Cost Analysis of Asphalt Shingle Replacement
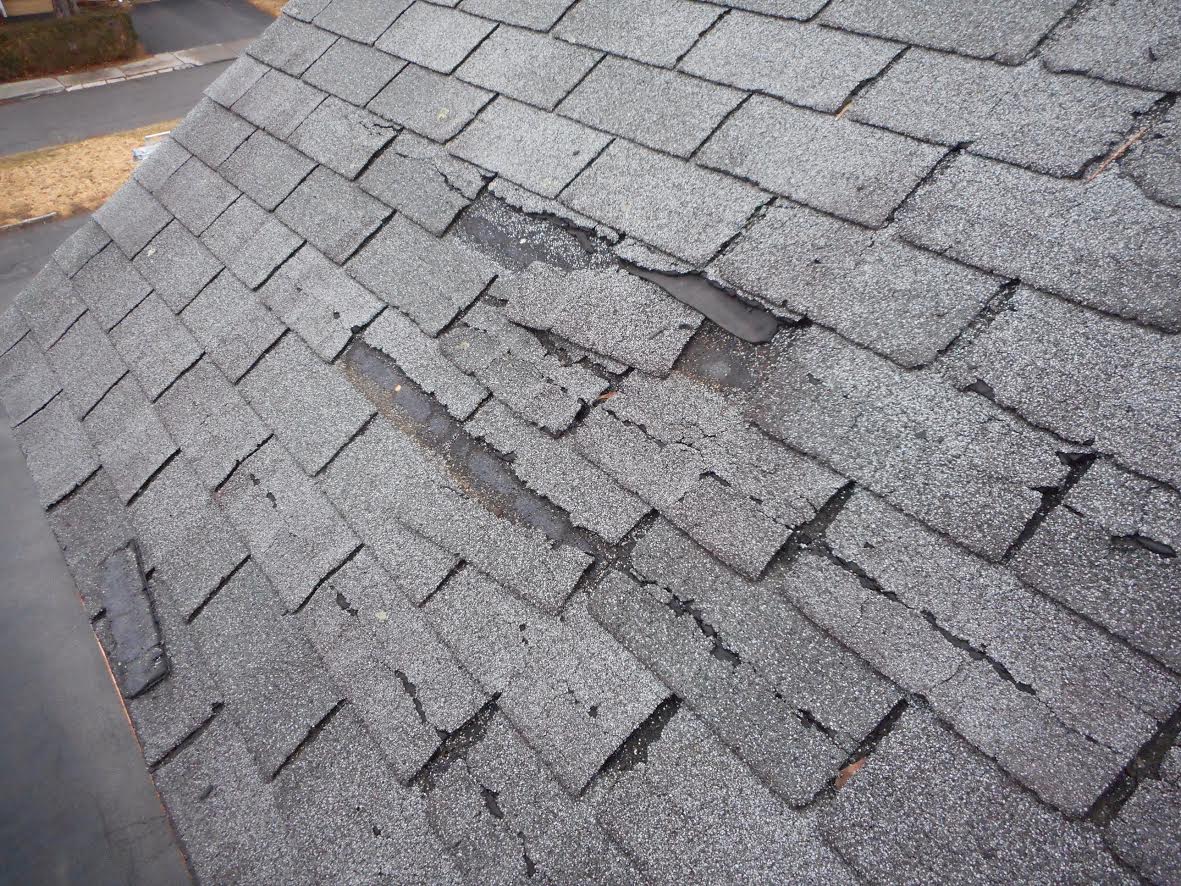
Replacing your asphalt shingles is a significant investment, and understanding the associated costs is crucial for effective budgeting and planning. This section provides a breakdown of the average costs involved, influencing factors, and strategies for cost savings.
Average Costs for Asphalt Shingle Replacement
The cost of asphalt shingle replacement varies considerably depending on several factors, primarily roof size and geographic location. Labor rates, material prices, and permit fees all contribute to the overall expense. For a medium-sized home (approximately 2,000 square feet) in a mid-range cost area, the total cost could range from $10,000 to $20,000. Larger roofs will naturally incur higher costs, while smaller roofs will be less expensive. Regional differences in labor and material costs can significantly impact the final price. For example, coastal areas or regions with high demand for skilled labor may have higher costs than rural areas. Permitting fees also vary by location and are usually a relatively small percentage of the overall cost.
Cost-Saving Strategies for Homeowners
Several strategies can help homeowners reduce the cost of their asphalt shingle replacement project. Negotiating with multiple contractors to obtain competitive bids is a crucial first step. Choosing less expensive, but still high-quality, asphalt shingles can significantly reduce material costs without compromising durability. Scheduling the project during the off-season (typically fall or winter) may result in lower labor costs due to reduced contractor demand. Finally, homeowners can save money by handling some of the preparatory work themselves, such as clearing debris from the roof, although it is advisable to leave the actual shingle installation to professionals for safety and warranty reasons.
Factors Influencing the Overall Cost of Asphalt Shingle Replacement
Several factors significantly influence the overall cost of an asphalt shingle replacement project. Roof complexity plays a major role; steeply pitched roofs, complex designs with many valleys and hips, and the presence of dormers or chimneys all increase labor time and material requirements, thus increasing the overall cost. The quality of the materials selected also impacts the price. Higher-quality shingles, such as those with enhanced durability and weather resistance, tend to be more expensive than standard options. Furthermore, the condition of the existing roof decking can affect the cost. If the decking needs repair or replacement before new shingles can be installed, this adds to the overall expense. Finally, unexpected issues discovered during the project, such as significant underlying damage or necessary repairs to the roof structure, can also lead to cost overruns.
Comparison of Asphalt Shingle Costs
The following table compares the costs of different asphalt shingle types. These are average costs and can vary based on location, supplier, and installation costs.
Shingle Type | Average Cost per Square (100 sq ft) | Lifespan (Years) | Warranty Information |
---|---|---|---|
3-Tab Shingles | $80 – $150 | 15-20 | Typically 20-25 years |
Architectural Shingles | $150 – $300 | 25-30 | Typically 30-50 years |
Luxury Shingles | $300+ | 30+ | Typically lifetime or 50+ years |
Choosing the Right Asphalt Shingles
Selecting the appropriate asphalt shingles for your roof is a crucial decision impacting both the aesthetic appeal and longevity of your home. This involves considering various factors, including durability, visual appeal, cost, and the architectural style of your house. Making informed choices ensures a roof that is both beautiful and resilient.
Asphalt Shingle Types: Durability, Aesthetics, and Cost
Asphalt shingles are categorized into three main types: 3-tab, architectural (dimensional), and luxury shingles. 3-tab shingles are the most economical option, offering a simple, flat appearance. Architectural shingles, also known as dimensional shingles, provide a more textured, upscale look due to their layered design. Luxury shingles represent the premium tier, boasting superior durability, enhanced aesthetics (often mimicking natural materials like slate or wood), and a longer lifespan. The cost increases significantly as you move from 3-tab to architectural to luxury shingles, reflecting the enhanced materials and manufacturing processes. For example, a 3-tab shingle roof might cost $5,000-$8,000, while an architectural shingle roof could range from $8,000-$15,000, and a luxury shingle roof could easily exceed $15,000. These figures are estimates and vary based on roof size, labor costs, and regional factors.
Shingle Weight and Roof Lifespan, Asphalt shingle replacement
Shingle weight is a critical factor influencing the roof’s longevity and resilience against harsh weather conditions. Heavier shingles generally offer superior durability and wind resistance. They are less prone to damage from strong winds, hail, and heavy snow. The weight is usually expressed in pounds per square (a square being 100 square feet). While lighter shingles are less expensive, they may require more frequent replacements, ultimately increasing the overall cost over the long term. A heavier shingle, for instance, weighing 330 lbs per square, might offer a 20-30 year lifespan compared to a lighter shingle weighing 250 lbs per square which might last 15-20 years.
Asphalt Shingle Styles and Architectural Suitability
Various shingle styles cater to different architectural preferences. 3-tab shingles, with their simple design, are suitable for a wide range of homes, especially those with more traditional or modest styles. Architectural shingles, offering a more textured and dimensional appearance, complement contemporary, craftsman, and even some Victorian architectural styles. Luxury shingles, with their intricate designs and potential for mimicking natural materials, are ideal for high-end homes or those with distinct architectural features. The color and texture of the shingles also play a significant role in complementing the overall aesthetic of the house. For example, a dark-colored shingle might be more suitable for a modern home, while lighter colors might better suit a traditional home.
Visual Guide to Asphalt Shingle Types
A visual guide would depict three distinct shingle samples: one 3-tab, one architectural, and one luxury shingle.
* 3-Tab Shingle: This illustration would show a flat, rectangular shingle with three distinct tabs, clearly indicating its simple, uniform structure. The color would be a neutral tone, like gray or brown, to represent the typical color options available. The text would emphasize its affordability and basic appearance.
* Architectural Shingle: This illustration would showcase a thicker, more textured shingle with layered design elements, creating a three-dimensional effect. The illustration should highlight the shadow lines and depth created by the layering, contributing to a more visually interesting roof surface. The color could be a darker, richer tone, such as a deep brown or black, to reflect its more sophisticated aesthetic.
* Luxury Shingle: This would depict a highly detailed shingle, possibly mimicking slate or wood, with a complex layering and textural design. The illustration should emphasize the intricate detailing and realistic imitation of the natural material. The color palette could be wider, including options such as variegated browns or grays, simulating natural stone variations. The text would emphasize the superior quality and longevity of this shingle type. The visual representation would clearly differentiate the three types based on thickness, texture, and overall visual complexity.
The Asphalt Shingle Replacement Process
Replacing your asphalt shingles is a significant undertaking, but with careful planning and execution, it can be a smooth and successful process. This section Artikels the steps involved in a professional asphalt shingle replacement, from initial assessment to final cleanup, highlighting key considerations at each stage. Understanding this process will help you manage expectations and communicate effectively with your contractor.
Asphalt shingle replacement – The entire process involves a series of carefully coordinated steps, each critical to the longevity and performance of your new roof. From initial assessment to the final cleanup, attention to detail is paramount. This detailed guide will walk you through each phase, ensuring you are well-informed throughout the project.
Preparation and Assessment
Before any shingles are removed, a thorough assessment of the existing roof is crucial. This involves inspecting the roof decking for damage, checking the condition of the underlayment, and determining the overall structural integrity of the roof. This step is essential for identifying any potential issues that need to be addressed before the new shingles are installed. Accurate assessment prevents unforeseen delays and cost overruns.
- Roof Inspection: A detailed examination of the existing roof, including the shingles, decking, flashing, and ventilation. This helps determine the extent of the necessary repairs and the overall condition of the roofing system.
- Material Selection: Choosing the right asphalt shingles based on factors like budget, climate, and aesthetic preferences. Samples should be reviewed and a final decision made before beginning the installation.
- Permitting: Obtaining the necessary permits from local authorities, which is a legal requirement in most jurisdictions. This step ensures compliance with building codes and regulations.
Removal of Old Shingles
Careful and safe removal of the old asphalt shingles is the next step. This process requires attention to detail to avoid damaging the underlying roof deck. Proper disposal of the old shingles is also crucial for environmental responsibility.
- Shingle Removal: The old shingles are carefully removed, starting from the ridge and working down. Nails are removed, and any damaged decking is repaired or replaced.
- Debris Removal: All debris, including old shingles, nails, and other materials, is carefully removed from the roof and disposed of properly, often in accordance with local regulations.
- Deck Inspection: A thorough inspection of the roof deck is performed after shingle removal to identify any further damage that needs to be addressed before installing the new underlayment and shingles.
Underlayment Installation
Proper underlayment installation is critical for protecting the roof deck from moisture damage. It acts as a secondary water barrier, providing added protection even if the shingles are compromised. Different types of underlayment offer varying levels of protection and should be selected based on the specific needs of the roof.
- Underlayment Selection: Choosing the appropriate type of underlayment based on factors such as climate, roof pitch, and budget. Options include felt paper, synthetic underlayment, and ice and water shield.
- Installation: The underlayment is carefully installed, overlapping each sheet to ensure complete coverage. Proper fastening is essential to prevent movement or tearing.
- Flashing Installation: Flashing around chimneys, vents, and other penetrations is installed to prevent water leakage. This is a crucial step in ensuring the long-term performance of the roof.
New Shingle Installation
The installation of new asphalt shingles is a precise process requiring skilled labor and attention to detail. Proper shingle alignment and nailing are essential for a long-lasting, leak-free roof. Following manufacturer’s instructions is paramount.
- Starting Course: The installation begins with the starter course, which provides a level base for the subsequent shingle layers.
- Shingle Layering: Shingles are applied in overlapping rows, ensuring proper alignment and nailing. The manufacturer’s instructions should be followed precisely for optimal performance.
- Ridge Cap Installation: The ridge cap is installed to protect the ridge from the elements. This is the final layer of shingles and completes the roof covering.
Final Cleanup
After the new shingles are installed, a thorough cleanup is essential to remove any debris left behind. This ensures a safe and aesthetically pleasing finish to the project.
- Debris Removal: All remaining debris, including nails, shingle scraps, and other materials, is carefully removed from the roof and the surrounding area.
- Site Inspection: A final inspection is performed to ensure that all work has been completed to the required standards and that there are no remaining issues.
Necessary Tools and Equipment
Professional asphalt shingle replacement requires specialized tools and equipment to ensure efficiency and safety. These tools enable accurate and effective installation, contributing to a long-lasting roof.
- Safety Equipment: Hard hats, safety glasses, gloves, and fall protection equipment are essential for worker safety.
- Roofing Tools: These include roofing hammers, shingle cutters, utility knives, measuring tapes, chalk lines, and roofing nails.
- Lifting Equipment: For heavier materials, equipment like scaffolding, ladders, and possibly a crane may be necessary depending on the size and complexity of the roof.
Finding and Hiring a Contractor
Replacing your asphalt shingles is a significant investment, and choosing the right contractor is crucial for a successful and long-lasting result. This section will guide you through the process of finding, vetting, and hiring a qualified professional for your asphalt shingle replacement project. Careful consideration at this stage will save you time, money, and potential headaches down the line.
Finding a reputable contractor requires diligent research and due diligence. It’s not simply about finding the cheapest option; it’s about finding a contractor with the necessary skills, experience, and licensing to complete the job correctly and efficiently.
Contractor Selection Methods
Several avenues exist for finding potential contractors. Online directories, such as those provided by the Better Business Bureau or Angie’s List, offer reviews and ratings from previous clients. Local home improvement stores often maintain lists of recommended contractors. Word-of-mouth referrals from trusted friends, family, or neighbors can also be invaluable. Finally, checking with your local building department can help identify licensed and insured contractors operating in your area. Thorough research increases the likelihood of finding a reliable and competent contractor.
The Importance of Multiple Bids
Obtaining multiple bids from different contractors is essential. This allows for a fair comparison of pricing, services offered, and overall project approach. Comparing bids highlights discrepancies in pricing and reveals potential overcharges or hidden costs. It also allows you to evaluate the level of detail and professionalism in each contractor’s bid proposal. For example, one contractor might offer a detailed breakdown of materials and labor costs, while another might provide a single lump sum, making it difficult to assess value. By comparing bids, you can make an informed decision based on both price and quality.
Key Questions to Ask Potential Contractors
Before committing to a contractor, several key questions should be asked. These questions address crucial aspects of the project, including licensing, insurance, experience, and warranty. For instance, inquiring about their licensing and insurance ensures they are legally operating and financially responsible. Asking about their experience with similar projects helps assess their expertise. Clarifying their warranty provisions protects your investment in case of future issues. Asking about their project timeline provides a realistic expectation of the project’s duration. Finally, discussing their cleanup procedures ensures a clean and safe work environment throughout the project.
Contractor Qualification Checklist
A comprehensive checklist should be used to evaluate potential contractors. This checklist should include verification of licensing and insurance, checking for positive online reviews and references, reviewing their experience with similar projects, and confirming their adherence to local building codes. In addition, verifying their warranty offerings, ensuring they have proper liability insurance, and confirming their adherence to safety regulations are essential steps. Finally, obtaining a detailed written contract outlining the scope of work, payment schedule, and project timeline protects your interests and ensures clarity throughout the project. This thorough approach helps ensure the selection of a contractor capable of delivering a high-quality, safe, and compliant asphalt shingle replacement.
Understanding Warranties and Guarantees
Choosing the right asphalt shingles and contractor involves careful consideration of warranties and guarantees. These crucial elements protect your investment and provide recourse should problems arise with the materials or workmanship. Understanding the different types of warranties available and their implications is essential for making informed decisions.
Asphalt shingle manufacturers offer various warranties, primarily focusing on the shingle’s lifespan and performance. These warranties typically cover defects in materials and workmanship, but the specifics vary greatly. Contractor warranties, on the other hand, cover the installation itself, ensuring the job is done correctly and according to industry standards. Both types of warranties are vital for protecting your investment.
Types of Asphalt Shingle Warranties
Manufacturer warranties for asphalt shingles commonly fall into two categories: limited and full. A limited warranty covers defects in materials and manufacturing for a specified period, often 20-30 years. A full warranty, while less common, offers more comprehensive coverage, potentially including labor costs for repairs or replacements. The warranty’s terms and conditions, including the definition of “defect” and the process for filing a claim, should be carefully reviewed before purchasing. For instance, a limited warranty might only cover the cost of the shingles themselves, while a full warranty might cover both materials and labor. Some warranties may also have prorated coverage, meaning the manufacturer’s responsibility decreases over time.
Understanding Warranty Terms and Conditions
Before committing to a purchase, meticulously examine the warranty document. Pay close attention to the duration of coverage, what is and isn’t covered (e.g., wind damage, hail damage, algae growth), the process for filing a claim, and any exclusions or limitations. Understanding these aspects will prevent future misunderstandings and disputes. For example, a warranty might explicitly exclude damage caused by improper installation, emphasizing the importance of choosing a qualified and reputable contractor. Similarly, certain environmental conditions might void parts of the warranty.
Contractor Warranties and Guarantees
Reputable contractors typically offer warranties on their workmanship, covering issues resulting from faulty installation. These warranties often span several years and ensure the contractor will rectify any problems related to their work, such as leaks or premature shingle failure. It’s essential to obtain a written warranty from the contractor, clearly outlining the scope of coverage, duration, and the process for submitting a claim. For instance, a contractor’s warranty might cover leaks for five years, but exclude damage caused by unforeseen circumstances like a tree falling on the roof.
Filing a Warranty Claim
The process for filing a warranty claim varies depending on the manufacturer and contractor. Generally, it involves documenting the damage with photographs and contacting the relevant party (manufacturer or contractor) to initiate the claim. The warranty document will provide specific instructions on the required documentation and the claim submission process. Thorough documentation is crucial for a successful claim, and it’s advisable to keep copies of all correspondence and documentation related to the claim. Delays can occur in processing claims, so it is important to be patient and persistent in following up.
Maintenance and Lifespan of Asphalt Shingles
Proper maintenance significantly extends the lifespan of your asphalt shingle roof, saving you money and hassle in the long run. Regular inspections and proactive care can prevent minor issues from escalating into costly repairs or premature replacements. Understanding the factors influencing shingle longevity allows for informed decisions regarding maintenance and future replacements.
Regular maintenance helps to prevent premature deterioration and extends the life of your asphalt shingles. This involves both routine visual inspections and occasional more thorough checks. Neglecting maintenance can lead to accelerated damage and significantly shorten the lifespan of your roof.
Factors Affecting Asphalt Shingle Lifespan
Several factors influence how long your asphalt shingles will last. These include the quality of the shingles themselves, the climate in your region, and the quality of installation. Understanding these factors helps in making informed decisions about shingle selection and maintenance.
- Shingle Quality: Higher-quality shingles, typically indicated by thicker construction and better materials, tend to have longer lifespans. For example, architectural shingles, with their thicker construction and layered design, often outlast standard three-tab shingles.
- Climate: Extreme weather conditions, such as intense sun, heavy snow, or frequent hail, can significantly reduce the lifespan of asphalt shingles. Areas with harsh winters might see more rapid deterioration due to ice damming and freeze-thaw cycles. Coastal regions may experience more damage from salt spray.
- Installation Quality: Proper installation is crucial for shingle longevity. Improper nailing, inadequate ventilation, or poor flashing around chimneys and vents can lead to premature shingle failure. A well-installed roof will protect your home effectively and last longer.
- Tree Overhang: Overhanging tree branches can trap moisture and debris on your roof, accelerating shingle deterioration. Regular trimming of overhanging branches is important for roof health.
Signs of Damage and Wear
Recognizing signs of damage early allows for timely repairs, preventing more extensive and costly problems. Regular inspections are key to identifying these issues.
- Missing or Damaged Shingles: Missing or severely damaged shingles are obvious signs requiring immediate attention. These expose the underlying roofing felt and structure to the elements, leading to leaks and further damage.
- Granule Loss: Noticeable granule loss, leaving exposed shingle material, indicates wear and tear. This reduces the shingles’ ability to reflect sunlight and resist moisture damage, leading to premature aging.
- Curling or Cupping Shingles: Shingles curling upwards at the edges (cupping) or downwards (curling) are signs of moisture damage or improper installation. This reduces their weather resistance and aesthetic appeal.
- Algae or Moss Growth: The presence of algae or moss indicates excessive moisture retention, often due to poor ventilation or shading. This can weaken the shingles and lead to deterioration.
- Leaks: Water stains on ceilings or walls are clear indications of roof leaks, requiring immediate attention and repair.
Maintaining Asphalt Shingles to Extend Lifespan
Proactive maintenance can significantly extend the life of your asphalt shingles. A few simple steps can make a big difference.
Regularly inspect your roof, at least twice a year, after leaf fall and before the start of winter, to check for damage. Remove debris such as leaves, branches, and pine needles to prevent moisture buildup. Clean algae and moss growth using a suitable cleaning solution, following manufacturer’s instructions. Proper ventilation is crucial to prevent moisture buildup, so ensure your attic has adequate ventilation. Consider addressing any damaged shingles promptly, even small repairs, before they worsen. Regular trimming of overhanging branches minimizes the risk of damage from falling debris and moisture retention.
Environmental Considerations: Asphalt Shingle Replacement
Replacing your asphalt shingles presents an opportunity to consider the environmental impact of your roofing choices. Asphalt shingle manufacturing and disposal both contribute to environmental concerns, but responsible choices can mitigate these effects. Understanding these impacts allows for more informed decisions, leading to a greener roofing solution.
Asphalt shingles, while a common and cost-effective roofing material, have a significant environmental footprint. Their production involves the extraction and processing of raw materials, including asphalt (a petroleum product), fiberglass, and mineral fillers. These processes consume energy and release greenhouse gases, contributing to climate change. Furthermore, the manufacturing process can generate air and water pollution. At the end of their lifespan, discarded asphalt shingles often end up in landfills, occupying valuable space and potentially leaching harmful substances into the environment. The sheer volume of discarded shingles annually adds to the overall waste management challenge.
Eco-Friendly Asphalt Shingle Options
Several manufacturers are now producing asphalt shingles with improved environmental profiles. These options often incorporate recycled materials in their composition, reducing the demand for virgin resources. Some shingles utilize recycled rubber or plastic, diverting waste from landfills and lowering the overall carbon footprint. Additionally, some manufacturers focus on improving energy efficiency by incorporating reflective granules that reduce the amount of heat absorbed by the roof, thus lowering cooling costs and reducing energy consumption. These “cool roof” shingles can contribute to a smaller carbon footprint over the shingle’s lifetime. It is important to research manufacturers’ claims and look for certifications from reputable environmental organizations to verify the environmental benefits of specific products. Examples of such certifications include those provided by organizations focusing on sustainable building materials.
Proper Disposal of Old Shingles
The proper disposal of old asphalt shingles is crucial for minimizing environmental impact. Simply discarding them in a landfill should be avoided whenever possible. Many communities offer recycling programs specifically for roofing materials. These programs often involve the processing of old shingles into useful products, such as asphalt pavement. Alternatively, some contractors offer shingle removal and recycling services. In some cases, old shingles can be repurposed for other applications, such as landscaping features (although this should be done cautiously, considering potential leaching concerns). Researching local recycling options and responsible disposal methods is a key step in minimizing the environmental impact of your roofing replacement project. The responsible handling of discarded shingles reduces landfill waste and contributes to a more sustainable roofing practice.
Safety Precautions During Replacement
Asphalt shingle replacement is a potentially hazardous undertaking, requiring careful attention to safety for both homeowners and contractors. Neglecting safety protocols can lead to serious injuries, property damage, and legal liabilities. This section details essential safety measures to ensure a safe and successful project.
Roof work inherently involves significant risks, primarily due to working at heights. Falls are the most common and severe hazard. Other dangers include exposure to the elements, sharp objects, and potential electrical hazards. Proper planning and the consistent use of appropriate safety equipment are paramount to mitigate these risks.
Personal Protective Equipment (PPE)
The use of personal protective equipment (PPE) is non-negotiable for all individuals involved in asphalt shingle replacement. This equipment protects against various hazards and significantly reduces the risk of injury.
- Hard Hats: Essential to protect against falling objects, such as shingles, tools, or debris.
- Safety Harness and Lanyard: A crucial safety measure for working at heights, preventing falls from the roof. The lanyard should be secured to a suitable anchor point.
- Safety Glasses or Goggles: Protect eyes from flying debris, dust, and UV radiation.
- Gloves: Protect hands from cuts, abrasions, and chemical exposure from asphalt shingles and other materials.
- Work Boots with Steel Toes: Protect feet from falling objects and sharp materials.
- Hearing Protection: Reduce exposure to loud noises from power tools.
- Fall Arrest System: This system, including a harness, lanyard, and anchor point, is crucial for preventing falls from significant heights. Regular inspections are essential to ensure functionality.
Roof Access and Work Procedures
Safe access to the roof and established work procedures are critical for minimizing risks. Improper access or unsafe practices can quickly lead to accidents.
- Stable Ladders and Scaffolding: Ladders should be properly positioned, secured, and extended at least three feet above the roofline. Scaffolding should be erected according to manufacturer’s instructions and inspected regularly for stability.
- Designated Work Areas: Clearly defined work areas help prevent collisions and ensure efficient movement on the roof.
- Controlled Material Handling: Shingles and other materials should be carefully handled and stacked to prevent falls or slips. Use appropriate lifting techniques to avoid strains or injuries.
- Weather Conditions: Work should be postponed in adverse weather conditions, such as strong winds, rain, snow, or ice, to prevent falls and ensure safety.
- Communication: Clear communication between workers is vital, especially when working at heights or using power tools.
Electrical Hazards
Contact with power lines is a serious and potentially fatal hazard. Precautions must be taken to avoid any contact with electrical wiring during roof work.
- Identify Power Lines: Before commencing work, carefully identify and mark the location of all overhead power lines. Maintain a safe distance from these lines at all times.
- Call Utility Companies: Contact utility companies to request temporary de-energization of power lines if necessary. This should be done well in advance of the work commencement.
- Use Non-Conductive Tools: Use tools with insulated handles to avoid electrical shocks.
Homeowner Responsibilities
Homeowners also play a crucial role in ensuring a safe working environment. Their cooperation and understanding of safety protocols are essential.
- Clear the Work Area: Remove any obstructions from the roof and surrounding areas that could create tripping hazards or interfere with the work.
- Inform Neighbors: Notify neighbors about the upcoming roof work to avoid any misunderstandings or concerns.
- Supervise Children and Pets: Keep children and pets away from the work area to prevent accidents.
- Provide Access to Water and Rest Areas: Ensure the contractors have access to water and shaded rest areas, especially during hot weather.
Permitting and Legal Requirements
Replacing your asphalt shingles often necessitates navigating a landscape of permits and legal requirements. Understanding these regulations ensures compliance with local laws, protects your investment, and prevents potential legal issues down the line. Failure to obtain necessary permits can result in fines or even the forced removal of the new roof.
The specific permits and inspections required for asphalt shingle replacement vary significantly depending on your location. These differences stem from local building codes, zoning ordinances, and environmental regulations. Generally, however, most jurisdictions require some form of permit before work commences. This is primarily to ensure the work is done to code and meets safety standards. Additionally, inspections are often scheduled at various stages of the project to verify compliance.
Permitting Processes
Securing the necessary permits usually involves submitting an application to your local building department or planning office. This application typically requires detailed information about the project, including the scope of work, materials to be used, and the contractor’s license information. You may need to provide architectural drawings or plans depending on the complexity of the project. After the application is reviewed and approved, the permit is issued, authorizing the commencement of work. Throughout the process, expect inspections at key stages such as after the removal of the old shingles, during the installation of the underlayment, and finally, after the completion of the new shingle installation. Failure to pass these inspections can result in delays and potential additional costs.
Legal Requirements for Roofing Work
Legal requirements for roofing work extend beyond simply obtaining permits. Contractors are usually required to hold specific licenses and insurance. This protects homeowners from liability in case of accidents or faulty workmanship. It is crucial to verify that your chosen contractor possesses all necessary licenses and insurance before commencing work. Furthermore, many jurisdictions have regulations regarding waste disposal and the proper handling of hazardous materials, such as old asphalt shingles containing asbestos. Understanding and adhering to these regulations is crucial for both legal compliance and environmental responsibility. It’s advisable to research your local and state laws concerning proper disposal of roofing materials.
Resources for Obtaining Permits and Complying with Regulations
Your local building department or planning office is the primary resource for obtaining information about necessary permits and regulations. Their website often provides detailed information on the application process, required documentation, and associated fees. Additionally, you can contact them directly via phone or in person to ask specific questions and obtain clarification. State and regional government websites also provide valuable information regarding building codes and regulations. Furthermore, many professional roofing associations offer guidance and resources for both homeowners and contractors regarding best practices and legal compliance. Consulting with an experienced roofing contractor can also be beneficial as they are familiar with the local permitting process and regulations.
Common Queries
How long does asphalt shingle replacement typically take?
The timeframe varies depending on roof size and complexity, but generally ranges from a few days to a couple of weeks.
Can I replace shingles myself?
While possible for smaller repairs, complete shingle replacement is best left to professionals due to safety and expertise required.
What is the best time of year for asphalt shingle replacement?
Spring and fall generally offer the best weather conditions for roofing work, avoiding extreme heat or cold.
How often should I inspect my asphalt shingles?
At least twice a year, after fall leaf drop and in the spring, is recommended to check for damage.