Average Costs
Understanding the average cost of ceiling insulation is crucial for budgeting home improvement projects. Several factors influence the final price, making it essential to consider these variables when planning your insulation installation. This section will provide a clearer picture of typical costs and the elements that contribute to price fluctuations.
Ceiling insulation cost per square foot – The cost of ceiling insulation varies significantly depending on the material chosen, the square footage of the area to be insulated, the complexity of the installation, and regional labor rates. While obtaining precise figures requires a professional assessment, understanding average costs provides a valuable starting point for your budgeting process.
Average Costs Per Square Foot for Different Insulation Materials
The following table presents average cost ranges per square foot for common ceiling insulation materials. Remember that these are estimates, and actual costs can vary based on the factors discussed below.
Insulation Material | Cost Per Square Foot (USD) | Installation Complexity | Typical R-Value |
---|---|---|---|
Fiberglass Batts | $0.50 – $1.50 | Low to Moderate | R-13 to R-38 |
Cellulose Loose-Fill | $0.75 – $2.00 | Moderate | R-30 to R-49 |
Spray Foam (Open-Cell) | $1.50 – $3.00 | High | R-3.6 to R-3.8 per inch |
Spray Foam (Closed-Cell) | $2.50 – $4.00 | High | R-6.0 to R-7.0 per inch |
Factors Influencing Cost Variation
Several factors contribute to the wide range in insulation costs per square foot. These variations are not merely due to material prices but also encompass labor, accessibility, and project specifics.
The type of insulation significantly impacts cost. Spray foam, for example, is more expensive than fiberglass batts due to the specialized equipment and skilled labor required for installation. Accessibility also plays a crucial role; insulating a cathedral ceiling is more labor-intensive and, therefore, more expensive than insulating a standard flat ceiling. The square footage of the area to be insulated directly influences the overall cost; larger areas naturally require more materials and labor, resulting in higher expenses. Regional variations in labor costs also affect the final price. Areas with higher labor costs will generally have higher overall insulation costs. Finally, the existing condition of the ceiling and any necessary repairs prior to insulation can add to the total expense. For instance, if significant repairs are needed to the ceiling joists or drywall, this will increase the project cost.
Labor Versus Material Costs
A significant portion of the total insulation cost is attributed to labor. While material costs are readily apparent, the labor component often constitutes a substantial percentage of the final bill. For example, in a typical installation using fiberglass batts, material costs might account for 30-40% of the total, while labor costs make up the remaining 60-70%. However, with more complex installations like spray foam, the labor cost percentage increases significantly due to the specialized skills and equipment needed. This is because spray foam requires specialized equipment and highly trained technicians, leading to higher labor charges compared to simpler installations with fiberglass or cellulose.
Material Costs
Understanding the material costs associated with ceiling insulation is crucial for accurate budgeting. The price per square foot varies significantly depending on the type of insulation chosen and its R-value, a measure of thermal resistance. This section will detail the cost differences between common insulation materials and explore how R-value impacts pricing.
Fiberglass, Cellulose, and Spray Foam Insulation Costs
Fiberglass batts and rolls are generally the most affordable insulation option. Costs typically range from $0.30 to $1.00 per square foot, depending on the R-value and thickness. Cellulose insulation, made from recycled paper, offers a slightly higher cost, usually between $0.50 and $1.50 per square foot, again varying with R-value. Spray foam insulation is the most expensive, ranging from $1.00 to $3.00 or more per square foot, due to its higher installation costs and superior insulating properties. These price ranges are estimates and can vary based on location, supplier, and project specifics. For example, a higher density spray foam will cost more per square foot than a lower density option.
R-Value and Price Differences, Ceiling insulation cost per square foot
The R-value directly impacts the cost of insulation. A higher R-value indicates better thermal resistance, meaning less heat transfer and improved energy efficiency. This increased performance comes at a higher price. For example, fiberglass insulation with an R-13 rating will be cheaper per square foot than R-30 fiberglass insulation, due to the increased thickness and material required to achieve the higher R-value. The same principle applies to cellulose and spray foam insulation; higher R-values translate to a higher cost per square foot. It’s important to balance cost with the desired level of energy efficiency when selecting an R-value. A homeowner in a colder climate might opt for a higher R-value to minimize heating costs, even if the upfront material cost is higher.
Lifespan and Maintenance of Insulation Types
The following table compares the lifespan and maintenance requirements of fiberglass, cellulose, and spray foam insulation:
Insulation Type | Lifespan (Years) | Maintenance Requirements | Notes |
---|---|---|---|
Fiberglass | 50-75 | Minimal; occasional inspection for settling | Susceptible to settling over time, potentially reducing R-value. |
Cellulose | 50-75 | Minimal; occasional inspection for settling | Similar to fiberglass, can settle, but often provides better air sealing. |
Spray Foam | 80+ | Very low; typically requires no maintenance | Excellent air sealing properties contribute to a long lifespan. |
Labor Costs
Labor costs represent a significant portion of the overall expense for ceiling insulation projects. These costs are influenced by several interconnected factors, leading to a wide range of prices depending on the specifics of each job. Understanding these factors is crucial for accurate budgeting and realistic project planning.
Factors Affecting Labor Costs
Geographic Location
Labor rates vary considerably across different regions. Metropolitan areas with a higher cost of living and greater demand for skilled labor tend to have higher hourly rates for insulation installers. Conversely, more rural areas may offer lower labor costs due to lower competition and lower living expenses. For example, installing insulation in a densely populated city like New York City will likely cost more per square foot than in a smaller town in rural Nebraska. This difference is primarily driven by the higher wages and overhead costs associated with operating a business in a high-cost-of-living area.
Project Size and Complexity
Larger projects generally command lower per-square-foot labor costs due to economies of scale. Installers can achieve greater efficiency when working on larger, continuous areas. Smaller projects, however, often involve a higher proportion of setup and teardown time, leading to a higher per-square-foot cost. Similarly, complex projects with difficult-to-access areas or unique structural elements will require more time and specialized techniques, increasing the labor costs. For instance, insulating a cathedral ceiling with intricate beams will be more expensive per square foot than insulating a simple flat ceiling in a standard attic.
Installer Experience and Expertise
Experienced and highly skilled insulation installers may charge higher rates than less experienced ones. Their expertise translates to faster, more efficient work, minimizing labor time and potential material waste. However, the higher initial cost might be offset by the superior quality of the installation and a longer lifespan for the insulation. A highly skilled installer specializing in spray foam insulation, for example, might command a higher rate per square foot than a general contractor installing batts, reflecting their specialized knowledge and precision techniques.
Labor Cost Examples
The following examples provide a general idea of labor costs per square foot for different insulation types and installation methods. These are estimates and actual costs can vary significantly based on the factors discussed above.
Insulation Type | Installation Method | Labor Cost per Square Foot (Estimate) |
---|---|---|
Batt Insulation | Standard Installation | $0.50 – $1.50 |
Loose-Fill Insulation | Blown-in Installation | $0.75 – $2.00 |
Spray Foam Insulation | Spray Application | $1.50 – $4.00 |
Labor Cost Comparison: Small Attic vs. Large Commercial Space
Consider two scenarios: insulating a small 500 square foot attic versus a large 10,000 square foot commercial space. Assuming a labor cost of $1.00 per square foot for the attic and $0.75 per square foot for the commercial space (reflecting economies of scale), the total labor costs would be:
* Small Attic: 500 sq ft * $1.00/sq ft = $500
* Large Commercial Space: 10,000 sq ft * $0.75/sq ft = $7,500
This comparison illustrates how the per-square-foot labor cost can decrease significantly with increasing project size. The commercial space benefits from streamlined processes and reduced setup/teardown time, resulting in a lower overall cost per square foot. However, the total labor cost for the commercial space is substantially higher due to the significantly larger area.
R-Value and Cost
Understanding the relationship between R-value and the cost of ceiling insulation is crucial for making informed decisions about home energy efficiency. Higher R-values generally indicate better insulation, leading to lower energy bills. However, this improvement comes at a higher initial cost. This section explores the cost-effectiveness of different R-values to help you weigh the initial investment against long-term savings.
The R-value of insulation represents its thermal resistance. A higher R-value means the material resists heat transfer more effectively. This directly translates to less energy needed to heat or cool your home, resulting in lower utility bills. However, materials with higher R-values often cost more per square foot. The challenge lies in finding the optimal balance between initial cost and long-term energy savings.
R-Value and Cost Effectiveness
The cost-effectiveness of different R-values varies depending on several factors, including climate, energy prices, and the type of insulation used. Generally, investing in higher R-value insulation yields greater energy savings over time, but the payback period needs careful consideration. The following bullet points illustrate potential scenarios:
- R-13 Insulation: This is a common choice for many climates, offering a balance between cost and performance. It provides decent insulation but may not be sufficient in extremely cold or hot regions. The initial cost per square foot is relatively low, making it an attractive option for budget-conscious homeowners. However, energy savings may be less significant compared to higher R-values.
- R-21 Insulation: This represents a step up in insulation performance, providing better protection against heat transfer. The initial cost per square foot is higher than R-13, but the increased energy savings over the lifespan of the insulation can justify the additional expense, especially in areas with moderate to severe temperature fluctuations. The payback period might be shorter than with R-13 insulation.
- R-30 or higher Insulation: These high-performance insulation options offer superior thermal resistance, resulting in substantial energy savings. They are particularly beneficial in extremely cold or hot climates. However, the initial cost per square foot is significantly higher. The long-term cost savings might outweigh the initial investment, but the payback period will likely be longer compared to lower R-value options. This option might be most cost-effective in energy-efficient homes or for those prioritizing maximum energy savings.
It’s important to note that these are general examples, and the actual cost-effectiveness will vary based on specific circumstances. A detailed cost-benefit analysis considering local energy prices, climate, and insulation material costs is recommended before making a decision.
Installation Methods
Choosing the right insulation installation method significantly impacts both the final cost and the effectiveness of your insulation. The three primary methods—batt, blown-in, and spray foam—each have unique characteristics affecting labor and material expenses. Understanding these differences is crucial for making an informed decision.
The installation method you choose directly affects the overall cost of your ceiling insulation project. Factors such as the accessibility of your attic, the existing structure of your ceiling, and the type of insulation material all play a role in determining the labor intensity and therefore the cost of installation.
Batt Insulation Installation
Batt insulation, composed of fiberglass or mineral wool, comes in pre-cut rolls or batts. Installation typically involves fitting these batts between joists or rafters. This method is generally straightforward for DIY projects in easily accessible attics with standard joist spacing. However, fitting batts precisely can be challenging, potentially leading to gaps that compromise insulation effectiveness. Cost savings can be realized through DIY installation, but professional installation offers assurance of proper fitting and maximized R-value. Professional installation costs typically range from $0.50 to $2.00 per square foot, depending on location and labor rates. Material costs for batt insulation usually fall between $0.30 and $1.50 per square foot, depending on the R-value and material type.
Blown-In Insulation Installation
Blown-in insulation, typically cellulose or fiberglass, is pneumatically applied into existing cavities. This method is particularly advantageous for hard-to-reach areas and uneven surfaces, making it suitable for attics with obstructions or unusual framing. It effectively fills gaps and crevices, leading to a more consistent R-value. However, specialized equipment is required, increasing the labor costs. Professional installation is almost always necessary, adding to the overall expense. Expect to pay between $1.00 and $3.00 per square foot for professional installation, including material costs. The material cost alone typically ranges from $0.50 to $2.00 per square foot, depending on the type and desired R-value.
Spray Foam Insulation Installation
Spray foam insulation, either open-cell or closed-cell, is sprayed directly onto the ceiling surface, creating a seamless air barrier. This method offers superior air sealing and moisture control, resulting in significant energy savings. However, it is the most expensive option, requiring specialized equipment and highly skilled technicians. The high cost is driven by both the material itself and the specialized labor required for application. Installation costs typically range from $2.00 to $6.00 per square foot, significantly higher than batt or blown-in insulation. Material costs alone can range from $1.50 to $4.00 per square foot depending on the type of spray foam and desired R-value. For example, a 1000 square foot attic insulated with closed-cell spray foam could cost between $2000 and $6000 for just the material.
Project Size and Cost
The cost of ceiling insulation installation is significantly influenced by the size of the project. Larger projects generally benefit from economies of scale, resulting in a lower cost per square foot compared to smaller projects. This is due to several factors, including reduced material handling time, more efficient use of labor, and potentially bulk discounts on materials.
Project size directly impacts the overall labor and material costs. While material costs generally scale linearly with the area to be insulated, labor costs don’t increase proportionally. For instance, the setup time for equipment and the travel time to and from the job site remain relatively constant regardless of the project size. This means that the fixed costs are spread over a larger area in bigger projects, lowering the per-square-foot cost.
Economies of Scale in Insulation Installation
Economies of scale are realized in insulation installation through several mechanisms. Firstly, purchasing materials in bulk often leads to significant discounts from suppliers. Secondly, the efficiency of the installation crew improves as they become more familiar with the job site and workflow in larger projects. This reduces the time spent on the project, lowering the overall labor costs per square foot. Finally, the fixed costs associated with the project, such as equipment rental and transportation, are spread over a larger area, leading to a decrease in the per-square-foot cost.
Examples of Cost Differences Between Small and Large Projects
Consider two projects: a small attic insulation job covering 500 square feet and a large commercial building insulation project covering 5000 square feet. Assuming a base cost of $2 per square foot for a small project, the total cost would be $1000. However, for the larger project, economies of scale could reduce the cost per square foot to $1.50, resulting in a total cost of $7500. While the larger project has a higher overall cost, the per-square-foot cost is significantly lower, illustrating the impact of project size. This difference reflects the reduced labor cost per square foot in larger projects due to improved efficiency and the bulk purchasing discounts on materials. In a smaller project, the fixed costs of the job make up a larger portion of the overall cost.
Geographic Location and Cost
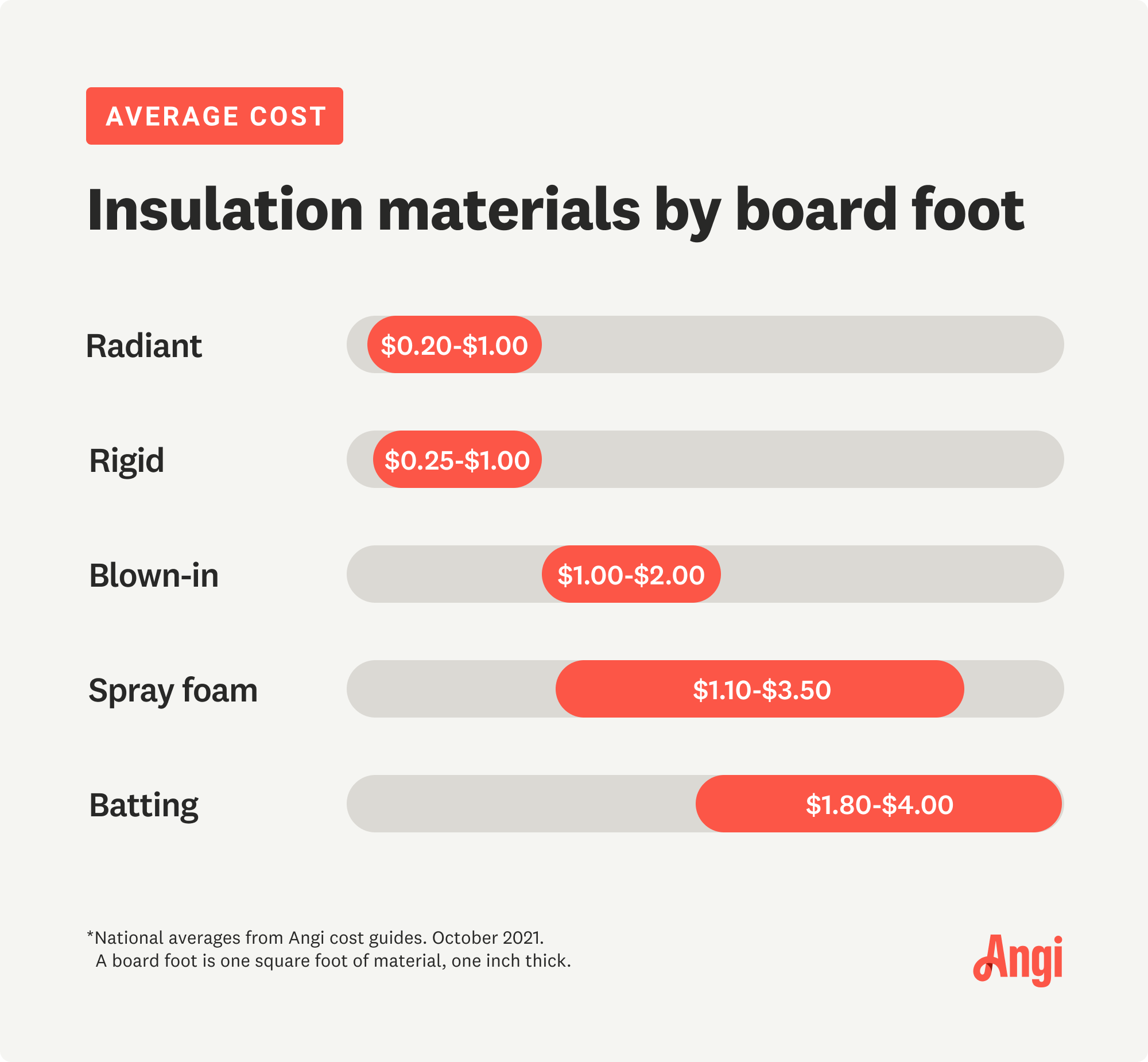
Geographic location significantly impacts the cost of ceiling insulation. Several interconnected factors contribute to these regional variations, making a national average less useful than a localized estimate. Understanding these influences allows homeowners to better budget for their projects.
The cost of ceiling insulation varies across different geographic locations due to a combination of factors including material availability, labor costs, and local regulations. These factors interact in complex ways to produce significant price differences between states and even within the same state.
Material Costs and Availability
Material costs, primarily for insulation itself, fluctuate based on regional supply and demand. Areas with limited access to insulation manufacturing facilities or major distribution hubs may experience higher prices due to increased transportation costs. Conversely, regions with abundant local production might enjoy lower prices. For example, fiberglass insulation might be cheaper in areas near major manufacturing plants, while spray foam insulation could be more expensive in remote locations due to specialized transportation requirements and potentially higher installer travel times. This disparity can significantly impact the overall project cost.
Labor Costs and Availability
The cost of labor is another crucial determinant of insulation expenses. Areas with higher minimum wages or strong union presence tend to have higher labor costs. Regions experiencing labor shortages in the construction industry may also see inflated prices as skilled installers command higher rates. For instance, coastal areas with high demand for construction workers might see higher insulation installation costs compared to less populated inland regions.
Local Regulations and Building Codes
Local building codes and regulations influence insulation costs in several ways. Areas with stricter energy efficiency standards might mandate higher R-value insulation, increasing material and installation costs. Permitting processes and inspections can also add to the overall expense. For example, a city with stringent energy codes might require a more expensive, higher R-value insulation compared to a city with less rigorous standards. Additionally, the complexity of the permitting process in different jurisdictions can lead to varied administrative costs.
Examples of Regional Cost Differences
While precise figures fluctuate based on market conditions, anecdotal evidence and industry reports suggest significant differences. For instance, installing ceiling insulation in a high-cost-of-living area like San Francisco, California, is likely to be considerably more expensive than in a more rural area in the Midwest, such as parts of Iowa or Nebraska. This difference stems from the interplay of higher labor costs, potentially higher material transportation expenses, and potentially stricter building codes in the higher cost-of-living area. Similarly, states with robust unionized labor forces may see consistently higher insulation costs compared to states with less union activity. These variations highlight the importance of obtaining local quotes for accurate cost estimates.
DIY vs. Professional Installation
Choosing between DIY and professional installation for ceiling insulation significantly impacts both cost and outcome. While DIY offers potential cost savings, professional installation ensures quality and safety. This section compares both approaches, detailing their respective advantages and disadvantages to help you make an informed decision.
Professionals possess the expertise, tools, and experience to install insulation efficiently and effectively, minimizing risks and maximizing energy efficiency. DIY projects, while potentially cheaper upfront, can lead to unforeseen complications and higher long-term costs if mistakes are made.
Cost Comparison: DIY vs. Professional Installation
The cost of professional ceiling insulation installation varies based on factors like the size of the area, insulation type, and regional labor rates. A rough estimate for professional installation ranges from $1 to $3 per square foot, but this can fluctuate considerably. DIY installation, while initially cheaper, might involve unexpected expenses due to tool rentals or material miscalculations. A complete cost analysis requires careful consideration of all involved factors.
Risks and Benefits of DIY Installation
DIY installation offers the benefit of potential cost savings on labor. However, it carries several risks. Improper installation can lead to reduced energy efficiency, compromised structural integrity, and even health hazards from inhaling insulation particles. Additionally, accessing and working in attics or crawl spaces can be dangerous without proper training and safety precautions. Conversely, professional installers are insured and possess the skills to handle these risks effectively. They are also familiar with local building codes and best practices, ensuring a safe and compliant installation.
Risks and Benefits of Professional Installation
Professional installation guarantees a higher quality of work, leading to improved energy efficiency and a longer lifespan for the insulation. Experienced installers use appropriate safety equipment and techniques, minimizing the risks associated with working at heights or in confined spaces. Furthermore, professional installation often comes with a warranty, offering protection against defects in workmanship or materials. The main drawback is the higher initial cost compared to DIY.
DIY Installation: Material and Tool Costs
The cost of materials for a DIY insulation project depends on the type and amount of insulation needed. For a 100 square foot attic, for example, you might need approximately 100 square feet of insulation batts (around $100 – $200 depending on the R-value), and potentially additional materials like vapor barriers or sealant (another $50 – $100). Tool rental costs could add another $50 – $100 depending on the availability of tools and the rental rates in your area. This does not account for safety equipment such as respirators, eye protection, and work gloves, which are essential for a safe DIY project. It is crucial to accurately assess your needs before purchasing materials to avoid unnecessary expenses.
Energy Savings and ROI
Investing in ceiling insulation offers significant long-term cost savings through reduced energy consumption. Proper insulation minimizes heat loss in winter and heat gain in summer, directly impacting your heating and cooling bills. The return on investment (ROI) varies depending on factors like insulation type, climate, and energy prices, but generally, the energy savings quickly outweigh the initial installation costs.
The energy savings from insulation translate to lower utility bills over the lifespan of the insulation. This reduction in energy consumption is directly proportional to the R-value of the insulation; higher R-values indicate better insulation performance and, consequently, greater energy savings. These savings accumulate year after year, leading to substantial long-term cost benefits. The faster the payback period, the higher the ROI.
Return on Investment Calculation for Different Insulation Types
Calculating the ROI for insulation involves comparing the initial cost of installation with the cumulative savings on energy bills over a specific period (typically 10-20 years). The formula is:
ROI = (Total Energy Savings – Total Insulation Cost) / Total Insulation Cost * 100%
To illustrate, let’s consider two common insulation types: fiberglass batt insulation (R-13) and spray foam insulation (R-13 to R-38 depending on the thickness and type). Assume a 1,000 square foot attic needing insulation. Fiberglass batt installation might cost $1,500, while spray foam could cost $5,000. Let’s assume annual energy savings of $200 for R-13 fiberglass and $500 for R-38 spray foam.
Insulation Type | Initial Cost | Annual Savings | 10-Year Savings | ROI (10 years) |
---|---|---|---|---|
Fiberglass Batt (R-13) | $1,500 | $200 | $2,000 | 33.3% |
Spray Foam (R-38) | $5,000 | $500 | $5,000 | 0% |
*Note: These are simplified examples. Actual costs and savings can vary significantly based on location, energy prices, climate, and existing insulation.* The spray foam example shows a 0% ROI after 10 years, but the higher R-value will result in greater long-term savings beyond the 10-year mark.
Long-Term Cost Benefits of Insulation Investment
Investing in ceiling insulation provides substantial long-term cost benefits beyond immediate energy savings. A well-insulated home is more comfortable, maintaining a consistent temperature throughout the year. This comfort translates to improved indoor air quality and a healthier living environment. Furthermore, improved energy efficiency can increase the resale value of your home, making it a worthwhile investment even if you plan to move in the future.
For example, a home in a cold climate with inadequate insulation might experience significant temperature fluctuations, leading to higher heating bills and discomfort. By upgrading to a higher R-value insulation, the homeowner can reduce these fluctuations, resulting in lower energy bills and a more comfortable living space. This leads to long-term savings that far exceed the initial investment in insulation. Similarly, in warmer climates, better insulation reduces the strain on air conditioning systems, lowering energy costs and improving comfort.
Factors Affecting Overall Cost: Ceiling Insulation Cost Per Square Foot
Beyond the fundamental costs of materials and labor, several other factors significantly influence the total expense of ceiling insulation installation. Understanding these additional costs allows homeowners to budget more accurately and avoid unexpected financial burdens during the project. Careful planning and proactive communication with contractors are key to managing these variables effectively.
Permitting and Inspection Fees
Securing the necessary permits from local authorities is often a requirement for home improvement projects, including ceiling insulation installation. These permits ensure compliance with building codes and safety regulations. The cost of permits varies significantly depending on location, the scope of the project, and the specific regulations in place. For instance, larger projects or those involving significant structural modifications might incur higher permit fees. Furthermore, inspections by building officials are usually required at various stages of the project, adding to the overall cost. These inspection fees are typically charged per visit and are dependent on the complexity of the work. Homeowners should factor in these costs early in the planning process by contacting their local building department to inquire about permit requirements and associated fees.
Waste Removal and Disposal
The removal and disposal of existing insulation materials and construction debris is another expense that homeowners often overlook. The cost of waste removal depends on the amount of material needing disposal, the type of material (some materials have special disposal requirements), and the local waste management regulations. For example, asbestos-containing materials require specialized handling and disposal, significantly increasing the cost. Homeowners should inquire about waste removal costs upfront during the bidding process and consider the potential for unexpected waste generation. Planning for efficient waste management during the project can minimize costs and ensure compliance with environmental regulations.
Unexpected Issues and Repairs
Unforeseen issues during the installation process can significantly impact the final cost. For example, discovering damaged or deteriorated framing members might necessitate costly repairs before insulation can be installed. Similarly, encountering unexpected obstacles such as difficult-to-access areas or unforeseen structural complexities could lead to increased labor costs. In some cases, the discovery of mold or pest infestations might require specialized remediation, adding a substantial expense to the project. A thorough inspection prior to starting the project can help mitigate some of these risks, but complete avoidance of unexpected issues is rarely possible.
Access and Preparation Costs
Preparing the area for insulation installation can involve additional expenses. This might include the cost of removing existing fixtures, protecting furniture and flooring, and providing access to the attic or ceiling space. For example, if access to the attic requires the creation of a new access point, this will increase the overall cost. Similarly, if significant amounts of furniture need to be moved or protected, this will add to the labor and material costs. Planning for these preparatory steps in advance helps ensure a smooth installation process and minimizes unforeseen delays and cost overruns.
Managing and Minimizing Unexpected Costs
To effectively manage and minimize unexpected costs, homeowners should obtain multiple bids from reputable contractors, carefully review the contract terms, and request detailed breakdowns of all costs. A clear understanding of the project scope and potential challenges is crucial. Regular communication with the contractor throughout the project can help identify and address potential problems early on, preventing them from escalating into major cost overruns. Finally, setting aside a contingency fund of 10-20% of the estimated cost can provide a buffer for unforeseen expenses. This approach ensures that the project remains financially manageable even if unexpected issues arise.
Finding Reliable Contractors
Insulating your ceiling is a significant investment, and choosing the right contractor is crucial for a successful project. A reliable contractor ensures quality workmanship, adherence to safety standards, and a positive overall experience. This section details the steps to find and select a qualified and trustworthy professional for your ceiling insulation needs.
Finding a qualified insulation contractor involves a systematic approach. Begin by gathering recommendations from friends, family, and neighbors who have recently had similar work done. Online resources, such as review websites and contractor directories, can also provide valuable leads. Check for licensing and insurance – these are crucial indicators of legitimacy and protection for you in case of accidents or disputes. Always verify the information provided by potential contractors through independent channels.
Contractor Qualification Verification
Thoroughly vetting potential contractors is essential. This involves checking their licensing and insurance coverage, verifying their experience through references, and reviewing online reviews and ratings. Look for contractors with a proven track record of successfully completed projects, positive customer feedback, and a strong understanding of insulation materials and installation techniques. Requesting proof of insurance and licenses protects you from potential liabilities. For example, a contractor with a valid license demonstrates compliance with local regulations and a commitment to professional standards. Similarly, proof of insurance provides financial protection should any accidents or damages occur during the project.
Comparing Quotes and Selecting a Contractor
Once you have a shortlist of potential contractors, obtain detailed written quotes from each. These quotes should clearly Artikel the scope of work, materials to be used, labor costs, and the total project price. Comparing quotes requires careful attention to detail; ensure that all quotes include the same scope of work to avoid unfair comparisons. Consider factors beyond just the price, such as the contractor’s reputation, experience, warranty offerings, and communication style. A lower price may not always be the best option if the contractor lacks experience or provides limited warranties. For example, a quote detailing the type and R-value of insulation used, along with a clear breakdown of labor costs, is more informative and trustworthy than a vague, single-figure quote.
The Importance of Multiple Quotes
Obtaining multiple quotes is a critical step in the contractor selection process. It allows for a fair comparison of prices, services, and overall value. Comparing quotes from at least three different contractors provides a clearer picture of the market price range for your project and helps to identify potential overcharges or hidden costs. For example, one contractor might offer a lower price but use inferior materials, while another might offer a higher price but provide a longer warranty and superior customer service. By comparing multiple quotes, you can make an informed decision that balances cost with quality and reliability.
Top FAQs
What is the typical lifespan of different ceiling insulation materials?
Fiberglass batts generally last 50-75 years, cellulose insulation can last 50-100 years, and spray foam insulation can last for the lifetime of the house (50+ years).
Can I install ceiling insulation myself?
While DIY installation is possible for some materials (like fiberglass batts), professional installation is often recommended for optimal results and to avoid potential risks. Professionals possess the expertise and equipment to ensure proper installation, maximizing energy efficiency and longevity.
How much does it cost to remove existing insulation before installing new insulation?
The cost of removing existing insulation varies greatly depending on the type of insulation, the accessibility of the area, and the amount of insulation needing removal. It’s best to get a quote from a contractor for this aspect of the project.
What are the potential risks of improper insulation installation?
Improper installation can lead to reduced energy efficiency, moisture buildup, pest infestations, and fire hazards. It’s crucial to ensure proper installation, whether by a professional or following detailed DIY instructions carefully.