Factors Influencing Flat Roof Installation Costs
Several key factors significantly influence the overall cost of a flat roof installation. Understanding these factors allows homeowners and contractors to develop realistic budgets and expectations. These factors encompass material selection, labor requirements, geographical location, and project specifics.
Materials Costs
The choice of roofing materials dramatically affects the final price. Different materials offer varying levels of durability, lifespan, and aesthetic appeal, directly impacting the initial investment. High-performance materials generally command higher prices due to their superior longevity and resistance to weather damage. For example, a single-ply membrane system using TPO (Thermoplastic Polyolefin) will likely cost more upfront than a traditional built-up roofing (BUR) system, but may offer longer-term cost savings due to its extended lifespan and reduced maintenance needs. Furthermore, the quantity of materials needed, dictated by the roof’s size and complexity, also contributes to the overall expense. Additional materials, such as insulation, flashing, and fasteners, add to the total material cost.
Labor Costs and Installation Methods
Labor costs constitute a substantial portion of the overall project expense. The complexity of the installation process significantly impacts labor time and therefore the cost. A simple, low-slope roof installation will require less labor than a complex roof with numerous penetrations, valleys, or unusual features. The chosen installation method also plays a crucial role. For instance, a mechanically fastened single-ply membrane system generally requires less labor than a fully adhered system, which demands more precise application and careful attention to detail. The contractor’s experience and hourly rate also influence the labor cost; highly skilled and experienced contractors often command higher rates.
Geographical Location and Market Conditions, Flat roof installation price
Geographical location significantly impacts the cost of flat roof installation. Factors such as labor rates, material availability, and local regulations vary considerably across different regions. Areas with high labor costs or limited access to materials will naturally result in higher overall installation costs. Furthermore, market conditions, including material price fluctuations and contractor demand, influence pricing. A region experiencing a construction boom might see increased labor costs and material prices compared to a less active market. For example, coastal areas may experience higher costs due to potential hurricane damage considerations and specialized materials required for high-wind resistance.
Material Price Comparison
The following table compares the approximate cost per square (100 square feet) of common flat roofing materials. These are estimates and can vary significantly based on location, material quality, and project specifics. It’s crucial to obtain detailed quotes from local contractors for accurate pricing.
Roofing Material | Cost per Square (USD) | Lifespan (Years) | Maintenance |
---|---|---|---|
TPO (Thermoplastic Polyolefin) | $3.50 – $6.00 | 15-30 | Low |
EPDM (Ethylene Propylene Diene Monomer) | $2.50 – $4.50 | 10-20 | Moderate |
PVC (Polyvinyl Chloride) | $4.00 – $7.00 | 20-30 | Low |
Built-Up Roofing (BUR) | $3.00 – $5.00 | 15-25 | Moderate |
Size and Complexity of the Project
The size and complexity of your flat roof directly impact the overall installation cost. Larger roofs naturally require more materials and labor, leading to higher expenses. Similarly, intricate designs and unusual shapes increase the time and skill needed for installation, further driving up the price. Understanding this relationship allows for better budgeting and project planning.
The cost of a flat roof installation is largely determined by the area needing coverage. A simple, large, rectangular roof will generally cost less *per square foot* than a smaller roof with numerous dormers, skylights, or complex angles. The added labor and material required for intricate designs significantly increase the total cost. For example, cutting and fitting materials around obstacles demands more precision and time, impacting the final price. This is further compounded by the need for specialized materials or techniques to ensure a watertight seal in complex areas.
Roof Area and Cost Correlation
The direct relationship between roof area and installation cost is straightforward. Larger areas necessitate more materials, such as roofing membrane, insulation, and fasteners. Furthermore, the increased labor hours needed to cover a larger surface area directly contribute to higher expenses. The following table illustrates a hypothetical cost escalation with increasing roof area, assuming a relatively simple, rectangular roof design. Note that these figures are for illustrative purposes and actual costs can vary significantly based on location, materials chosen, and contractor rates.
Roof Area (sq ft) | Estimated Material Cost ($) | Estimated Labor Cost ($) | Total Estimated Cost ($) |
---|---|---|---|
500 | 2500 | 3000 | 5500 |
1000 | 5000 | 5500 | 10500 |
1500 | 7500 | 8000 | 15500 |
2000 | 10000 | 10500 | 20500 |
Complex Roof Designs and Increased Costs
Complex roof designs, such as those incorporating multiple levels, irregular shapes, or numerous penetrations (e.g., skylights, chimneys, vents), substantially increase installation costs. These designs require more intricate planning, precise measurements, and specialized techniques to ensure a watertight and structurally sound roof. The increased complexity often necessitates the use of more expensive materials or the engagement of highly skilled and experienced installers, leading to a higher overall project cost.
For instance, a flat roof with numerous dormers, each requiring individual flashing and sealant application, will cost considerably more than a simple, single-level roof of the same area. Similarly, a roof with irregular angles or curves will require more time and effort for precise material cutting and fitting, leading to a price increase. A project involving a 1000 sq ft simple rectangular roof might cost around $10,500 (as per the table above), while a similarly sized roof with multiple dormers and complex angles could easily cost $15,000 or more.
Necessary Preparations and Site Conditions
Proper preparation and assessment of site conditions are crucial for a smooth and cost-effective flat roof installation. Overlooking these factors can lead to significant delays and unexpected expenses, ultimately impacting the final project cost. A thorough evaluation before the installation begins is essential to minimize potential problems and ensure a successful outcome.
The existing condition of the roof significantly influences the overall cost of a new installation. Pre-existing damage, such as deteriorated roofing materials, structural issues, or water damage, will necessitate additional repairs or a complete tear-off before the new roof can be installed. This adds considerable expense to the project, as it involves labor, material costs for repairs, and potentially disposal fees for the old roofing materials. For example, a roof with extensive water damage requiring significant structural repairs might add thousands of dollars to the initial installation estimate.
Pre-existing Roof Conditions and Associated Costs
The condition of the existing roof directly impacts the installation process and associated costs. A simple replacement of a relatively undamaged roof will be significantly cheaper than a project that requires extensive repairs or a complete tear-off of the old roofing system. Factors like the presence of rot, rust, or previous patching jobs all contribute to increased labor and material costs. A detailed inspection by a qualified roofing contractor is vital to accurately assess the extent of necessary repairs and provide a precise cost estimate. This inspection should include checking for structural integrity, the condition of the decking, and the presence of any leaks or water damage. The cost of such an inspection is usually minimal compared to the potential savings from avoiding unforeseen expenses during the installation.
Additional Expenses Related to Repairs or Tear-Offs
Repairing or completely removing an existing roof adds substantial costs to a new flat roof installation. A tear-off, which involves the complete removal of the old roofing materials, adds significant labor costs and disposal fees for the waste materials. The cost of a tear-off varies depending on the size of the roof, the type of material being removed, and local disposal regulations. Furthermore, if significant underlying structural repairs are needed (e.g., replacing damaged decking or repairing structural framing), these expenses will be added to the overall project cost. For instance, a large commercial building requiring a complete tear-off and structural repairs could easily see an increase in costs exceeding 50% of the original flat roof installation estimate.
Cost Implications of Challenging Site Access
Difficult site access significantly increases the labor costs and time required for a flat roof installation. Factors such as narrow driveways, steep inclines, or limited space around the building can make it challenging to transport materials and equipment to the work site. This often requires specialized equipment, such as cranes or smaller delivery vehicles, which increases transportation and labor costs. Furthermore, if workers need to navigate obstacles or use more time-consuming methods to access the roof, the overall project timeline extends, leading to increased labor expenses. For example, a roof situated on a hillside with limited access might necessitate the use of a crane to lift materials, adding several thousand dollars to the overall project cost.
Preparation Steps and Associated Costs
Before installation begins, several preparatory steps are essential. These steps, while seemingly minor individually, cumulatively contribute significantly to the overall project cost.
- Site Survey and Assessment: This involves a thorough inspection of the existing roof and surrounding area to identify potential issues and assess the complexity of the project. Costs are typically minimal, often included in the initial consultation.
- Permitting and Inspections: Obtaining necessary permits and scheduling inspections adds administrative costs, varying by location and project complexity.
- Existing Roof Tear-off (if necessary): The removal of old roofing materials adds significant labor and disposal costs, especially for larger projects or roofs with multiple layers.
- Structural Repairs (if necessary): Repairing damaged decking, framing, or other structural components adds substantially to the project cost, depending on the extent of the damage.
- Material Delivery and Handling: Transporting and handling roofing materials to the work site, especially in areas with limited access, can increase costs.
- Waste Removal: Proper disposal of old roofing materials and construction debris incurs disposal fees, influenced by local regulations and the volume of waste generated.
Types of Flat Roof Systems: Flat Roof Installation Price
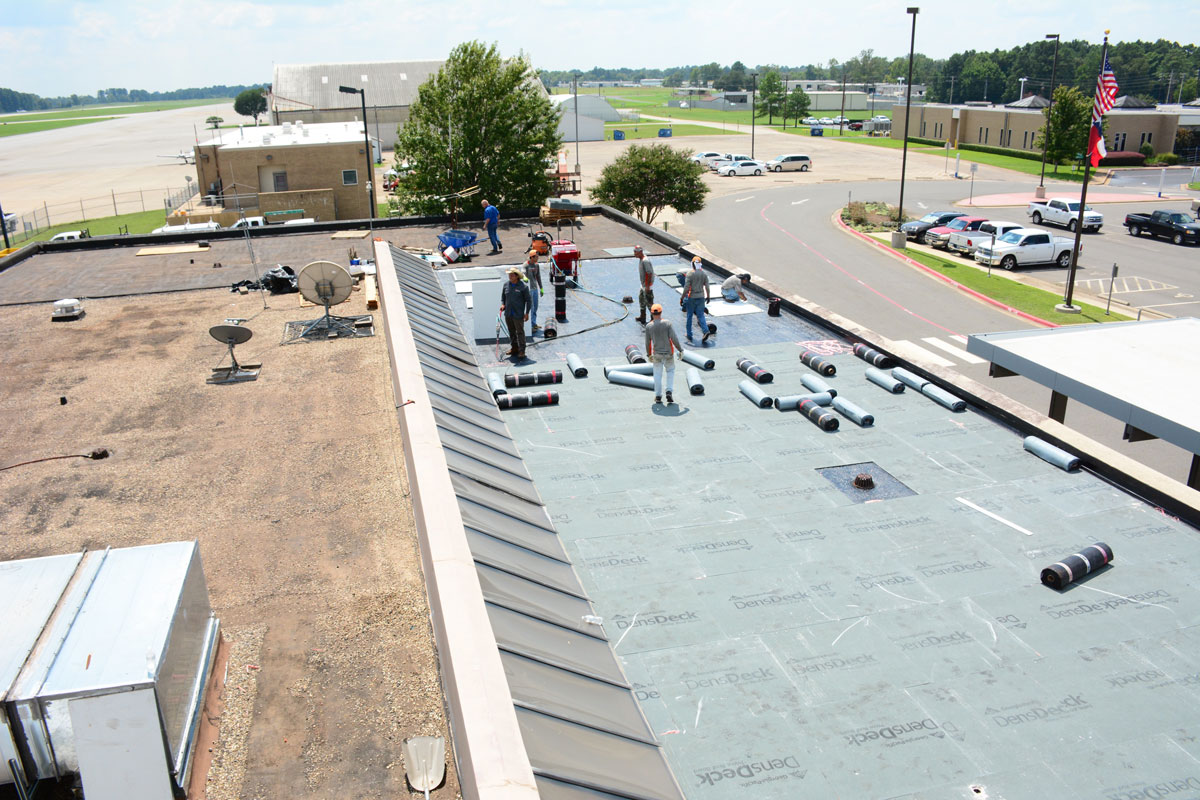
Choosing the right flat roof system significantly impacts both the longevity and the cost of your project. Several factors, including climate, building usage, and budget, influence the optimal choice. This section details the various systems available, comparing their installation costs and highlighting key differences.
Comparison of Flat Roof System Installation Costs
Built-up roofing (BUR) and single-ply membranes are the two most prevalent flat roof systems. BUR systems, traditionally composed of multiple layers of asphalt and felt, are generally more labor-intensive, leading to higher installation costs compared to single-ply membranes. Single-ply membranes, such as TPO, EPDM, and PVC, are prefabricated and installed more quickly, resulting in lower labor costs. However, the initial material costs for single-ply membranes can vary depending on the chosen material and its thickness. The overall cost will depend on the size of the roof, the complexity of the installation (e.g., number of penetrations, roof features), and the regional labor rates. For example, a 1000 sq ft BUR system might cost between $10,000 and $15,000, while a comparable single-ply membrane system could range from $8,000 to $12,000. These are estimates and actual costs can vary considerably.
Price Differences Between Membrane Types
Among single-ply membranes, Thermoplastic Polyolefin (TPO), Ethylene Propylene Diene Monomer (EPDM), and Polyvinyl Chloride (PVC) each offer unique properties and price points. TPO membranes are typically less expensive than PVC, offering a good balance of cost-effectiveness and durability. EPDM membranes, known for their flexibility and longevity, often fall in the mid-range price-wise. PVC membranes, while offering superior strength and resistance to punctures, are usually the most expensive option. The price differences stem from material composition, manufacturing processes, and the specific membrane thickness required for the project. A larger roof area will naturally increase the material cost for all three options, but the relative price differences between them will generally remain consistent. For instance, a 2000 sq ft roof might see a $2,000 to $3,000 difference between the cheapest (TPO) and the most expensive (PVC) membrane options.
Cost Comparison of Insulation Options
Proper insulation is crucial for energy efficiency and the overall lifespan of a flat roof. Several insulation options exist, each with varying costs and performance characteristics. Polyisocyanurate (polyiso) foam is a popular choice due to its high R-value (insulation effectiveness) and relatively low cost. Extruded polystyrene (XPS) foam offers excellent moisture resistance but can be slightly more expensive than polyiso. Mineral wool insulation provides good fire resistance and sound dampening but is generally more costly than both polyiso and XPS. The cost of insulation depends heavily on the R-value required to meet local building codes and the chosen insulation type. A higher R-value will naturally require a thicker layer of insulation, increasing the overall cost. For example, achieving an R-30 rating with polyiso might cost less than achieving the same rating with mineral wool.
Summary of Flat Roof System Pros, Cons, and Price Ranges
Roof System | Pros | Cons | Price Range (per 1000 sq ft) |
---|---|---|---|
Built-Up Roofing (BUR) | Durable, long lifespan, relatively inexpensive upfront (materials) | Labor-intensive installation, less environmentally friendly than some single-ply options, prone to cracking and ponding | $10,000 – $15,000 |
Single-Ply Membranes (TPO) | Quick installation, cost-effective, lightweight, reflective | Susceptible to punctures and UV degradation (if not properly protected) | $8,000 – $12,000 |
Single-Ply Membranes (EPDM) | Flexible, durable, long lifespan, relatively easy to repair | Can be more expensive than TPO, may require specialized adhesives | $9,000 – $13,000 |
Single-Ply Membranes (PVC) | Strong, puncture-resistant, excellent UV resistance, long lifespan | Most expensive option, requires specialized welding equipment for installation | $11,000 – $16,000 |
Warranty and Maintenance Considerations
Choosing a flat roof system involves careful consideration of not only the initial installation cost but also the long-term implications of warranties and maintenance. These factors significantly impact the overall cost of ownership and the lifespan of your roof. Understanding the nuances of warranties and maintenance plans is crucial for making an informed decision.
Warranty length directly influences the initial project cost. Longer warranties, offering greater peace of mind, often translate to a higher upfront investment. This is because manufacturers factor in the increased risk they assume by providing extended coverage. Conversely, shorter warranties might initially seem more affordable, but they expose the homeowner to greater financial risk in the event of premature roof failure. The cost difference between a 10-year and a 20-year warranty, for instance, can vary considerably depending on the manufacturer and the specific roofing system.
Warranty Length and Upfront Cost
The relationship between warranty length and upfront cost is generally positive; longer warranties typically come with higher initial installation prices. This reflects the manufacturer’s confidence in their product and their willingness to cover potential defects for an extended period. For example, a TPO membrane might offer a 10-year warranty at a lower cost than a comparable system with a 20-year warranty. The increased cost for the extended warranty represents a premium for the added protection against potential future repair or replacement expenses. It is important to compare not only the warranty length but also the specifics of what is covered under the warranty (labor, materials, etc.) before making a decision.
Costs Associated with Different Maintenance Plans
Maintenance plans offer varying levels of coverage and cost. Basic plans might include annual inspections to identify potential problems early on. More comprehensive plans might include cleaning, minor repairs, and preventative maintenance tasks to prolong the roof’s lifespan. The cost of these plans varies depending on the frequency of inspections, the services included, and the size of the roof. For instance, a small flat roof might only require a few hundred dollars annually for a comprehensive plan, while a larger commercial roof could cost several thousand. Regular maintenance can help prevent costly repairs down the line, making even higher-cost plans a potentially cost-effective investment.
Impact of Extended Warranties on Long-Term Cost
Extended warranties provide a financial safety net against unexpected repairs or replacements during the warranty period. While the initial cost is higher, the potential savings on costly repairs can offset this over the long term. Consider a scenario where a roof with a 10-year warranty fails after 11 years. The homeowner would be responsible for the entire replacement cost. However, with a 20-year warranty, the manufacturer would cover the replacement, saving the homeowner potentially tens of thousands of dollars. This long-term cost analysis is crucial when comparing warranties. The extended warranty acts as insurance, mitigating risk and potentially saving significant money over the lifespan of the roof.
Comparison of Warranty Offerings from Various Manufacturers
Different manufacturers offer varying warranty lengths and coverage terms for their flat roofing systems. For example, one manufacturer might offer a 15-year warranty on their EPDM membrane, while another offers a 20-year warranty on their TPO membrane. The specifics of the warranty should be carefully examined. Some warranties might only cover material defects, while others might include labor costs for repairs or replacements. It’s essential to compare apples to apples, focusing on the total coverage offered, rather than just the length of the warranty period. Requesting warranty details from multiple manufacturers allows for a thorough comparison and selection of the best option based on both cost and coverage.
Permitting and Inspections
Obtaining the necessary permits and undergoing inspections are crucial steps in any flat roof installation project. These processes, while sometimes perceived as bureaucratic hurdles, are essential for ensuring the safety and compliance of the new roof with local building codes and regulations. Failure to obtain proper permits can lead to significant legal and financial repercussions, including fines, stop-work orders, and even the requirement for demolition and reconstruction.
Permitting and inspection costs vary considerably depending on location, project size, and the complexity of the roof system. These costs are typically incurred upfront and can significantly impact the overall project budget. Understanding these expenses and the potential for delays is vital for accurate project planning and cost estimation.
Permitting Costs
Permitting fees are determined by local government agencies and are usually based on the project’s square footage, the type of roofing material used, and the complexity of the work involved. These fees can range from a few hundred dollars to several thousand dollars, depending on the jurisdiction and project scope. For example, a small residential flat roof replacement might cost between $200 and $500 in permitting fees, while a larger commercial project could easily exceed $2000. Additional fees might apply for expedited processing or specific inspections. It’s crucial to contact the local building department early in the planning stages to obtain accurate cost estimates and understand the specific requirements for your project.
Inspection Costs
Inspection costs are usually included within the overall permitting process. These inspections are conducted at various stages of the installation, including before, during, and after the work is completed. The number of inspections required varies depending on local regulations and the complexity of the project. While the costs are often bundled within the permit fee, significant delays caused by failed inspections can result in additional labor and material costs, as contractors need to reschedule work and potentially make costly repairs. For instance, if an inspection reveals a critical flaw in the underlayment, the contractor may need to remove and replace sections of the work, resulting in extra expenses and project delays.
Permit-Related Delays and Cost Implications
Delays in obtaining permits can significantly impact the project timeline and budget. Common causes include incomplete applications, missing documentation, and appeals processes. These delays can result in extended project timelines, leading to increased labor costs for the contractor and potential financial penalties if the project completion date is missed. For example, a two-week delay in obtaining a permit might result in an additional $1000-$2000 in labor costs for a mid-sized commercial project, depending on the contractor’s hourly rates and crew size. Furthermore, inclement weather during these delays can cause additional setbacks and potentially lead to higher material costs if materials are damaged or need replacement. It’s important to submit complete and accurate applications promptly to minimize the risk of such delays.
Typical Permitting Process and Associated Fees
The typical permitting process involves submitting a detailed application, including architectural plans, specifications of materials, and proof of contractor licensing. The application is then reviewed by the local building department, which may require additional information or clarifications. Once the application is approved, the permit is issued, and inspections are scheduled at various stages of the project. Fees are typically paid upfront when submitting the application. A typical breakdown might include a base permit fee, fees for each inspection, and potential additional fees for expedited review or plan review. Detailed fee schedules are usually available on the local building department’s website or can be obtained by contacting them directly.
Finding and Choosing a Contractor
Selecting the right contractor is crucial for a successful flat roof installation. A poorly chosen contractor can lead to cost overruns, substandard workmanship, and lengthy disputes. Thorough research and careful consideration are essential to ensure a smooth and satisfactory project.
Contractor Pricing Strategies
Contractors employ various pricing strategies. Some may offer fixed-price contracts, providing a total cost upfront. Others might use a time-and-materials approach, billing for labor and materials separately. A third approach involves unit pricing, where the contractor charges per square foot of roofing installed. Comparing these different approaches requires careful analysis of the scope of work included in each quote to avoid unfair comparisons. For instance, a fixed-price contract might seem cheaper initially but may exclude certain essential aspects, ultimately costing more in the long run. A time-and-materials contract offers transparency but carries the risk of unexpected cost increases if the project takes longer than anticipated. Unit pricing offers a simple calculation but can overlook complexities that might inflate the final cost.
The Importance of Multiple Quotes
Obtaining multiple quotes from different contractors is paramount. This allows for a direct comparison of pricing, proposed materials, and projected timelines. It also helps to identify potential red flags, such as unusually low bids that might indicate compromised quality or hidden costs. For example, obtaining three quotes for a similar-sized project will provide a realistic range of costs and help you identify any outliers that require further investigation. This competitive bidding process safeguards against overpaying and ensures you receive a fair price.
Factors for Selecting a Reputable Contractor
Several factors contribute to selecting a reputable contractor. These include verifying licensing and insurance, checking online reviews and testimonials, assessing experience with similar projects, and confirming references. A licensed and insured contractor demonstrates compliance with industry standards and provides protection against potential liabilities. Positive online reviews and testimonials highlight customer satisfaction and project quality. Experience in handling projects of similar size and complexity ensures the contractor possesses the necessary expertise. Checking references allows direct communication with previous clients to gain firsthand insights into the contractor’s work ethic and professionalism.
Checklist of Questions for Potential Contractors
A well-prepared checklist of questions helps ensure a thorough assessment of potential contractors. This includes inquiries about their experience, licensing and insurance, the materials they use, their warranty offerings, their project timeline, their payment terms, and their approach to handling potential problems. Asking about specific aspects of the project, such as the type of roofing system proposed, its lifespan, and the maintenance requirements, allows for informed decision-making. Clarifying the payment schedule and any potential penalties for delays ensures transparency and protects your financial interests. Inquiring about their problem-solving approach helps gauge their preparedness to handle unforeseen complications.
Hidden Costs and Unexpected Expenses
Flat roof installation, while seemingly straightforward, can harbor unexpected costs that significantly inflate the final bill. These hidden expenses often stem from unforeseen circumstances or complexities revealed only during the project’s execution. Understanding these potential additions is crucial for accurate budgeting and avoiding financial surprises.
Flat roof installation price – Unforeseen circumstances frequently impact the final price of a flat roof installation. These can range from discovering underlying structural issues to encountering unexpected material shortages or encountering difficult-to-access areas. Proper planning and thorough site assessments are essential to mitigate these risks, but even with careful preparation, some unforeseen events are inevitable. Accurate cost estimations often rely on assumptions about the existing conditions, which may not always reflect reality. Delays caused by these unforeseen issues can also contribute to higher costs due to extended labor and material holding fees.
Unexpected Material Costs
Unexpected increases in material costs can significantly impact the project’s budget. For instance, a sudden surge in the price of roofing membrane due to supply chain disruptions or material defects requiring replacement can lead to substantial overruns. Similarly, unforeseen damage to existing materials during demolition or unexpected quantities of materials needed due to project complexity can add considerable expense. Contingency planning that includes a buffer for potential price fluctuations is highly recommended. For example, a project initially budgeted at $10,000 might require an additional $1,500 if the cost of the roofing membrane increases by 15%.
Unexpected Labor Costs
Unforeseen complexities during the installation process often translate into increased labor costs. Discovering hidden structural damage requiring extensive repairs, for example, will necessitate additional labor hours and potentially specialized expertise, driving up the overall expense. Difficult access to the roof, such as needing specialized equipment to navigate obstacles or work in confined spaces, also contributes to higher labor costs. Unexpected weather delays further add to labor costs as workers must be paid for time spent waiting for favorable conditions. A project initially estimated to take five days might extend to seven, leading to a 40% increase in labor expenses.
Site Conditions and Unexpected Repairs
Poor site conditions can lead to numerous hidden costs. For instance, uncovering rotted decking or damaged insulation during the removal of the old roof requires extensive repairs, adding considerable expense to the project. Unexpected discoveries of asbestos or other hazardous materials necessitate specialized removal and disposal, incurring significant additional costs. The need for extensive preparation work, such as removing obstacles or stabilizing the roof structure, also contributes to increased expenses. A project might require an additional $2,000 for unexpected repairs if the existing decking is found to be severely compromised and needs complete replacement.
List of Potential Unexpected Costs and Their Likely Causes
The following list summarizes potential unexpected costs and their likely causes. While not exhaustive, it highlights common scenarios that can lead to budget overruns.
Unexpected Cost | Likely Cause |
---|---|
Increased material costs | Supply chain disruptions, material defects, inaccurate initial assessment of material needs |
Increased labor costs | Unforeseen structural issues, difficult access, weather delays, need for specialized skills |
Unexpected repairs | Hidden damage to decking, insulation, or other structural components; discovery of hazardous materials |
Permitting and inspection fees | Unexpected delays or additional requirements from local authorities |
Waste disposal costs | Unexpected quantities of waste material requiring disposal |
Payment Schedules and Financing Options
Securing funding for your flat roof installation is a crucial step. Understanding common payment schedules and available financing options will help you manage your budget effectively and choose the best approach for your project. This section will Artikel typical payment structures and financing choices, highlighting their respective advantages and disadvantages.
Common Payment Schedules for Flat Roof Installations
Payment schedules for flat roof installations typically involve a series of installments tied to project milestones. A common approach is a three-part structure: an initial deposit, a progress payment upon completion of a significant portion of the work (e.g., after the tear-off and decking are finished), and a final payment upon project completion and successful inspection. The exact percentages allocated to each payment will vary depending on the contractor and the project’s complexity. Some contractors may offer alternative schedules, such as smaller, more frequent payments spread throughout the project duration. It’s essential to review the contract carefully to understand the payment schedule and ensure it aligns with your budget and expectations.
Financing Options for Larger Flat Roof Projects
For larger or more expensive flat roof projects, securing financing might be necessary. Several options exist, including home equity loans, personal loans, and contractor financing programs. Home equity loans use the equity in your home as collateral, potentially offering lower interest rates but risking your home if you default. Personal loans are unsecured, meaning they don’t require collateral but may come with higher interest rates. Contractor financing programs, offered directly by some contractors or through partnering financial institutions, provide specialized financing tailored to home improvement projects. These programs may offer flexible payment plans and potentially lower interest rates than other options.
Benefits and Drawbacks of Different Payment Methods
Each payment method has its own advantages and disadvantages. For instance, paying upfront in full might offer a discount, but it requires having a significant sum available immediately. Staggered payments spread the cost over time, making larger projects more manageable but potentially increasing the total cost due to interest charges. Financing options, while helpful for budgeting, can lead to higher overall expenses due to interest payments. Carefully weighing these factors is crucial to selecting the best approach for your individual circumstances.
Comparison of Financing Options from Different Lenders
Comparing financing options from various lenders is critical. Interest rates, loan terms, and fees can vary significantly. Consider factors like the annual percentage rate (APR), the length of the loan term, and any associated prepayment penalties. It’s advisable to obtain quotes from multiple lenders—banks, credit unions, and online lenders—to compare offers and select the most favorable option. Checking your credit score beforehand is also recommended, as it influences the interest rates offered by lenders. For example, a credit union may offer lower rates than a large national bank, but this will depend on individual creditworthiness and the specific loan product. Shop around and compare offers carefully to secure the best terms possible.
Long-Term Cost Analysis (excluding lifespan)
Understanding the ongoing maintenance costs associated with a flat roof is crucial for budgeting and long-term financial planning. While the initial installation cost is significant, the cumulative expense of repairs and upkeep over the roof’s operational life can be substantial. This section details potential repair costs and strategies for minimizing these expenses.
Ongoing maintenance significantly impacts the overall cost of flat roof ownership. Neglecting regular inspections and timely repairs can lead to escalating expenses and potentially catastrophic failures, resulting in far greater costs than proactive maintenance. A proactive approach, however, can mitigate many of these risks.
Potential Repair Costs Over a Roof’s Operational Life
Predicting exact repair costs is difficult, as it depends heavily on factors such as weather conditions, roof material, and the quality of the initial installation. However, we can illustrate potential scenarios. Common repairs include addressing leaks, repairing punctures, replacing damaged flashing, and addressing ponding water.
For example, a small leak might cost a few hundred dollars to repair, involving sealant application and minor patching. However, a larger leak, if left unaddressed, could necessitate extensive repairs involving the replacement of sections of roofing membrane, potentially costing thousands of dollars. Similarly, damage from severe weather, such as hail or strong winds, could result in significant repair expenses, ranging from several hundred to tens of thousands of dollars depending on the extent of the damage.
Strategies for Minimizing Long-Term Maintenance Expenses
Implementing preventative maintenance significantly reduces long-term costs. This includes regular inspections (at least annually), prompt attention to minor issues before they escalate, and ensuring proper drainage to prevent ponding water. Choosing high-quality materials during installation also contributes to longevity and reduces the frequency of repairs. Furthermore, investing in a quality warranty can provide significant protection against unforeseen expenses.
Regular cleaning of debris and vegetation from the roof surface also prevents premature wear and tear. This simple act can significantly extend the life of the roofing membrane and reduce the need for costly repairs. Professional inspections, conducted by experienced roofing contractors, can identify potential problems before they become major issues, saving considerable expense in the long run.
Hypothetical Scenario: Potential Repair Costs Over 10 Years
Let’s consider a hypothetical scenario for a medium-sized flat roof (approximately 2000 square feet) installed with a TPO membrane.
Year | Repair/Maintenance Item | Estimated Cost |
---|---|---|
1 | Annual Inspection and Minor Sealant Repairs | $300 |
3 | Flashing Repair around a chimney | $800 |
5 | Minor Leak Repair (sealant and patching) | $500 |
7 | Cleaning and debris removal | $200 |
10 | Extensive repair due to ponding water damage (partial membrane replacement) | $3000 |
Total (10 years) | $4800 |
This hypothetical scenario demonstrates that even with proactive maintenance, unexpected repairs can still occur, resulting in significant expenses over a decade. The actual costs will vary based on numerous factors, emphasizing the importance of budgeting for potential repairs.
Regional Price Variations
The cost of flat roof installation varies significantly across different regions of the country. This variation is influenced by a complex interplay of factors, primarily related to labor costs, material availability and local market conditions. Understanding these regional differences is crucial for homeowners and businesses planning a flat roof installation project to accurately budget and compare contractor bids.
Factors Contributing to Regional Price Differences
Several key factors contribute to the disparity in flat roof installation costs across different regions. Labor costs, a significant component of overall project expense, fluctuate based on local economic conditions, unionization rates, and the demand for skilled labor. Areas with high concentrations of construction activity or a shortage of qualified installers tend to have higher labor costs. Similarly, material availability and transportation costs play a crucial role. Regions with limited access to suppliers or experiencing transportation bottlenecks may see inflated material prices. Furthermore, local regulations, permitting fees, and the prevalence of specific building codes can also influence the final cost.
Examples of Regional Price Variations
Consider the example of comparing flat roof installation costs in New York City versus those in rural areas of the Midwest. New York City, with its high demand for skilled labor and expensive building materials, generally experiences significantly higher installation costs than smaller towns in the Midwest. The higher cost of living and increased competition for skilled workers in metropolitan areas like New York City directly translate to higher labor rates. Conversely, rural areas often benefit from lower labor costs and potentially easier access to certain materials, resulting in lower overall installation expenses. Coastal regions, particularly those prone to hurricanes or other severe weather, might see higher costs due to the need for more robust and expensive roofing materials designed to withstand extreme conditions.
Regional Price Variation Map
A visual representation of regional price variations would be a thematic map of the United States. The map would utilize a color gradient, ranging from a light green (representing lower average installation costs) to a deep red (representing higher average installation costs). Each state or region would be colored according to its average flat roof installation cost per square foot, derived from a compilation of data from various sources, including contractor estimates, industry reports, and publicly available pricing information. For enhanced clarity, the map could incorporate a legend displaying the cost ranges associated with each color. States with significant cost variations within their boundaries could be further subdivided into smaller regions with distinct color-coding to provide a more granular representation of price differences. Cities with exceptionally high or low costs could be highlighted with labels and specific cost figures. This would allow for a quick and comprehensive overview of regional price fluctuations across the country, providing a valuable tool for prospective clients to estimate project costs in their specific location.
Clarifying Questions
What is the average lifespan of a flat roof?
The lifespan of a flat roof varies depending on the materials used, climate, and maintenance. Generally, you can expect a lifespan ranging from 15 to 30 years.
Can I finance a flat roof installation?
Yes, many contractors and lenders offer financing options for larger roofing projects. Explore options with your contractor or seek financing through home improvement loans.
How long does a flat roof installation typically take?
The installation time depends on the size and complexity of the roof. Smaller projects might take a few days, while larger ones can extend over several weeks.
What type of warranty should I expect?
Warranties vary by manufacturer and contractor. Look for warranties covering both materials and workmanship, ideally for a minimum of 10-20 years.