Types of Rigid Roof Insulation
Choosing the right rigid insulation for your roof is crucial for energy efficiency and long-term cost savings. Several materials offer excellent thermal performance, but their properties vary significantly in terms of cost, lifespan, and environmental impact. Understanding these differences will help you make an informed decision.
Best rigid insulation for roof – This section provides a detailed comparison of common rigid insulation materials, focusing on their thermal performance, cost, lifespan, and environmental considerations. We will examine polyurethane, polyisocyanurate, extruded polystyrene (XPS), and expanded polystyrene (EPS) to illustrate the key differences between these options.
Rigid Insulation Material Properties
The following table summarizes the key properties of common rigid roof insulation materials. R-value represents the material’s resistance to heat flow, with higher values indicating better insulation. Note that R-values can vary depending on the thickness of the insulation board.
Material | R-value per inch (approximate) | Thermal Performance | Typical Lifespan (years) |
---|---|---|---|
Polyurethane (PU) | 6-7 | Excellent; high R-value per inch, good moisture resistance. | 30-50+ |
Polyisocyanurate (PIR) | 6-8 | Excellent; higher R-value than PU, good moisture resistance, often faced with foil for added reflectivity. | 30-50+ |
Extruded Polystyrene (XPS) | 4-7 | Good; high compressive strength, moisture resistant, suitable for below-grade applications. | 50+ |
Expanded Polystyrene (EPS) | 3-4 | Fair; lower R-value, less moisture resistant than XPS, less compressive strength. | 20-30 |
Cost, Lifespan, and Environmental Impact Comparison
The following table provides a comparative overview of cost, lifespan, and environmental impact. Note that costs can vary significantly depending on location, supplier, and thickness of the insulation. Environmental impact considers manufacturing processes, embodied carbon, and recyclability.
Material | Cost (Relative) | Lifespan (years) | Environmental Impact (Relative) |
---|---|---|---|
Polyurethane (PU) | High | 30-50+ | Moderate; some concerns regarding blowing agents used in manufacturing. |
Polyisocyanurate (PIR) | High | 30-50+ | Moderate; similar concerns to PU regarding blowing agents. |
Extruded Polystyrene (XPS) | Medium | 50+ | Low; generally considered more environmentally friendly than PU and PIR. |
Expanded Polystyrene (EPS) | Low | 20-30 | Low to moderate; recyclable, but lower R-value leads to increased energy consumption over its lifespan. |
Cellular Structure Visualization
The differences in thermal performance are partly due to variations in cellular structure. Imagine four magnified views of each insulation type:
Polyurethane (PU) and Polyisocyanurate (PIR): These would show a closed-cell structure with small, tightly packed cells. This minimizes air pockets and significantly reduces heat transfer. PIR often shows a slightly more uniform cell structure than PU.
Extruded Polystyrene (XPS): This would display a closed-cell structure, but with slightly larger cells than PU or PIR. This results in a slightly lower R-value per inch compared to the other two, but still offers good thermal performance and excellent moisture resistance.
Expanded Polystyrene (EPS): This would depict an open-cell structure with larger, less uniformly sized cells and more air gaps. This contributes to its lower R-value and greater susceptibility to moisture absorption compared to closed-cell options.
R-Value and Energy Efficiency
R-value is a crucial factor in determining the effectiveness of roof insulation and its impact on energy consumption. A higher R-value indicates greater resistance to heat flow, meaning less heat escapes in winter and less heat enters in summer. This directly translates to significant energy savings and improved comfort within the home. Understanding the relationship between R-value and energy efficiency is key to making informed decisions when choosing insulation for your roof.
The relationship between R-value and energy savings is directly proportional. For every increase in R-value, you can expect a corresponding reduction in energy loss through the roof. This translates to lower heating and cooling bills, reduced reliance on HVAC systems, and a smaller carbon footprint. The exact savings will depend on several factors, including the climate, the existing insulation level, and the efficiency of the heating and cooling systems.
Climate Zone Influence on Optimal R-Value
Different climate zones necessitate different optimal R-values for roof insulation. Colder climates with long, harsh winters require significantly higher R-values to minimize heat loss. Conversely, warmer climates with hot summers may benefit from a lower R-value to reduce the heat gain from the sun. For example, a home in a northern state like Minnesota might benefit from an R-value of R-60 or higher, while a home in southern California might be adequately insulated with an R-38. Building codes often provide minimum R-value requirements based on the specific climate zone. Ignoring these recommendations can lead to higher energy bills and reduced comfort.
Examples of Increased R-Value Impact on Heating and Cooling Costs
Consider a hypothetical scenario: A house with R-13 insulation in the attic experiences an average annual heating and cooling cost of $1500. Upgrading the insulation to R-49 could reduce these costs by approximately 30-40%, resulting in annual savings of $450-$600. This savings is a result of significantly reduced heat transfer through the roof. Similarly, a home in a hotter climate might see a considerable reduction in cooling costs by increasing insulation from R-30 to R-49, potentially lowering the annual cooling bill by 20-30%. These figures are illustrative and will vary depending on factors like the size of the house, the efficiency of the HVAC system, and the climate. However, they demonstrate the potential for significant cost savings associated with improved insulation.
Installation Methods and Best Practices
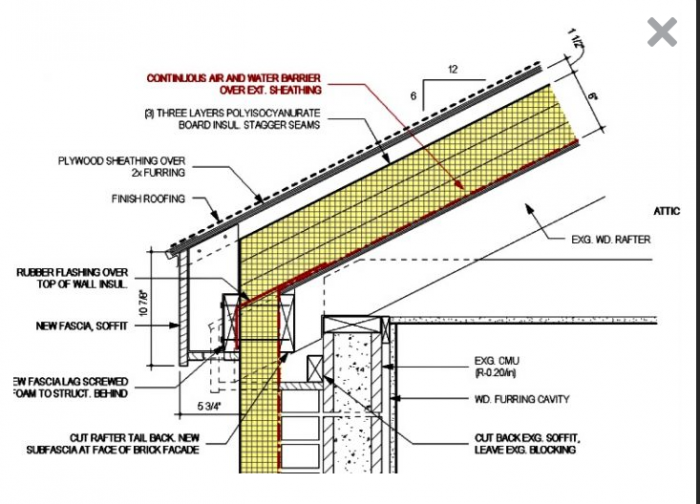
Proper installation of rigid foam roof insulation is crucial for maximizing its energy-saving potential and ensuring the longevity of your roof system. This involves careful consideration of several factors, including the type of roof, the climate, and the specific characteristics of the insulation itself. Following best practices will minimize thermal bridging, prevent moisture problems, and contribute to a more energy-efficient building envelope.
Successful rigid foam insulation installation requires attention to detail and adherence to manufacturer’s instructions. This section will Artikel general procedures and best practices applicable to various roof types, emphasizing the importance of vapor barriers and air sealing to create a continuous, high-performance insulation layer.
Installing Rigid Insulation on Flat Roofs
Installing rigid foam insulation on flat roofs generally involves adhering the boards directly to the roof deck. This process typically begins with a thorough cleaning of the roof surface to ensure proper adhesion. The insulation boards should be laid out in a staggered pattern, similar to bricklaying, to minimize gaps and maximize thermal performance. For larger flat roofs, using a mechanical fastening system in conjunction with adhesive may be necessary to secure the insulation against wind uplift. After the insulation is installed, a robust vapor barrier is crucial, followed by the final roofing membrane. Careful attention must be paid to sealing all seams and penetrations to prevent air leakage.
Installing Rigid Insulation on Sloped Roofs
Installing rigid foam insulation on sloped roofs requires a slightly different approach. The insulation can be installed either between rafters (in a retrofit application) or over the rafters (in new construction). When installing between rafters, ensure a tight fit to minimize gaps. For installations over rafters, the process resembles that of flat roofs, requiring attention to proper fastening and sealing. Regardless of the approach, appropriate vapor barrier installation is essential to prevent moisture damage and ensure optimal thermal performance. Consider using tapered insulation boards to create a smooth surface for the final roofing layer on sloped roofs.
Minimizing Thermal Bridging
Thermal bridging occurs when heat flows easily through areas of higher thermal conductivity, such as metal framing members. This reduces the overall R-value of the insulation system and increases energy loss. To minimize thermal bridging on both flat and sloped roofs, it’s important to ensure continuous insulation with minimal gaps. Using rigid foam boards that completely cover framing members, or incorporating additional insulation around framing elements, can significantly reduce thermal bridging. Careful attention to sealing around penetrations such as vents and pipes is also vital. For sloped roofs, using continuous insulation over the rafters is more effective in minimizing thermal bridging compared to installing insulation between the rafters.
Vapor Barrier and Air Sealing Best Practices
A continuous and properly installed vapor barrier is essential to prevent moisture from entering the insulation and causing damage. The vapor barrier should be installed on the warm side of the insulation, usually on the interior side of the roof in most climates. All seams and penetrations in the vapor barrier must be carefully sealed with appropriate tape or sealant to ensure a continuous barrier. Air sealing is equally important; any gaps or cracks in the insulation or vapor barrier can lead to air leakage and reduced energy efficiency. Air sealing should be addressed throughout the installation process, paying attention to areas around windows, doors, and other penetrations. Consider using caulk, expanding foam, or weatherstripping to seal gaps.
Factors Affecting Insulation Choice
Selecting the best rigid insulation for your roof involves more than just considering R-value. Several crucial factors influence the optimal choice, ensuring both energy efficiency and long-term building performance. These factors interact, and careful consideration of each is vital for a successful installation.
Several key factors significantly impact the selection of rigid roof insulation. Understanding these factors ensures that the chosen insulation not only meets energy efficiency goals but also aligns with the specific needs and constraints of the project.
Roof Design and Climate
Roof design plays a crucial role in insulation selection. Steeply pitched roofs, for example, might benefit from different insulation types compared to flat roofs due to variations in airflow and potential for moisture accumulation. Climate significantly impacts the required R-value. Colder climates demand higher R-values to minimize heat loss, while hotter climates necessitate insulation that effectively reflects solar radiation and reduces heat gain. For instance, a home in Alaska would require a significantly higher R-value than a home in Florida. The specific climate data, including average temperatures, snowfall, and humidity levels, should inform the choice of insulation thickness and type. This ensures the insulation adequately protects the building from extreme temperatures and moisture ingress.
Budget and Building Code Requirements
Budgetary constraints often influence the choice of insulation. Higher R-value insulation typically costs more upfront, but the long-term energy savings can outweigh the initial investment. Building codes dictate minimum R-value requirements based on location and climate zone. Understanding these regulations is essential to ensure compliance and avoid potential penalties. For example, many regions have specific codes for attic insulation, requiring a minimum R-value to meet energy efficiency standards. Balancing budget with code requirements necessitates careful planning and potentially exploring different insulation options to find the most cost-effective solution that meets all regulatory needs.
Long-Term Maintenance Considerations
The longevity and maintenance requirements of different insulation types should be factored into the decision. Some insulation materials are more susceptible to moisture damage or degradation over time than others. Insulation with a high moisture resistance rating is preferable in areas prone to high humidity or potential leaks. Choosing durable, low-maintenance insulation minimizes the need for future repairs or replacements, reducing overall lifecycle costs. For example, closed-cell spray foam insulation, known for its high moisture resistance, might be a better choice for coastal regions prone to moisture than fiberglass batts. Regular inspection and maintenance are still recommended regardless of the chosen insulation.
Fire Resistance
Fire safety is paramount, and the fire resistance rating of insulation is a crucial factor. Insulation materials have varying fire performance characteristics, typically rated using a Class A, B, or C classification, with Class A representing the highest level of fire resistance. Building codes often specify minimum fire resistance requirements for roof insulation, especially in areas with stringent fire safety regulations. Selecting insulation with appropriate fire resistance ratings not only protects the building from fire damage but also contributes to overall occupant safety. For example, a commercial building might require a higher fire-resistance rated insulation than a residential dwelling, reflecting the increased risk and stricter safety regulations.
Moisture Management and Preventing Damage
Protecting your rigid roof insulation from moisture is crucial for maintaining its thermal performance and the longevity of your roof system. Moisture can lead to significant problems, including reduced R-value, mold growth, structural damage, and premature insulation failure. Proper ventilation and the implementation of effective waterproofing measures are key to preventing these issues.
Proper ventilation is paramount in preventing moisture damage to rigid roof insulation. Moisture accumulation within the roof assembly can occur due to several factors, including condensation from warm, moist interior air meeting colder roof surfaces, and the infiltration of outside moisture through leaks or inadequate flashing. Effective ventilation creates an airflow that removes this moisture, preventing it from saturating the insulation and causing damage. This airflow helps to equalize temperatures across the roof assembly, reducing the likelihood of condensation. Without adequate ventilation, trapped moisture can lead to significant deterioration of the insulation, compromising its effectiveness and potentially causing structural damage to the roof deck.
Ventilation Strategies for Rigid Roof Insulation
Effective ventilation requires a balanced approach, ensuring both intake and exhaust airflow. Intake vents, often located at the soffit level, allow outside air to enter the roof cavity. Exhaust vents, usually positioned at the ridge or peak of the roof, allow the moist air to escape. The size and placement of these vents are critical and should be determined based on the specific characteristics of the roof and climate. Properly sized vents ensure sufficient airflow to prevent moisture buildup, while poorly designed or insufficient ventilation can lead to moisture accumulation and damage. Consideration should also be given to the type of insulation used, as some materials are more susceptible to moisture damage than others. For example, closed-cell spray foam insulation, due to its low permeability, is less susceptible to moisture intrusion compared to open-cell foam or fiberglass.
Protecting Rigid Insulation from Water Damage During and After Installation
Protecting rigid insulation from water damage during and after installation is essential to preserving its performance and extending the lifespan of the roof system. Several measures can be employed to achieve this. During installation, careful handling and protective covering of the insulation boards are vital. The use of waterproof sheeting or tarps to cover the insulation while other roofing work is being completed is a recommended practice. This prevents rain or snow from directly contacting the insulation, which can lead to water absorption and damage. After installation, ensuring proper sealing around penetrations (such as chimneys, vents, and skylights) is crucial to prevent water leakage. High-quality sealant should be used to create a waterproof barrier around these areas. Regular roof inspections after installation are also recommended to identify and address any potential leaks or damage promptly. Early detection of moisture problems can prevent extensive damage and costly repairs.
Vapor Barrier System Selection, Best rigid insulation for roof
The selection of a suitable vapor barrier system is a critical aspect of moisture management in a roof system with rigid insulation. A vapor barrier acts as a control layer, preventing the movement of moisture vapor from the interior of the building into the insulation and roof assembly. The choice of vapor barrier depends on several factors, including the climate, the type of insulation used, and the construction of the roof. In humid climates, a highly impermeable vapor barrier is often preferred to prevent excessive moisture from entering the insulation. In drier climates, a more breathable vapor barrier might be suitable. The vapor barrier should be installed correctly, ensuring it is continuous and free of any gaps or tears. Improper installation can negate the effectiveness of the vapor barrier, leading to moisture problems. Common vapor barrier materials include polyethylene sheeting, foil-faced insulation, and specialized vapor-retarding paints. The selection should be made in consultation with a qualified roofing professional to ensure it aligns with the specific needs of the building and the climate.
Long-Term Performance and Durability
The longevity and effectiveness of rigid roof insulation are crucial for maintaining a building’s energy efficiency and structural integrity over its lifespan. Several factors influence the long-term performance and durability of different rigid insulation materials, impacting their ability to withstand environmental stressors and retain their insulating properties. Understanding these factors is vital for making informed choices during the construction or renovation process.
Several factors significantly affect the long-term performance and lifespan of rigid roof insulation. These include the material’s inherent properties, exposure to environmental conditions, and the quality of installation. For example, some materials are inherently more resistant to moisture absorption and degradation than others, directly influencing their lifespan. Similarly, proper installation, minimizing gaps and ensuring a good seal, is crucial to preventing premature deterioration.
UV Exposure and Environmental Impact on Insulation
Exposure to ultraviolet (UV) radiation from sunlight is a major factor affecting the long-term performance of many rigid insulation materials. UV radiation can degrade the surface of the insulation, causing it to become brittle, crack, and lose its insulating properties. This degradation is particularly noticeable in materials that lack UV stabilizers, which are additives that protect the material from the damaging effects of UV radiation. For example, exposed polyurethane foam insulation is known to be susceptible to UV degradation, leading to a reduction in R-value over time. In contrast, some polyisocyanurate (polyiso) foams are formulated with UV-resistant coatings, mitigating this issue. Other environmental factors such as extreme temperature fluctuations, wind, rain, and snow can also contribute to the weathering and degradation of rigid insulation, particularly affecting its physical integrity and leading to potential moisture penetration. The impact varies depending on the material’s properties and the severity of the climate.
Durability Comparison of Rigid Insulation Materials
Different rigid insulation materials exhibit varying levels of durability under various weather conditions. Expanded polystyrene (EPS) foam, for example, is relatively lightweight and easy to handle, but it is susceptible to damage from physical impacts and can be more prone to moisture absorption compared to other materials. Extruded polystyrene (XPS) foam offers better resistance to moisture and compression, making it a more durable choice for applications where these factors are critical. Polyisocyanurate (polyiso) foam often incorporates a facer layer that provides additional protection against UV radiation and moisture, enhancing its durability compared to other options. However, even polyiso can experience degradation over an extended period, especially if the facer is damaged. Mineral wool insulation, while less susceptible to UV degradation, can be more vulnerable to moisture absorption if not properly protected by a vapor barrier. The choice of material, therefore, depends on the specific climatic conditions and the desired lifespan of the insulation system. For example, in regions with intense UV radiation and frequent rainfall, polyiso with a high-quality facer might be a preferred choice over EPS foam.
Sustainability and Environmental Impact
Choosing rigid roof insulation involves considering not only its thermal performance but also its environmental impact throughout its entire lifecycle. From manufacturing to disposal, each material carries a different environmental footprint, influencing a building’s overall sustainability. Understanding these impacts is crucial for making informed decisions that minimize the building’s carbon footprint and promote environmentally responsible construction practices.
The environmental impact of rigid insulation materials varies significantly depending on their composition and manufacturing processes. Factors such as embodied carbon, recyclability, and the energy consumed during production all contribute to the overall environmental burden. Minimizing these impacts is essential for achieving sustainable building practices and reducing the overall environmental footprint of the construction industry.
Embodied Carbon in Rigid Insulation Materials
The embodied carbon of a building material represents the total greenhouse gas emissions associated with its extraction, manufacturing, transportation, and installation. Different rigid insulation materials exhibit varying levels of embodied carbon. For example, extruded polystyrene (XPS) insulation generally has a higher embodied carbon footprint compared to polyisocyanurate (polyiso) due to the energy-intensive manufacturing process involving the use of blowing agents. Conversely, materials like mineral wool, derived from natural resources, often exhibit lower embodied carbon footprints, particularly when produced with recycled content. The choice of insulation material can significantly impact the overall carbon footprint of a building, with lower embodied carbon options contributing to a more sustainable outcome. Life cycle assessments (LCAs) provide a comprehensive evaluation of the embodied carbon for various insulation types, enabling informed comparisons and selection.
Recyclability and End-of-Life Management
The recyclability of rigid insulation materials is another crucial factor in assessing their environmental impact. Some materials, like mineral wool, are more readily recyclable than others. XPS and polyiso insulation, while less readily recyclable in many regions, are increasingly being incorporated into recycling streams through innovative technologies and partnerships with recycling facilities. The availability of recycling programs for specific insulation materials will influence their environmental impact at the end of the building’s lifespan. Choosing insulation with higher recyclability rates contributes to reducing landfill waste and conserving natural resources. Furthermore, the development and implementation of effective end-of-life management strategies are critical for minimizing the environmental burden of discarded insulation materials.
Eco-Friendly Rigid Insulation Options
Several eco-friendly rigid insulation options are available in the market, catering to diverse sustainability goals. These options often incorporate recycled content, utilize renewable resources, and demonstrate lower embodied carbon footprints compared to traditional alternatives. Examples include insulation made from recycled denim, which transforms waste material into a valuable building product, or insulation manufactured with bio-based polyols, derived from renewable sources such as plants. These materials showcase the potential for innovation in the insulation industry to reduce the environmental impact of buildings. Furthermore, the selection of insulation with certifications such as GreenGuard Gold or Declare labels can provide assurance of its environmental performance and compliance with strict sustainability standards.
Cost Analysis and ROI
Investing in high-quality rigid roof insulation is a significant financial decision, but the long-term benefits often outweigh the initial costs. Understanding the cost-effectiveness of different insulation options requires careful analysis of initial investment, installation expenses, and projected energy savings. This section will provide a framework for evaluating the return on investment (ROI) for various rigid insulation choices.
The total cost of a roof insulation project encompasses several factors. These include the material cost (per square foot or unit), the cost of labor for installation, and any additional expenses like permits or specialized equipment. The long-term savings are primarily realized through reduced energy consumption for heating and cooling, leading to lower utility bills. Calculating ROI involves comparing the total cost of the insulation project to the cumulative energy savings over its lifespan. This analysis will help homeowners and building owners make informed decisions based on their specific needs and budget constraints.
Cost Comparison of Rigid Insulation Options
The following table provides a comparative analysis of the initial cost, installation cost, and projected long-term savings for three common types of rigid roof insulation: extruded polystyrene (XPS), expanded polystyrene (EPS), and polyisocyanurate (polyiso). These figures are estimates and can vary depending on factors such as location, material thickness, installer rates, and energy prices. It is crucial to obtain quotes from multiple contractors to accurately reflect your specific situation.
Insulation Type | Initial Material Cost (per sq ft) | Installation Cost (per sq ft) | Estimated Annual Energy Savings (per sq ft) |
---|---|---|---|
Extruded Polystyrene (XPS) | $0.50 – $1.50 | $1.00 – $3.00 | $0.25 – $0.75 |
Expanded Polystyrene (EPS) | $0.30 – $1.00 | $0.75 – $2.50 | $0.15 – $0.50 |
Polyisocyanurate (Polyiso) | $1.00 – $2.50 | $2.00 – $4.00 | $0.50 – $1.50 |
Return on Investment (ROI) Calculation
Calculating the ROI for roof insulation involves comparing the total investment to the total savings over the insulation’s lifespan. A simplified formula for ROI is:
ROI = (Total Savings – Total Cost) / Total Cost * 100%
For example, consider a 1000 sq ft roof insulated with polyiso. Assuming an average initial cost of $1.75/sq ft, an installation cost of $3.00/sq ft, and annual savings of $1.00/sq ft, the calculation would be:
Total Cost = (1000 sq ft) * ($1.75 + $3.00) = $4750
Total Savings (over 10 years) = (1000 sq ft) * ($1.00/sq ft) * 10 years = $10000
ROI = ($10000 – $4750) / $4750 * 100% = 110.5%
This example illustrates a significant positive ROI, highlighting the long-term financial benefits of investing in high-performance roof insulation. Note that this is a simplified calculation; a more comprehensive analysis would consider factors such as inflation, potential changes in energy prices, and the insulation’s lifespan.
Case Studies Illustrating Financial Benefits
Numerous case studies demonstrate the significant financial returns associated with improved roof insulation. For example, a study conducted by the National Renewable Energy Laboratory (NREL) showed that upgrading attic insulation in a typical home can result in annual energy savings ranging from 15% to 30%, depending on the climate and existing insulation levels. These savings can quickly offset the initial investment, resulting in a substantial ROI over the insulation’s lifespan. Another example could be a commercial building retrofitting its roof with high-R-value polyiso, leading to a reduction in HVAC costs and a quicker payback period due to the larger scale of the project. Specific data for these case studies would need to be sourced from published reports or case study databases.
Code Compliance and Regulations: Best Rigid Insulation For Roof
Proper roof insulation is not merely about energy efficiency; it’s also a critical aspect of building code compliance. Adhering to these regulations ensures the safety, structural integrity, and longevity of your building, while also protecting against potential legal repercussions. Understanding and meeting these requirements is crucial for both homeowners and contractors.
Choosing and installing roof insulation in compliance with building codes involves several key steps. First, you must identify the specific codes applicable to your location. These vary by region, municipality, and even the type of building. Secondly, careful consideration must be given to the insulation’s R-value, thickness, and type, ensuring they meet the minimum requirements Artikeld in the relevant codes. Finally, proper installation techniques must be followed meticulously, as improper installation can invalidate the insulation’s effectiveness and lead to code violations.
Relevant Building Codes and Regulations
Building codes concerning roof insulation are primarily concerned with energy efficiency, fire safety, and moisture control. These regulations often specify minimum R-values based on climate zone, building type, and roof construction. For example, the International Energy Conservation Code (IECC) provides a framework for energy-efficient building design, including requirements for roof insulation. Local jurisdictions often adopt and amend the IECC, resulting in variations in specific requirements. Additionally, fire codes frequently address the flammability of insulation materials, often requiring the use of fire-resistant options in certain situations, particularly in commercial buildings or those with complex roof structures. Finally, building codes often address moisture control, requiring proper vapor barriers or breathable membranes to prevent condensation and mold growth within the roof assembly.
Ensuring Compliance During Insulation Selection and Installation
To ensure compliance, it’s crucial to consult the local building department for the most up-to-date codes and regulations applicable to your project. This typically involves reviewing the building permit application requirements and obtaining necessary approvals before commencing work. Contractors should have a thorough understanding of these codes and should be able to demonstrate compliance through documentation, such as material specifications and installation plans. Homeowners should request verification of compliance from their contractors. This might involve reviewing certificates of compliance or obtaining inspections from qualified building inspectors.
Examples of Common Code Violations and Their Consequences
Common code violations related to roof insulation include installing insulation with an insufficient R-value, using inappropriate insulation materials for the specific application (e.g., using flammable insulation in areas where fire-resistant material is required), and improper installation leading to air gaps or compression of the insulation. Consequences of these violations can range from costly fines and delays in project completion to the potential for structural damage, energy inefficiency, and increased risk of fire. In severe cases, buildings may be deemed unsafe, requiring costly remediation before occupancy permits can be issued. For instance, failure to meet minimum R-value requirements in a cold climate could lead to significant energy loss, increased heating bills, and potential structural issues due to ice damming. Using flammable insulation in a prohibited area could result in a fire hazard and potentially lead to insurance complications or legal action.
Troubleshooting Common Issues
Proper installation and maintenance of rigid roof insulation are crucial for maximizing its energy-saving benefits and extending its lifespan. However, several issues can arise during installation or over time, impacting performance and potentially leading to costly repairs. Understanding these common problems and their solutions is vital for homeowners and contractors alike.
Thermal Bridging
Thermal bridging occurs when heat transfers easily through areas of higher thermal conductivity, bypassing the insulation. In rigid roof insulation, this often happens at fasteners, penetrations (such as pipes or vents), or edges where the insulation doesn’t create a continuous barrier. This reduces the overall R-value of the system and increases energy loss. Solutions include using thermal breaks (insulating washers or specialized fasteners), sealing gaps around penetrations with appropriate sealant, and ensuring a continuous layer of insulation with minimal gaps at edges. Proper planning and careful installation are key preventative measures.
Moisture Intrusion
Moisture intrusion is a significant threat to rigid roof insulation, as it can lead to mold growth, reduced R-value, and structural damage. Water can enter through leaks in the roof covering, improper flashing around penetrations, or condensation forming within the insulation layer due to insufficient vapor barriers. Preventing moisture intrusion involves ensuring a waterproof roof membrane, proper flashing installation, and the use of a suitable vapor barrier on the warm side of the insulation. Regular roof inspections and prompt repairs of any leaks are essential. If moisture intrusion does occur, the affected insulation may need to be removed and replaced. Thorough drying of the affected area is crucial before reinstalling insulation.
Inadequate R-Value
Inadequate R-value results in insufficient thermal resistance, leading to higher energy bills and discomfort. This can stem from improper insulation thickness, gaps in the insulation layer, or the use of insulation with a lower R-value than required for the climate. To address this, ensure the installed insulation thickness meets or exceeds local building codes and energy efficiency recommendations for your climate zone. Carefully inspect for and seal any gaps in the insulation layer. If the R-value is insufficient, additional insulation may need to be added, but this may require careful consideration of the existing roof structure and load-bearing capacity.
Flowchart for Troubleshooting Rigid Roof Insulation Problems
A flowchart can streamline the troubleshooting process. The following steps provide a general framework:
Start → Identify Problem (Higher energy bills, visible moisture, etc.) → Inspect Insulation (Check for gaps, moisture, thermal bridging) → Determine Cause (Poor installation, material defects, moisture intrusion) → Implement Solution (Seal gaps, repair leaks, replace insulation) → Verify Solution (Monitor energy usage, check for moisture recurrence) → End
Essential FAQs
What is the lifespan of rigid foam roof insulation?
The lifespan varies depending on the material and installation quality, but generally ranges from 20 to 50 years.
Can I install rigid foam insulation myself?
While possible for some, professional installation is often recommended to ensure proper application and avoid costly mistakes.
How do I determine the appropriate R-value for my region?
Consult your local building codes and energy efficiency guidelines. These often specify minimum R-values based on climate zone.
What are the common signs of moisture damage in rigid foam insulation?
Signs include discoloration, mold growth, sagging, and a musty odor.