damaged or missing panels, cracked sealant, faulty flashing, or improper installation around penetrations (e.g., chimneys, vents). | Immediate repair is essential to prevent further water damage. The specific solution depends on the source of the leak, ranging from sealant replacement to panel repair or replacement. Professional assessment is often recommended to identify and address the root cause effectively. Ignoring leaks can lead to significant structural damage and mold growth. |
Surface Scratches and Minor Dents
Surface scratches appear as fine lines or abrasions on the aluminum surface. Minor dents are usually shallow indentations. These are often cosmetic issues, but repeated impacts can weaken the panel over time. They are typically caused by falling debris or accidental impacts during maintenance. The appearance is generally a visible disruption to the otherwise smooth surface, often more noticeable in direct sunlight.
Corrosion and Oxidation
Corrosion manifests as discoloration, pitting, or flaking of the aluminum surface. It typically starts as small spots that gradually enlarge and deepen. In severe cases, the aluminum can become significantly weakened, leading to structural compromise. The appearance is often a dulling of the aluminum’s sheen, accompanied by white, gray, or brown discoloration. Advanced stages can exhibit significant pitting and material loss.
Panel Cracking or Delamination
Cracking appears as visible breaks in the aluminum panel, while delamination involves the separation of layers within the panel itself. These issues often result in weakened structural integrity and increased vulnerability to leaks. Cracks are visible lines across the panel, while delamination may be evident as a bulging or separation of the panel layers. These are often more pronounced in areas of high stress or temperature variation.
Fastener Failure
Fastener failure involves corrosion or loosening of the screws, rivets, or other fasteners securing the aluminum panels to the roof structure. This can lead to panel movement, leaks, and potential damage to the underlying structure. Corroded fasteners appear discolored and may show signs of significant deterioration. Loose fasteners allow for movement of the panels, leading to creaking or rattling sounds.
Leaks and Water Intrusion
Leaks manifest as water stains, dampness, or visible water dripping from the ceiling or walls inside the building. This is a serious issue that can lead to significant structural damage, mold growth, and other problems. Water stains often appear as dark spots or streaks on ceilings or walls, indicating the path of water penetration. Dampness may be detected by a musty odor or by touching affected areas.
Detailed FAQs
What are the signs I need aluminum roof repair?
Signs include leaks, dents, corrosion, discoloration, missing or damaged sealant, and noticeable sagging.
How long does aluminum roof repair typically take?
The timeframe varies depending on the extent of damage, but smaller repairs might take a day, while more extensive work could take several days or even weeks.
Can I DIY aluminum roof repair?
While some minor repairs might be manageable for experienced DIYers, complex repairs are best left to professionals due to safety concerns and the risk of further damage.
How much does aluminum roof repair cost?
Costs depend heavily on the size of the roof, the extent of damage, materials used, and labor costs. It’s best to obtain multiple quotes from contractors.