Understanding Flat Roof Systems
Flat roofs, while seemingly simple in design, comprise a complex system of layers working together to protect a building from the elements. Understanding the different components and their potential failure points is crucial for ensuring a long-lasting and leak-free roof. This section will explore the various types of flat roofs, their lifespans, and common causes of failure.
Types of Flat Roofs
Several types of flat roofs are employed in residential and commercial construction, each with its own characteristics and suitability for different climates and building applications. The choice of roofing material significantly impacts the roof’s lifespan and overall performance.
- Built-up Roofing (BUR): This traditional system involves multiple layers of asphalt and felt, often with a gravel or aggregate surfacing. BUR systems are known for their durability and longevity, but they are heavier than other options and require more maintenance.
- Modified Bitumen Roofing (MBR): MBR systems use modified asphalt, offering improved flexibility and durability compared to traditional BUR. They are available in various forms, including roll roofing and cap sheets, and are often easier to install than BUR.
- Single-Ply Roofing Membranes: These systems utilize large sheets of synthetic material, such as TPO (thermoplastic polyolefin), EPDM (ethylene propylene diene monomer), or PVC (polyvinyl chloride). Single-ply membranes are known for their ease of installation, lightweight nature, and excellent reflectivity.
Lifespan of Flat Roofing Materials
The lifespan of a flat roof depends heavily on the chosen material, the quality of installation, and the climate. While these are estimates, proper maintenance can significantly extend their lifespan.
- Built-up Roofing (BUR): 15-25 years
- Modified Bitumen Roofing (MBR): 15-20 years
- TPO Single-Ply Membranes: 20-30 years
- EPDM Single-Ply Membranes: 20-30 years
- PVC Single-Ply Membranes: 20-30 years
Common Causes of Flat Roof Failure
Several factors contribute to flat roof failure. Addressing these issues proactively through proper design, installation, and maintenance is key to preventing costly repairs.
- Poor Installation: Incorrect installation techniques, such as inadequate sealing or improper flashing around penetrations (such as vents and pipes), are major causes of leaks and premature failure. A poorly installed roof, regardless of the material, is prone to early degradation.
- Ponding Water: Flat roofs are designed to shed water, but inadequate slope or drainage can lead to ponding water. Stagnant water puts extra stress on the roofing membrane and can lead to deterioration and leaks. For example, a poorly designed drainage system in a large commercial building can result in significant ponding, leading to premature roof failure.
- UV Degradation: Exposure to ultraviolet (UV) radiation from the sun can degrade roofing materials over time, causing them to become brittle and crack. This is particularly true for asphalt-based roofing systems. Regular inspection and potential application of UV-resistant coatings can help mitigate this.
- Lack of Maintenance: Regular inspections and prompt repairs of minor damage are essential to prevent small problems from becoming major, costly issues. A simple crack left unrepaired can eventually lead to a larger leak and significant damage.
- Punctures and Damage: Physical damage from falling objects, foot traffic, or improperly handled equipment can compromise the integrity of the roofing membrane. Regular inspections and protective measures can help minimize this risk.
Identifying Reputable Contractors
Choosing the right contractor for your flat roof replacement is crucial for ensuring a long-lasting, leak-free roof and avoiding costly repairs down the line. A thorough vetting process will save you time, money, and potential headaches. This section Artikels key steps to help you identify reputable and qualified contractors for your project.
Selecting a qualified flat roof replacement contractor requires careful consideration of several factors. It’s not simply about finding the cheapest option; rather, it’s about finding a contractor with the necessary experience, qualifications, and a proven track record of success. This ensures a quality installation and protects your investment.
Contractor Qualifications Checklist
A comprehensive checklist should be used to assess potential contractors. This checklist helps to ensure that the chosen contractor possesses the necessary skills, experience, and insurance to undertake the job competently and safely. Failing to check these points can lead to significant problems later on.
- Years of Experience: Look for contractors with a minimum of 5-10 years of experience specifically in flat roof replacements. Experience translates to expertise and problem-solving skills.
- Specialization in Flat Roofs: Flat roofs require specialized knowledge and techniques different from sloped roofs. Ensure the contractor specializes in this type of roofing.
- References and Portfolio: Request a list of recent clients and examine their completed projects. A strong portfolio demonstrates their capabilities and attention to detail.
- Warranty Information: Inquire about the warranty offered on both materials and workmanship. A reputable contractor will stand behind their work.
- Licensing and Certifications: Verify their licensing and any relevant certifications, such as those from industry associations.
- Detailed Proposal: A comprehensive proposal should include a detailed breakdown of costs, materials, timelines, and payment schedules.
- Safety Practices: Inquire about their safety protocols and adherence to industry standards. Safety should be a top priority for any contractor.
Verifying Contractor Licenses and Insurance
Verifying a contractor’s licensing and insurance is a critical step in protecting yourself from potential liabilities. Unlicensed or uninsured contractors can leave you responsible for accidents or faulty work. This section Artikels best practices for verification.
It is essential to independently verify all provided licensing and insurance information. Contacting the relevant licensing board directly is the most reliable method to confirm the contractor’s status and ensure their license is valid and in good standing. Similarly, contacting the insurance provider to verify the policy’s coverage and validity is a crucial step in protecting your investment. Always request proof of insurance and licensing before any work commences.
- Contact the Licensing Board: Directly contact your state’s licensing board to verify the contractor’s license number and check for any disciplinary actions or complaints.
- Verify Insurance Coverage: Request a certificate of insurance (COI) that clearly states the types and amounts of coverage, including general liability and workers’ compensation.
- Check for Claims History: While not always accessible, attempting to check for a history of claims against the contractor can offer additional insight into their reliability.
Checking Customer Reviews and Testimonials
Customer reviews and testimonials offer invaluable insights into a contractor’s work quality, professionalism, and customer service. These reviews provide a real-world perspective that supplements the contractor’s self-reported qualifications. This section highlights the importance of this step.
Thoroughly reviewing online reviews on platforms like Google My Business, Yelp, and Angie’s List can provide a comprehensive understanding of the contractor’s reputation. Pay close attention to both positive and negative feedback, looking for patterns or recurring themes. Be wary of contractors with overwhelmingly positive reviews without any negative ones, as this may indicate fabricated reviews. Look for reviews that detail specific aspects of the contractor’s work, such as communication, punctuality, cleanup, and overall quality.
The Bidding and Contract Process
Securing a new flat roof involves careful consideration of bids and the subsequent contract. Understanding the process ensures a smooth project and protects your investment. This section details the key elements of a successful bidding and contracting experience for your flat roof replacement. It covers the structure of a comprehensive bid, essential contract terms, and various payment options.
The bidding and contract process is crucial for a successful flat roof replacement. A well-structured bid clarifies the scope of work, materials, and costs, while a clear contract protects both the homeowner and the contractor.
Sample Flat Roof Replacement Contract
This sample contract Artikels essential terms and conditions. Remember, this is a sample and should be reviewed and potentially adapted by legal counsel to fit your specific circumstances. Always have a lawyer review any contract before signing.
Flat Roof Replacement Contract
This Agreement, made this [Date], between [Contractor Name], hereinafter referred to as “Contractor,” and [Homeowner Name], hereinafter referred to as “Homeowner,” for the replacement of the flat roof located at [Address].
1. Scope of Work: The Contractor shall replace the existing flat roof with [Type of roofing material], including [List of included tasks, e.g., tear-off, substrate preparation, installation, flashing, etc.].
2. Materials: The Contractor shall use [Specific materials and manufacturers].
3. Payment Terms: [Specify payment schedule, e.g., 25% deposit upon signing, 50% upon completion of tear-off and substrate preparation, 25% upon completion of roofing installation].
4. Warranty: The Contractor warrants the workmanship for [Number] years and the materials for [Number] years.
5. Permits: The Contractor shall obtain all necessary permits.
6. Timeline: The project shall be completed within [Number] days, commencing on [Start Date].
7. Dispute Resolution: Any disputes shall be resolved through [Method of dispute resolution, e.g., mediation, arbitration].
8. Termination Clause: Either party may terminate this contract with [Number] days’ written notice.
IN WITNESS WHEREOF, the parties have executed this Agreement as of the date first written above.
_________________________ _________________________
Contractor Signature Homeowner Signature
_________________________ _________________________
Printed Name Printed Name
Essential Elements of a Comprehensive Bid Proposal
A comprehensive bid proposal should provide clarity and detail, preventing misunderstandings later. Key elements include a detailed scope of work, specifications of materials, a precise timeline, payment terms, and warranty information. It should also include the contractor’s licensing and insurance information.
- Detailed Scope of Work: A precise description of all tasks involved, including tear-off, substrate preparation, installation, and cleanup.
- Materials Specification: Specific details about the roofing materials to be used, including manufacturer, model, and warranty information.
- Project Timeline: A realistic estimate of the project duration, including start and completion dates.
- Payment Schedule: A clear Artikel of payment terms, including percentages and due dates.
- Warranty Information: Details about the warranty provided for both workmanship and materials.
- Contractor Information: Licensing, insurance, and contact details.
- References: Contact information for previous clients.
Comparison of Contract Payment Structures
Different payment structures offer varying levels of risk and protection for both the homeowner and contractor. Choosing the right structure depends on the project size, contractor reputation, and homeowner comfort level.
Payment Structure | Advantages | Disadvantages |
---|---|---|
Upfront Payment | Simple for contractor | High risk for homeowner |
Progress Payments | Balances risk for both parties | Requires more detailed monitoring |
Final Payment | Low risk for homeowner | High risk for contractor |
Materials and Their Properties
Choosing the right roofing material is crucial for the longevity and performance of your flat roof. The selection depends on factors such as budget, climate, and the building’s specific needs. Different materials offer varying levels of durability, maintenance requirements, and lifespan. Understanding these differences is key to making an informed decision.
Flat roof replacement contractors – This section details the advantages and disadvantages of common flat roofing materials, allowing you to compare their properties and suitability for your project.
TPO Roofing Membranes
Thermoplastic Polyolefin (TPO) membranes are a popular choice for flat roofs due to their excellent durability and relatively low cost. TPO is a single-ply roofing system that’s lightweight, easy to install, and highly resistant to punctures and tears. Its seamless design minimizes the risk of leaks, and it offers good reflectivity, reducing the building’s energy consumption. However, TPO can be susceptible to UV degradation over time, necessitating regular inspections and potential repairs. Extreme temperature fluctuations can also affect its performance.
EPDM Roofing Membranes
Ethylene Propylene Diene Monomer (EPDM) rubber roofing is another widely used single-ply membrane known for its exceptional longevity and flexibility. EPDM is highly resistant to UV rays, ozone, and many chemicals, making it a durable and long-lasting option. It’s relatively easy to install and repair, and its elasticity allows it to accommodate building movement. However, EPDM can be susceptible to punctures from sharp objects and may require more seams than TPO, potentially increasing the risk of leaks. The material is also less reflective than TPO, leading to potentially higher cooling costs in hot climates.
PVC Roofing Membranes
Polyvinyl Chloride (PVC) roofing membranes are known for their exceptional strength and resistance to punctures and tears. PVC is also highly resistant to UV radiation and chemicals. It offers excellent reflectivity, helping to reduce energy costs. PVC membranes are typically reinforced with polyester fabric for added strength and durability. However, PVC can be more expensive than TPO or EPDM and can be more challenging to install due to its higher rigidity.
Modified Bitumen Roofing
Modified bitumen roofing systems are composed of asphalt-based materials modified with polymers like SBS (Styrene-Butadiene-Styrene) or APP (Atactic Polypropylene). These modifications enhance the roofing material’s flexibility, durability, and resistance to temperature extremes. Modified bitumen is a cost-effective option that offers good waterproofing properties. However, it requires more specialized installation techniques and may not be as long-lasting as other single-ply options like TPO or EPDM. It’s also less reflective than TPO or PVC.
Comparison of Flat Roofing Materials, Flat roof replacement contractors
Material | Cost (Relative) | Durability (Years) | Maintenance |
---|---|---|---|
TPO | Medium | 15-20 | Low to Moderate |
EPDM | Medium | 20-30 | Low to Moderate |
PVC | High | 20-30+ | Low |
Modified Bitumen | Low | 10-15 | Moderate |
The Replacement Process
Replacing a flat roof is a complex process requiring meticulous planning and execution. A successful project hinges on careful preparation, skilled labor, and the use of high-quality materials. The following steps Artikel a typical flat roof replacement, highlighting key considerations at each stage.
The entire process, from initial assessment to final cleanup, typically involves several key phases. Each phase requires attention to detail to ensure the longevity and performance of the new roof system.
Project Assessment and Preparation
Before any demolition begins, a thorough assessment of the existing roof is crucial. This includes identifying the extent of damage, determining the cause of any problems (e.g., water damage, poor insulation), and assessing the structural integrity of the underlying deck. The contractor should then create a detailed plan outlining the scope of work, materials required, and a realistic timeline. This plan should also detail waste disposal procedures, ensuring compliance with local regulations. Proper preparation, including securing necessary permits, is vital for a smooth and legal project. This phase often involves taking detailed measurements and photographs to inform the material ordering process and to document the existing conditions for insurance purposes.
Removal of Existing Roofing System
Careful removal of the old roofing system is essential. This process typically involves removing the existing roofing membrane, insulation, and any damaged decking. Debris must be carefully managed and disposed of responsibly, adhering to all environmental regulations. Workers should exercise caution during this phase to avoid damage to the underlying structure or injury to themselves. Safety harnesses and fall protection are crucial given the height involved. The removal process should be documented photographically to provide a clear record of the work completed.
Deck Inspection and Repair
Once the old roofing system is removed, a thorough inspection of the underlying deck is necessary. Any damaged or deteriorated sections of the deck must be repaired or replaced before the new roofing system is installed. This might involve replacing damaged plywood sheathing, repairing cracks, or addressing any structural issues. This step is crucial to ensure the long-term stability and performance of the new roof. Proper deck preparation is often overlooked, yet it directly impacts the lifespan of the new roof.
Installation of Underlayment
Proper underlayment installation is critical for preventing water damage. The underlayment acts as a secondary waterproof barrier, protecting the deck and the new roofing membrane from moisture intrusion. The underlayment should be installed according to the manufacturer’s instructions, ensuring proper overlap and sealing of seams. This layer adds an extra layer of protection, significantly extending the life of the new roof. Different types of underlayment offer varying degrees of protection and should be selected based on the specific climate and the type of roofing membrane being used.
Installation of New Roofing Membrane
The new roofing membrane is then installed over the prepared deck and underlayment. This process involves carefully adhering the membrane to the surface, ensuring a seamless and watertight seal. The specific installation techniques vary depending on the type of membrane being used (e.g., EPDM, TPO, PVC). Proper installation is crucial to ensure the longevity and performance of the new roof. The contractor should follow the manufacturer’s specifications carefully to ensure a proper installation and to maintain the warranty. This often involves using specialized tools and equipment to ensure accurate measurements and consistent application.
Final Inspection and Cleanup
Upon completion of the installation, a final inspection is conducted to ensure that the new roof meets all specifications and is free of defects. This inspection might involve checking for proper drainage, ensuring the seams are sealed, and verifying the overall quality of the workmanship. Any necessary repairs are made before the final cleanup. The site should be left clean and free of debris, with all materials properly disposed of. A final walk-through with the client is often conducted to address any questions or concerns.
Safety Precautions
Throughout the entire replacement process, safety is paramount. Contractors should adhere to all relevant safety regulations and guidelines. This includes using appropriate personal protective equipment (PPE), such as hard hats, safety glasses, and fall protection equipment. Proper training and supervision of workers are essential to minimize the risk of accidents. Regular safety meetings should be held to reinforce safe work practices and address any potential hazards. The use of proper lifting techniques and equipment is crucial to prevent injuries. Detailed safety plans should be developed and followed to ensure a safe work environment for all personnel.
Warranty and Maintenance
Protecting your investment in a new flat roof involves understanding the warranties offered and committing to a regular maintenance schedule. A well-maintained flat roof can significantly extend its lifespan and avoid costly repairs down the line. This section details standard warranties and provides a practical maintenance plan.
Manufacturers of reputable flat roofing materials, such as TPO (Thermoplastic Polyolefin), EPDM (Ethylene Propylene Diene Monomer), and PVC (Polyvinyl Chloride), typically offer warranties ranging from 10 to 20 years, sometimes even longer depending on the specific product and installation. These warranties generally cover defects in materials and workmanship, but specific terms and conditions vary. It’s crucial to carefully review the warranty documentation provided by your contractor and manufacturer to understand the extent of coverage. For example, a 20-year warranty might cover material defects but require the homeowner to maintain the roof according to specified guidelines to remain valid. A shorter warranty might offer a pro-rated coverage, meaning the manufacturer’s responsibility decreases over time.
Standard Warranties for Flat Roofing Materials
Standard warranties for flat roofing materials typically cover defects in manufacturing and materials. However, these warranties often have conditions, such as proper installation by a certified contractor and adherence to a regular maintenance schedule. The length of the warranty can vary greatly depending on the manufacturer and the specific product. For instance, a high-performance TPO membrane might have a 20-year warranty, while a less expensive EPDM membrane might only offer a 15-year warranty. These warranties usually don’t cover damage caused by extreme weather events, improper maintenance, or vandalism. It’s important to note that the warranty is typically non-transferable unless explicitly stated otherwise.
The Importance of Regular Roof Inspections and Maintenance
Regular inspections and preventative maintenance are essential for maximizing the lifespan of your flat roof and ensuring the warranty remains valid. Neglecting maintenance can lead to premature deterioration, leaks, and costly repairs. Early detection of potential problems, such as minor punctures or loose seams, allows for timely intervention and prevents significant damage. Regular inspections also help identify potential issues before they escalate into major problems, saving you time and money in the long run. For example, a small crack in a seam that’s identified and sealed during a routine inspection can prevent a much larger leak later on.
Sample Maintenance Schedule for Different Flat Roof Types
A proactive maintenance schedule is crucial for prolonging the life of your flat roof. The specific tasks will vary slightly depending on the type of roofing material.
Below is a sample maintenance schedule, but it’s recommended to consult with your roofing contractor for a tailored plan based on your specific roof and climate:
Roof Type | Annual Inspection | Every 2-3 Years | Every 5-7 Years |
---|---|---|---|
TPO | Visual inspection for punctures, debris, and loose seams. Clean debris and check for proper drainage. | Thorough cleaning with appropriate cleaning solutions. Check for any signs of wear and tear. | Consider professional inspection and potential recoating depending on condition. |
EPDM | Visual inspection for punctures, tears, and blisters. Clean debris and check for proper drainage. | Thorough cleaning and inspection for cracks or deterioration. Address any minor repairs promptly. | Professional inspection and potential recoating or repair depending on condition. |
PVC | Visual inspection for punctures, debris, and loose seams. Clean debris and check for proper drainage. | Thorough cleaning with appropriate cleaning solutions. Check for any signs of wear and tear. | Professional inspection and potential recoating or repair depending on condition. |
Cost Estimation and Budgeting
Accurately estimating the cost of a flat roof replacement is crucial for both homeowners and contractors. A well-defined budget ensures the project proceeds smoothly and avoids unexpected financial burdens. This section details the process of creating a comprehensive cost estimate and managing expenses throughout the project lifecycle.
Flat Roof Replacement Cost Estimation Worksheet
This worksheet helps organize the various cost components of a flat roof replacement. Accurate figures are essential for a realistic budget. Remember to obtain multiple quotes from reputable contractors to compare pricing and services.
Cost Component | Estimated Cost | Notes |
---|---|---|
Materials (roofing membrane, insulation, flashing, etc.) | $ | Specify materials and quantities. Include disposal fees for old materials. |
Labor (removal of old roof, installation of new roof, cleanup) | $ | Obtain detailed labor quotes from multiple contractors. |
Permits and Inspections | $ | Check with your local authority for permit fees and inspection schedules. |
Contingency (for unforeseen expenses) | $ (10-15% of total estimated cost) | Allocate a percentage for potential unexpected issues. |
Subtotal | $ | Sum of all costs above. |
Sales Tax (if applicable) | $ | Add applicable sales tax to the subtotal. |
Total Estimated Cost | $ | Final cost including all expenses. |
Factors Influencing Flat Roof Replacement Costs
Several factors significantly impact the overall cost of a flat roof replacement project. Understanding these elements allows for more accurate budgeting and informed decision-making.
- Roof Size and Complexity: Larger roofs naturally require more materials and labor, increasing the cost. Complex designs with multiple levels or unusual shapes also add to the expense.
- Roofing Material Selection: Different roofing materials vary greatly in price. TPO membranes are generally more affordable than EPDM or single-ply PVC membranes. The choice of insulation type and thickness also affects the cost.
- Labor Rates: Labor costs are influenced by geographical location, contractor experience, and project demand. Areas with higher labor costs will result in a more expensive project.
- Existing Roof Condition: The condition of the existing roof significantly impacts the cost. Extensive damage requiring extensive repairs or complete removal increases the overall expense.
- Permits and Inspections: Permit fees and inspection costs vary by location and project scope. These costs should be factored into the budget.
- Additional Services: Any additional services, such as repairs to the roof deck, installation of new flashing, or gutter work, will increase the overall project cost.
Expense Management and Tracking
Effective expense management is vital for successful project completion. Maintaining detailed records ensures that the budget remains on track and avoids cost overruns.
Regularly review and update the budget throughout the project. Compare actual expenses against the estimated costs. Identify any discrepancies and take corrective action promptly. Utilize accounting software or spreadsheets to track expenses meticulously. Maintain all receipts and invoices as proof of payments. Open a dedicated bank account for the project to streamline financial management.
For example, a project initially budgeted at $20,000 might experience a 5% increase in material costs due to unforeseen market fluctuations. Tracking these changes allows for adjustments to the budget and prevents unexpected financial shortfalls. Similarly, unexpected repairs to the roof deck, not initially included in the estimate, should be documented and accounted for to maintain budget transparency.
Dealing with Potential Problems: Flat Roof Replacement Contractors
Flat roof replacement projects, while offering significant improvements to building longevity and protection, can present unforeseen challenges. Understanding potential problems and having strategies in place for mitigation and resolution is crucial for a successful project. This section Artikels common issues, methods for handling unexpected situations, and approaches to resolving disputes.
Unexpected problems can significantly impact the project timeline and budget. Proactive planning and clear communication between the homeowner and the contractor are essential to minimize disruption and maintain a positive outcome.
Common Problems and Their Solutions
Several common issues can arise during flat roof replacements. These range from material defects to unforeseen structural problems. Addressing these effectively requires a combination of careful planning, skilled workmanship, and open communication.
- Material Defects: Damaged or substandard roofing materials can lead to leaks and premature failure. Solutions involve rigorous inspection of materials upon delivery, detailed documentation of any defects, and insistence on replacement with compliant materials by the contractor.
- Unforeseen Structural Issues: Underlying structural problems, such as deteriorated decking or inadequate insulation, may be discovered during demolition. Solutions necessitate a thorough pre-project inspection, potentially involving structural engineers, and agreement on revised plans and costs to address these issues.
- Weather Delays: Adverse weather conditions can significantly delay the project. Solutions include careful scheduling to avoid peak storm seasons, contingency plans for inclement weather, and clear contractual clauses addressing weather-related delays.
- Workmanship Issues: Poor workmanship can result in leaks, uneven surfaces, and premature roof failure. Solutions include regular site inspections, detailed photographic documentation of the work progress, and adherence to strict quality control measures.
Handling Unexpected Issues or Delays
Unexpected problems are inevitable in construction. Effective strategies for handling these issues include: Maintaining open communication with the contractor, documenting all changes and delays, and having a clear understanding of the contract’s provisions regarding change orders and extensions. For example, if unexpected water damage is discovered under the existing roofing, the contractor should provide a detailed assessment, proposed solution, and revised cost estimate before proceeding. This ensures transparency and prevents disputes.
Resolving Disputes or Conflicts with Contractors
Disputes can arise from various sources, including cost overruns, scheduling delays, or unsatisfactory workmanship. Effective strategies for conflict resolution include: Reviewing the contract carefully, documenting all communication and concerns, attempting to resolve issues through direct communication with the contractor, and, if necessary, seeking mediation or arbitration as Artikeld in the contract or through legal channels. For instance, if a significant discrepancy arises between the agreed-upon price and the final invoice, presenting detailed documentation, such as initial quotes, change orders, and payment records, can strengthen your position during negotiations or legal proceedings.
Choosing the Right Roofing System
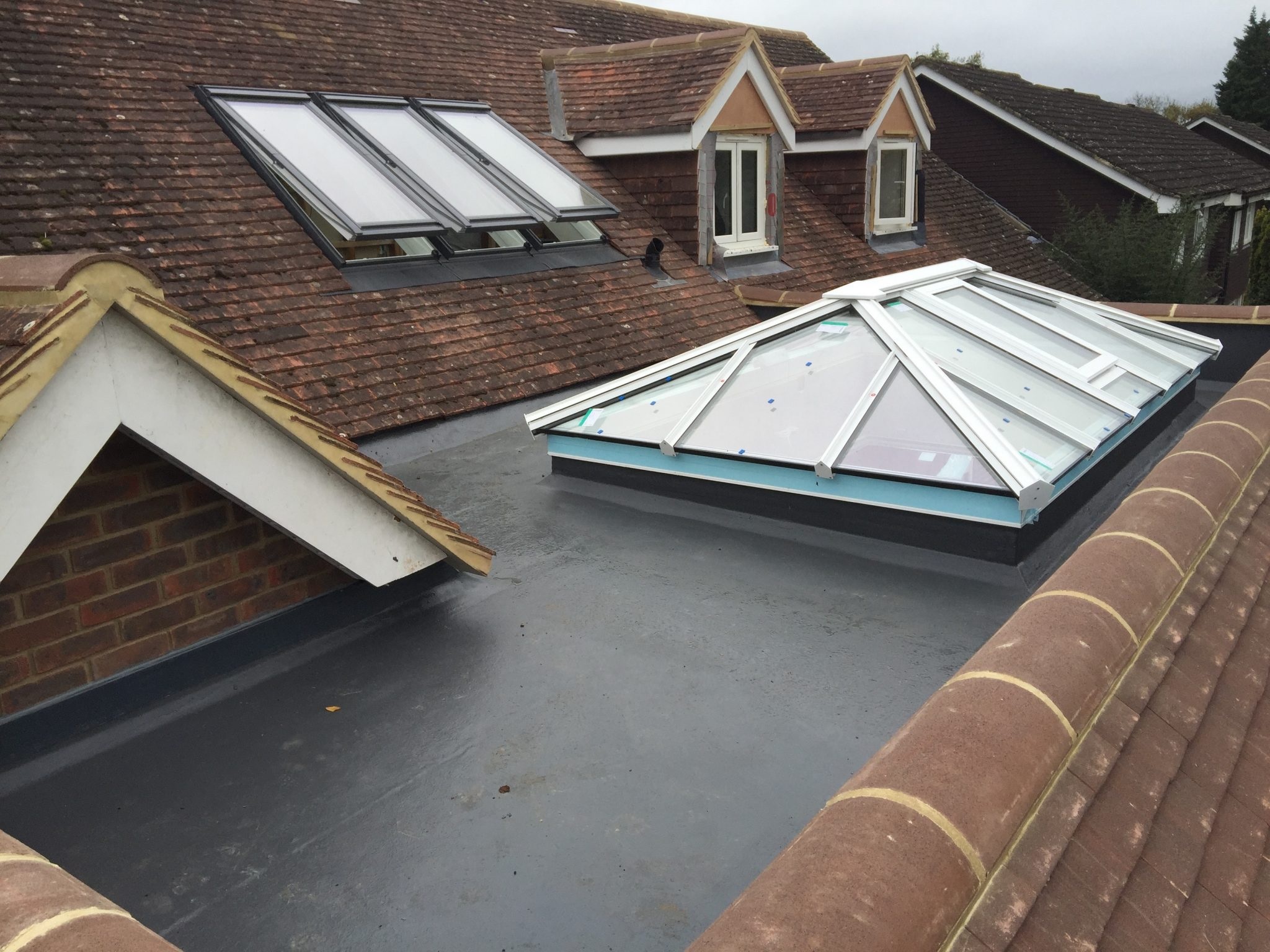
Selecting the optimal flat roofing system for your building requires careful consideration of several factors. The ideal choice depends on your specific climate, the type of building, and your budget. A well-informed decision will ensure a long-lasting, cost-effective, and trouble-free roof.
Choosing the right roofing system involves weighing the advantages and disadvantages of various options. Each system offers a unique balance of durability, cost, lifespan, and maintenance requirements. Understanding these trade-offs is crucial for making an informed decision that aligns with your long-term goals and financial resources.
Flat Roofing System Comparisons
Different flat roofing systems exhibit varying performance characteristics depending on climatic conditions. For instance, in regions with heavy snowfall, a system capable of withstanding significant weight and water accumulation, such as a modified bitumen system, might be preferred over a single-ply membrane system that could be more susceptible to damage under heavy loads. Conversely, in arid climates with intense sun exposure, a highly reflective membrane like a white TPO membrane could be beneficial to reduce heat absorption and energy costs. Building type also plays a crucial role. A large commercial building might necessitate a robust and durable system like a built-up roof (BUR), while a smaller residential structure could benefit from the faster installation and lower cost of a single-ply membrane. Budget constraints often dictate the final decision. While BUR systems and other high-performance options offer superior longevity, they often come with a higher upfront cost compared to more economical choices like EPDM or PVC membranes.
A Decision-Making Flowchart for Flat Roof System Selection
The selection process can be streamlined using a flowchart. This visual aid helps to systematically assess different factors and arrive at an informed decision.
[Imagine a flowchart here. The flowchart would start with a decision point: “What is your budget?”. Branches would lead to different options: “High,” “Medium,” “Low.” Each budget branch would then have further decision points: “What is your climate like?”, with branches for “Hot/Dry,” “Cold/Snowy,” “Moderate.” Each climate branch would then lead to recommendations for specific roofing systems (e.g., TPO for hot/dry, modified bitumen for cold/snowy). Finally, the flowchart would conclude with a decision box: “Recommended Roofing System: [System Name].”]
Long-Term Cost-Effectiveness Assessment
Assessing the long-term cost-effectiveness requires considering not only the initial investment but also factors like lifespan, maintenance costs, and energy efficiency. For example, a more expensive, high-performance system with a longer lifespan (e.g., 30+ years) and lower maintenance requirements might prove more cost-effective over its lifetime compared to a less expensive system requiring more frequent repairs and replacements over a shorter period (e.g., 15-20 years). A detailed cost analysis, including projections for future maintenance and repairs, is essential for comparing different options accurately. This analysis should consider factors such as material costs, labor costs, warranty coverage, and the potential impact on energy bills due to differences in reflectivity and insulation properties. For instance, a highly reflective membrane can reduce cooling costs significantly in hot climates, offsetting some of the higher initial investment.
Clarifying Questions
What is the average lifespan of a flat roof?
The lifespan of a flat roof varies depending on the materials used and the climate. Generally, it ranges from 15 to 30 years.
How can I tell if my flat roof needs replacing?
Signs of a failing flat roof include leaks, ponding water, blistering, cracks, and significant wear and tear. A professional inspection is recommended.
What type of warranty should I expect?
Reputable contractors and manufacturers offer warranties that typically cover material defects and workmanship for a specified period, often 10-20 years.
Are there financing options available for roof replacement?
Yes, many contractors offer financing plans or work with lenders to help homeowners manage the cost of a roof replacement.