Factors Affecting Insulation Installation Cost
Several key factors influence the overall cost of insulation installation. Understanding these variables allows for more accurate budgeting and informed decision-making during the home improvement process. This includes considering the type of insulation material, the size and complexity of the home, and the accessibility of the areas requiring insulation.
Insulation Material Costs
The type of insulation chosen significantly impacts the project’s cost. Fiberglass, cellulose, and spray foam are common options, each with varying price points and performance characteristics. Fiberglass batts are generally the most affordable, offering good insulation value for the price. Cellulose insulation, made from recycled paper, provides excellent thermal performance and is often a more environmentally friendly choice, though its cost might be slightly higher than fiberglass. Spray foam insulation, while more expensive upfront, offers superior air sealing and insulation properties, leading to long-term energy savings. The cost differences reflect the materials’ manufacturing processes, installation techniques, and resulting energy efficiency. For example, a 1500 sq ft home might see a cost difference of $1000-$2000 between fiberglass and spray foam installation.
Home Size and Complexity
The size of the home directly correlates with the amount of insulation needed, thus influencing the overall cost. Larger homes naturally require more material and labor, increasing the expense. Beyond square footage, the home’s design and construction also play a role. Multi-story homes, for instance, often present more challenges for installers, potentially increasing labor costs. Similarly, homes with complex rooflines or difficult-to-access areas will add to the overall expense. A simple single-story ranch will generally be less expensive to insulate than a two-story colonial with numerous dormers and cathedral ceilings.
Accessibility and Installation Complexity
Accessibility significantly affects installation costs. Insulating an easily accessible attic is typically less expensive than insulating walls, which often requires more labor-intensive methods such as drilling holes or removing sections of drywall. The presence of existing obstacles, such as plumbing or electrical wiring, further complicates the installation and adds to the overall cost. For example, retrofitting insulation into existing wall cavities is more expensive than installing it during new construction.
Installation Cost Comparison by Home Type
The following table provides estimated costs for insulation installation in different home types. These are estimates and actual costs can vary based on location, contractor, and specific project details.
Home Type | Average Square Footage | Estimated Fiberglass Batt Installation Cost | Estimated Spray Foam Installation Cost |
---|---|---|---|
Single-Story Ranch | 1500 sq ft | $2000 – $3500 | $5000 – $8000 |
Two-Story Colonial | 2500 sq ft | $3500 – $6000 | $8000 – $15000 |
Multi-Story Home | 3500 sq ft | $5000 – $8000 | $12000 – $20000 |
Split-Level | 2000 sq ft | $3000 – $5000 | $7000 – $12000 |
Labor Costs Associated with Insulation Installation
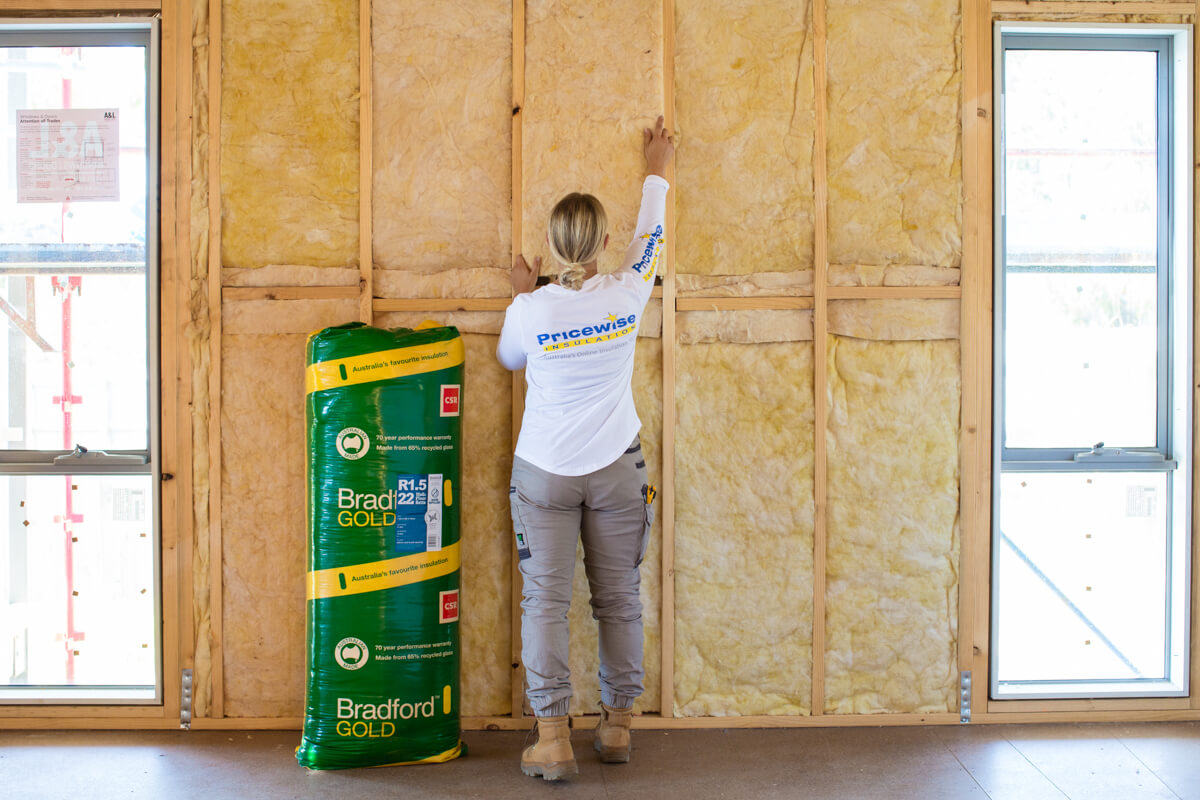
Labor costs represent a significant portion of the overall expense for insulation installation. Understanding these costs, including regional variations and potential hidden expenses, is crucial for accurate budgeting. This section will detail the various factors influencing labor costs, providing insights to help homeowners and contractors alike.
How much is it to install insulation – Hourly rates for insulation installers vary considerably across the country, influenced by factors such as local market conditions, the installer’s experience and specialization, and the type of insulation being installed. In general, expect to see higher rates in areas with a higher cost of living and a greater demand for skilled labor. For example, metropolitan areas on the coasts tend to have higher labor costs compared to smaller towns in the Midwest. While precise figures fluctuate, a reasonable range for hourly rates might be between $40 and $80, with specialized installers commanding higher fees. This range can significantly increase depending on the project’s complexity.
Hourly Rates for Insulation Installers by Region
Providing precise hourly rates for every region is challenging due to constant market fluctuations. However, we can illustrate the regional variation with hypothetical examples. Consider three hypothetical regions: Region A (a high-cost coastal city), Region B (a mid-sized city in a moderately priced state), and Region C (a rural area). A skilled installer in Region A might charge $75-$90 per hour, while a similar installer in Region B might charge $55-$70 per hour, and Region C might see rates between $40-$60 per hour. These are illustrative examples and should not be considered definitive rates. Always obtain quotes from local installers for accurate pricing.
Impact of Specialized Labor on Costs
Specialized insulation installation, such as spray foam application, typically involves higher labor costs compared to standard batt or roll insulation. Spray foam requires specialized equipment, training, and safety precautions, all of which contribute to a higher hourly rate. Installers with expertise in spray foam insulation often command significantly higher hourly rates than those installing fiberglass or cellulose insulation. The increased precision and technical skill required for spray foam installation justify the higher cost. For instance, an experienced spray foam installer might charge $80-$120 per hour or more, reflecting the specialized skills and equipment needed.
Factors Leading to Increased Labor Costs
Several factors can unexpectedly increase labor costs during an insulation project. Difficult access points, such as crawl spaces with limited headroom or attics with complex framing, significantly increase the time and effort required for installation. Unexpected issues, such as encountering asbestos or lead-based paint during the process, will necessitate additional work, specialized equipment, and potentially hazardous material removal procedures, leading to substantial cost overruns. Furthermore, projects requiring extensive demolition or preparation work before insulation can be installed will naturally add to the overall labor costs.
Common Hidden Labor Costs Associated with Insulation Projects
Beyond the basic hourly rate, several hidden labor costs can impact the final price. It’s essential to be aware of these potential additions to avoid unpleasant surprises.
- Travel Time: Installers often charge for travel time to and from the job site, especially for projects located in remote areas.
- Disposal Fees: Removing existing insulation and disposing of it properly can incur additional fees, especially if hazardous materials are involved.
- Material Handling: Moving and handling large quantities of insulation materials can add to the labor time and cost.
- Clean-up: Thorough cleaning and restoration of the work area after installation is often included in the labor costs.
- Permits and Inspections: While not directly labor costs, the time spent obtaining necessary permits and coordinating inspections can indirectly add to the overall project cost.
Material Costs for Different Insulation Types: How Much Is It To Install Insulation
Insulation material costs significantly impact the overall expense of a project. Understanding the price range per square foot for various materials, along with their respective R-values (a measure of thermal resistance), is crucial for making informed decisions. This section details the cost differences between various insulation types and explores the long-term cost-effectiveness considering energy savings. We will also examine the price differences associated with bulk versus smaller material purchases.
The price of insulation varies greatly depending on the type of material, its R-value, and the quantity purchased. Generally, higher R-values indicate better insulation, leading to lower energy bills but potentially higher upfront costs. Bulk purchases often result in lower per-unit costs, offsetting some of the initial investment. However, it’s crucial to accurately estimate your needs to avoid overspending on materials.
Insulation Material Costs and R-Values
The following table provides a price range per square foot for common insulation materials, along with their typical R-values. Note that prices can fluctuate based on location, supplier, and market conditions. These figures represent average values and should be considered estimates.
Material Type | Price Range per Square Foot | Typical R-Value per Inch |
---|---|---|
Fiberglass Batt | $0.30 – $1.00 | R-3.1 to R-3.8 |
Fiberglass Roll | $0.25 – $0.80 | R-3.1 to R-3.8 |
Cellulose | $0.50 – $1.50 | R-3.1 to R-3.8 (per inch, varies with density) |
Spray Foam (Open-cell) | $1.00 – $2.50 | R-3.6 to R-3.7 (per inch) |
Spray Foam (Closed-cell) | $2.00 – $4.00 | R-6.0 to R-7.0 (per inch) |
Rigid Foam Board (Polyisocyanurate) | $0.75 – $2.00 | R-6.0 to R-8.0 (per inch) |
Rigid Foam Board (Expanded Polystyrene) | $0.50 – $1.50 | R-4.0 to R-5.0 (per inch) |
Long-Term Cost-Effectiveness of Insulation Options
While higher initial costs are associated with certain insulation types, such as spray foam, the long-term energy savings can significantly offset these expenses. For example, a home with superior insulation might see a reduction in heating and cooling costs of 15-30% annually. This translates to considerable savings over the lifespan of the insulation, typically decades. Conversely, opting for cheaper, less efficient insulation may result in higher energy bills over time, negating any initial cost savings.
Cost Differences Between Bulk and Smaller Quantities
Purchasing insulation materials in bulk usually results in lower per-unit costs. Suppliers often offer discounts for larger orders. However, it’s crucial to accurately estimate your needs to avoid unnecessary expenses. Overestimating and purchasing excess materials leads to wasted resources and money. Conversely, underestimating your needs can cause project delays and necessitate additional purchases, potentially at a higher cost per unit due to smaller order sizes.
Regional Variations in Insulation Installation Costs
Geographic location significantly impacts the overall cost of insulation installation, influencing both labor and material expenses. Factors such as the availability of skilled labor, transportation costs for materials, local building codes, and even the climate itself contribute to these regional disparities. Understanding these variations is crucial for homeowners and contractors alike when budgeting for insulation projects.
Geographic Location’s Influence on Labor and Material Costs
Labor costs vary widely across different regions due to differences in the cost of living, demand for skilled labor, and prevailing wage rates. Areas with a high cost of living, such as major metropolitan areas on the coasts, typically have higher labor costs compared to more rural or less populated regions. Similarly, material costs are affected by transportation distances, import/export tariffs, and local supplier availability. For example, transporting insulation materials across long distances can significantly increase the overall cost, particularly for bulky materials. Regions with limited access to major suppliers may experience higher material costs as a result of increased transportation and potentially reduced competition.
Impact of Local Regulations and Building Codes on Installation Expenses
Local regulations and building codes play a significant role in determining insulation installation costs. Stricter codes often mandate higher R-values (a measure of thermal resistance) or specific types of insulation, leading to increased material costs. Furthermore, compliance requirements might necessitate additional labor, such as specialized inspections or the use of specific installation techniques, thereby increasing labor costs. For instance, areas prone to seismic activity might require specialized installation methods to ensure the insulation’s structural integrity, adding to the overall expense. Areas with stringent environmental regulations might also favor more expensive, eco-friendly insulation materials.
Comparison of Insulation Installation Costs Across Three Regions
To illustrate regional variations, let’s compare average installation costs for attic insulation (using fiberglass batts) in three distinct regions: the Northeast, the South, and the West. These figures are estimates based on averages gathered from various online resources and industry reports, and may vary depending on specific project details.
Let’s assume a 1,500 square foot home requiring attic insulation.
A hypothetical bar chart comparing average installation costs (per square foot) would look like this:
Northeast: $3.50/sq ft
South: $3.00/sq ft
West: $3.75/sq ft
This illustrates that the West, with potentially higher labor and material costs due to factors like transportation and higher cost of living in some areas, has the highest average cost. The South shows a lower average cost, possibly reflecting lower labor rates and potentially less stringent building codes in certain areas. The Northeast falls somewhere in between.
Note: These are illustrative examples, and actual costs will vary widely depending on factors such as the specific type of insulation used, the complexity of the installation, the contractor’s rates, and the specific location within each region.
Finding and Vetting Insulation Installers
Finding the right insulation installer is crucial for a successful and cost-effective project. A thorough vetting process ensures quality workmanship, fair pricing, and protects your investment. This involves several key steps to ensure you choose a reliable and competent professional.
Finding reputable insulation installers requires a multi-pronged approach. Begin by seeking recommendations from friends, family, or neighbors who have recently had insulation installed. Online resources such as review websites and contractor directories can also be valuable tools. Check for certifications from relevant organizations, indicating a commitment to professional standards and quality workmanship. Local building supply stores are another potential source of referrals. Remember to always verify any recommendations independently.
Comparing Contractor Quotes
Comparing quotes from multiple contractors is essential to ensure you receive a fair price. Simply comparing the total cost isn’t sufficient; a detailed analysis of the quote’s components is necessary. Look for clear itemization of materials, labor costs, and any additional charges. Inquire about the type and R-value of the insulation proposed, as this significantly impacts the overall effectiveness and cost. Confirm that all quotes are based on the same scope of work, to avoid comparing apples and oranges. For example, one contractor might use a more expensive, higher-performing insulation material than another, resulting in a higher price but potentially greater long-term energy savings.
License and Insurance Verification
Verifying the contractor’s license and insurance is a critical step in protecting yourself from potential liabilities. A valid license demonstrates compliance with local regulations and industry standards. Adequate insurance coverage, including workers’ compensation and liability insurance, safeguards you from financial responsibility in case of accidents or damages during the installation process. Contact your state’s licensing board or relevant regulatory authority to verify the contractor’s license status. Request proof of insurance from the contractor, ensuring the policy is current and covers the scope of the work. Failing to verify these aspects could leave you vulnerable to significant financial and legal risks.
Questions to Ask Potential Installers
Before committing to a contractor, a comprehensive checklist of questions will help ensure a smooth process. This should include inquiries about their experience with similar projects, their approach to safety and environmental considerations, their warranty offerings, and their payment terms. Request references from past clients and contact them to gather feedback on the contractor’s performance. Clarify the timeline for the project and the process for handling any unexpected issues or delays. Understanding their communication style and responsiveness is also crucial for a positive experience. For example, you might ask, “Can you provide examples of similar projects you’ve completed, and may I contact those clients for references?” This proactive approach minimizes the risk of unforeseen problems and ensures a satisfactory outcome.
DIY vs. Professional Insulation Installation
Choosing between DIY and professional insulation installation involves weighing cost savings against potential risks and the value of professional expertise. While a DIY approach might seem appealing for budget-conscious homeowners, professional installation offers significant advantages in terms of quality, efficiency, and long-term value. This section will analyze both options, highlighting their respective costs, benefits, and drawbacks.
Cost Comparison of DIY and Professional Insulation Installation
The cost difference between DIY and professional insulation installation can be substantial, depending on the size of the area to be insulated, the type of insulation used, and the complexity of the project. DIY projects generally require upfront material costs and potentially the rental or purchase of specialized tools. Professional installers, however, charge both for labor and materials, resulting in a higher overall expense. However, professionals often benefit from bulk purchasing discounts on materials, potentially mitigating some of the cost difference. The following table provides a general cost comparison; actual costs may vary significantly depending on location and project specifics.
Cost Factor | DIY Installation | Professional Installation |
---|---|---|
Materials | Variable, depending on insulation type and area; estimate $500 – $2000 | Included in labor cost; potentially higher due to bulk purchasing and potential waste reduction |
Labor | Your time (invaluable and variable) | $2000 – $6000 or more depending on project size and complexity |
Tools | Rental or purchase costs (e.g., $50-$200 for renting basic tools); potential for tool damage | Included in labor cost |
Waste Disposal | Your responsibility; potential additional costs | Typically included in labor cost |
Warranty | None | Typically offered by installer |
Potential Risks and Challenges of DIY Insulation Installation
Attempting DIY insulation installation carries several risks. Improper installation can lead to reduced energy efficiency, compromising the intended benefits. Incorrectly installed insulation can also create air leaks, potentially leading to moisture buildup, mold growth, and structural damage. Furthermore, working at heights or in confined spaces presents safety hazards. Lack of experience can result in wasted materials, inefficient installation, and ultimately, higher costs than initially anticipated. For example, improperly installed fiberglass insulation can cause skin irritation and respiratory problems if not handled correctly. Furthermore, certain types of insulation, such as spray foam, require specialized equipment and expertise for safe and effective application.
Tools and Materials Needed for DIY Insulation Installation
The tools and materials needed for DIY insulation installation vary depending on the type of insulation chosen. For fiberglass batts, you will need safety glasses, gloves, a utility knife, measuring tape, and potentially a staple gun. For spray foam, specialized equipment is required, including a spray gun and compressor, which are typically rented. Materials costs will depend on the area being insulated and the R-value of the chosen insulation. For example, a 100 sq ft area might require 10-15 rolls of fiberglass batts, costing between $100-$300 depending on the R-value. Spray foam insulation is generally more expensive per square foot than fiberglass batts. Accurate estimation of materials is crucial to avoid costly over- or under-purchases.
Energy Savings and Return on Investment
Investing in insulation offers significant long-term benefits beyond improved comfort. Proper insulation dramatically reduces energy consumption, leading to lower utility bills and a substantial return on your initial investment. This section explores the potential energy savings and provides a framework for calculating your return on investment.
Improved insulation minimizes the amount of energy required to heat your home in winter and cool it in summer. This is because insulation acts as a barrier, preventing heat from escaping in winter and entering in summer. The better the insulation, the less energy your heating and cooling systems need to work, resulting in lower energy bills and a smaller carbon footprint.
Energy Savings from Insulation Upgrades
The amount of energy saved depends on several factors, including the existing insulation level, the type and R-value of the new insulation, the size and climate of your home, and your energy consumption habits. Higher R-values indicate better insulation performance. For instance, upgrading from R-13 to R-30 wall insulation in a 2,000 square foot home in a climate with significant temperature swings could result in annual savings of several hundred dollars on heating and cooling costs. Similarly, improving attic insulation from R-19 to R-49 could yield even more substantial savings. These savings are cumulative; you will see the benefits year after year.
Return on Investment (ROI) Calculation
Calculating the ROI on insulation involves comparing the initial cost of installation against the cumulative energy savings over a specific period. A simple formula for calculating ROI is:
ROI = (Total Energy Savings – Total Installation Cost) / Total Installation Cost * 100%
For example, consider a homeowner who spends $5,000 on installing new insulation. Assume that the improved insulation results in annual energy savings of $500. Over a ten-year period, the total energy savings would be $5,000. Using the formula:
ROI = ($5,000 – $5,000) / $5,000 * 100% = 0%
In this scenario, the ROI is 0%, indicating that the homeowner recouped their initial investment over 10 years. However, if the annual savings were $750, the total savings over ten years would be $7,500. The ROI calculation would then be:
ROI = ($7,500 – $5,000) / $5,000 * 100% = 50%
This indicates a 50% return on investment over ten years. This is a simplified calculation; a more accurate calculation would consider factors like inflation and the potential increase in energy costs over time.
Examples of Potential Energy Savings
To illustrate potential energy savings, let’s consider two scenarios:
Scenario | Home Size (sq ft) | Existing Insulation R-Value | New Insulation R-Value | Estimated Annual Savings |
---|---|---|---|---|
Scenario 1: Attic Insulation Upgrade | 1500 | R-19 | R-49 | $300 – $600 |
Scenario 2: Wall Insulation Upgrade | 2000 | R-13 | R-21 | $200 – $400 |
*Note: These are estimated savings and actual savings may vary depending on several factors, including climate, energy prices, and home construction.*
Government Incentives and Rebates
Securing funding for home improvements, such as insulation installation, can significantly reduce the overall cost. Many government agencies at the federal, state, and local levels offer incentives and rebates designed to encourage energy efficiency upgrades. These programs can take the form of tax credits, direct rebates, or low-interest loans, making insulation projects more financially accessible.
Government incentives for insulation installation vary widely depending on location and specific program details. Eligibility criteria typically revolve around factors such as household income, the type of insulation used, and the energy savings achieved. The application process usually involves submitting documentation proving eligibility and project completion. It’s crucial to research the available programs in your specific area to determine eligibility and maximize potential savings.
Available Government Programs
Understanding the specific programs available in your region is vital to securing funding for your insulation project. Below is a table illustrating examples; however, it is not exhaustive and should be considered a starting point for your own research. Always verify current program details directly with the relevant government agency.
Program Name | Eligibility Criteria | Available Incentives |
---|---|---|
Federal Tax Credit for Energy Efficiency Improvements (Example) | Homeowners who install qualifying energy-efficient improvements, including insulation, may be eligible. Income limits may apply. Specific insulation types and installation requirements must be met. | A tax credit of up to a certain percentage of the cost of qualifying improvements. The exact percentage and maximum credit amount can vary from year to year. |
State Energy Efficiency Program (Example – California) | Homeowners and renters in California may qualify based on income levels and the type of insulation installed. Programs often prioritize low-income households. | Rebates, direct payments, or low-interest loans to offset the cost of insulation installation. Specific amounts vary depending on the program and the project. |
Local Utility Company Rebates (Example – A hypothetical utility company) | Customers of the utility company who install insulation that meets specific energy-efficiency standards may be eligible. May require proof of installation and energy savings. | Rebates directly from the utility company, often based on the amount of energy saved. The rebate amount varies based on the type and amount of insulation installed. |
Impact of Home Size and Insulation Type on Costs
The cost of insulation installation is significantly influenced by both the size of the home and the type of insulation chosen. Larger homes naturally require more insulation material, leading to higher material costs. Simultaneously, the labor involved in installing insulation across a larger area increases the overall labor expense. The type of insulation selected also plays a crucial role, as different materials vary widely in price and the level of expertise required for proper installation.
The square footage of a home directly correlates with the amount of insulation needed. A larger home, say 3000 square feet, will require considerably more insulation than a smaller home of 1000 square feet. This increased volume directly translates into a higher material cost. Furthermore, the labor involved in covering a larger area will take longer, thus increasing the labor component of the overall cost. This is especially true for areas that are difficult to access, such as attics or crawl spaces, where the additional time and effort required to install insulation significantly increase labor costs.
Material and Labor Costs for Different Insulation Types
Different insulation types have varying material costs and labor requirements. Fiberglass batts, a common and relatively inexpensive option, are generally easier to install than spray foam insulation, which requires specialized equipment and expertise. Spray foam, while more expensive upfront, often requires less labor due to its seamless application and superior air sealing capabilities, potentially offsetting some of the initial higher material cost in the long run due to reduced energy consumption. Cellulose insulation, made from recycled paper, offers a balance between cost and performance, falling somewhere between fiberglass and spray foam in both material and labor costs.
Cost Examples Based on Home Size and Insulation Choices
Consider two homes: a 1500 square foot ranch and a 3000 square foot two-story. If fiberglass batts are chosen for both, the larger home will require approximately double the amount of material, resulting in roughly double the material cost. However, the labor cost increase will likely be less than double due to economies of scale; the installer can often work more efficiently on a larger project. If spray foam insulation were chosen instead, the difference in material cost between the two homes would be even more pronounced, potentially exceeding a simple doubling due to the bulk nature of the material and the increased complexity of the installation for a larger home. The labor cost would still be significantly higher for the larger home, but again, the rate of increase might not be directly proportional to the increase in square footage.
Estimated Costs for Various Home Sizes and Insulation Types, How much is it to install insulation
Home Size (sq ft) | Fiberglass Batts (Estimate) | Cellulose Insulation (Estimate) | Spray Foam Insulation (Estimate) |
---|---|---|---|
1000 | $1500 – $2500 | $2000 – $3500 | $4000 – $7000 |
1500 | $2250 – $3750 | $3000 – $5250 | $6000 – $10500 |
2000 | $3000 – $5000 | $4000 – $7000 | $8000 – $14000 |
3000 | $4500 – $7500 | $6000 – $10500 | $12000 – $21000 |
*Note: These are estimates and actual costs can vary based on several factors including regional pricing, accessibility of installation areas, and specific installer pricing.*
Common Mistakes to Avoid When Getting Insulation Installed
Proper planning and execution are crucial for a successful insulation installation project. Failing to address key aspects can lead to wasted money, ineffective insulation, and even structural damage. Understanding common pitfalls and taking preventative measures will ensure a worthwhile investment that delivers long-term energy savings.
Insufficient Planning and Budgeting
Thorough planning prevents costly oversights. Many homeowners underestimate the total cost, failing to account for factors beyond material and labor, such as demolition, waste disposal, and potential structural modifications needed to accommodate insulation. This can lead to budget overruns and project delays. For instance, neglecting to factor in the cost of removing existing insulation before installing new material can significantly increase the overall expense. Accurate budgeting requires obtaining multiple quotes from reputable installers and carefully reviewing the scope of work detailed in each proposal.
Ignoring Existing Insulation Conditions
Ignoring the condition of existing insulation is a frequent mistake. Old, damaged, or inadequate insulation may require removal before new insulation can be effectively installed. Failing to address this can lead to poor thermal performance, rendering the new insulation less effective and negating potential energy savings. For example, if damp or moldy insulation is left in place, it can create health hazards and further compromise the new installation. A thorough inspection of existing insulation is essential before starting any new installation.
Choosing the Wrong Type of Insulation
Selecting the appropriate insulation type is critical for optimal performance and cost-effectiveness. Different insulation materials have varying R-values (resistance to heat flow), thermal properties, and suitability for different applications. Choosing the wrong type for your climate, building structure, or specific area (walls, attic, crawlspace) can result in ineffective insulation and wasted resources. For example, using fiberglass batt insulation in a damp crawlspace is inappropriate, as it can absorb moisture and lose its insulating properties. Consulting with a qualified insulation professional can help determine the most suitable type for your needs.
Neglecting Air Sealing
Air sealing is just as important as insulation itself. Air leaks allow conditioned air to escape, negating the benefits of even the best insulation. Failing to adequately seal air gaps and cracks before installing insulation significantly reduces its effectiveness and increases energy costs. Common air leakage points include gaps around windows, doors, and electrical outlets. A comprehensive air sealing strategy should be implemented before insulation installation.
Failing to Hire a Qualified Installer
Hiring an unqualified or inexperienced installer can lead to poor workmanship, inadequate insulation, and potentially costly repairs. Unlicensed installers may not follow building codes or use appropriate safety measures, resulting in structural damage, fire hazards, or health risks. Choosing a reputable installer with verifiable credentials, positive reviews, and insurance is crucial to ensure a quality installation. Checking online reviews and obtaining references can help verify the installer’s competence.
Underestimating the Importance of Proper Installation
Improper installation techniques can severely compromise the effectiveness of insulation. Issues such as insufficient packing density, gaps in insulation, or improper vapor barrier installation can all lead to reduced thermal performance and increased energy costs. A qualified installer understands the importance of proper installation techniques and will ensure the insulation is installed correctly to maximize its effectiveness. This may include using appropriate tools and techniques to ensure proper density and continuity.
- Mistake: Insufficient planning and budgeting. Consequence: Budget overruns and project delays.
- Mistake: Ignoring existing insulation conditions. Consequence: Poor thermal performance and health hazards.
- Mistake: Choosing the wrong type of insulation. Consequence: Ineffective insulation and wasted resources.
- Mistake: Neglecting air sealing. Consequence: Reduced insulation effectiveness and increased energy costs.
- Mistake: Failing to hire a qualified installer. Consequence: Poor workmanship, structural damage, and safety hazards.
- Mistake: Underestimating the importance of proper installation. Consequence: Reduced thermal performance and increased energy costs.
Clarifying Questions
What is the R-value, and why is it important?
R-value measures the thermal resistance of insulation; higher R-values indicate better insulation and lower energy bills.
Can I get tax credits or rebates for insulation installation?
Yes, many government programs offer tax credits or rebates for energy-efficient home improvements, including insulation. Check with your local or state energy office for details.
How long does insulation installation typically take?
The time required varies greatly depending on the size of your home, the type of insulation, and the accessibility of the areas needing insulation. It can range from a few hours to several days.
What is the warranty on insulation materials?
Warranties vary by manufacturer and type of insulation. Check the manufacturer’s specifications for details.