Average Costs
The cost of a new asphalt shingle roof varies significantly depending on several factors. Understanding these factors will help you budget effectively for your roofing project. This section will provide a range of average costs based on common scenarios, highlighting the key influences on the final price.
New asphalt roof cost – Several key factors contribute to the variability in asphalt roof costs. The size of your roof is a primary determinant, with larger roofs naturally requiring more materials and labor. Geographical location also plays a crucial role, as material costs and labor rates fluctuate regionally. The quality of the materials chosen, from the shingles themselves to underlayment and flashing, significantly impacts the overall expense. Finally, the complexity of the roof—including its pitch, shape, and the presence of dormers or valleys—can increase labor costs and, consequently, the total project cost.
Average Costs by Roof Size and Region
The table below presents estimated average costs for new asphalt shingle roofs in different regions of the United States, categorized by roof size. These figures are estimates and should be considered as a starting point for your budgeting. Actual costs may vary based on the factors discussed above and local market conditions.
Region | Small Roof (under 1000 sq ft) | Medium Roof (1000-2000 sq ft) | Large Roof (over 2000 sq ft) |
---|---|---|---|
Northeast | $5,000 – $8,000 | $10,000 – $16,000 | $15,000 – $25,000 |
South | $4,000 – $7,000 | $8,000 – $14,000 | $12,000 – $20,000 |
Midwest | $4,500 – $7,500 | $9,000 – $15,000 | $13,500 – $22,500 |
Material Costs
The cost of materials significantly impacts the overall price of a new asphalt roof. Understanding the various types of asphalt shingles available, their price points, and the warranties offered by different manufacturers is crucial for making an informed decision. This section will detail the cost breakdown of common asphalt shingle types and compare pricing from various manufacturers.
Asphalt shingle costs vary based on several factors, including the type of shingle, the manufacturer, and the quantity needed. Generally, the more durable and aesthetically pleasing the shingle, the higher the cost. Warranties also play a significant role; longer warranties typically correlate with higher initial material costs, reflecting the manufacturer’s confidence in the product’s longevity.
Asphalt Shingle Types and Costs
Three-tab shingles are the most economical option, known for their simple, flat design and relatively low cost per square. Architectural shingles, also known as dimensional shingles, offer a more textured, upscale appearance and generally boast improved durability and longevity compared to 3-tab shingles. They achieve this enhanced performance through a thicker profile and more complex layering. Luxury shingles represent the top tier, often featuring thicker profiles, enhanced weathering resistance, and sophisticated designs. These premium options command a significantly higher price but often come with extended warranties.
Manufacturer Comparison and Warranties, New asphalt roof cost
Several major manufacturers dominate the asphalt shingle market, each offering various shingle lines with varying prices and warranty lengths. For example, Owens Corning, GAF, and CertainTeed are well-known brands that consistently receive high ratings for quality and customer service. Direct price comparisons between manufacturers can fluctuate depending on regional availability and current market conditions. However, it’s generally true that premium shingle lines from reputable manufacturers will cost more upfront but often come with longer warranties (25-50 years or more), potentially offering long-term cost savings by reducing the likelihood of premature replacement. It’s essential to compare not just the initial cost but also the total cost of ownership, considering the potential for repairs or early replacement under shorter warranties.
Shingle Type Comparison Table
The following table provides a general comparison of three common shingle types: 3-Tab, Architectural, and Luxury. Note that prices are estimates and can vary based on location, supplier, and specific product features. Warranties can also be affected by proper installation and adherence to manufacturer guidelines.
Shingle Type | Lifespan (Years) | Cost per Square ($) | Warranty Length (Years) |
---|---|---|---|
3-Tab | 15-20 | 60-100 | 10-20 |
Architectural | 25-30 | 120-200 | 25-30 |
Luxury | 30-50 | 200-350 | 30-50 |
Labor Costs
Labor costs represent a significant portion of the overall expense for a new asphalt roof installation. Understanding these costs is crucial for budgeting and comparing different contractors. Several factors influence the final labor price, making it essential to carefully consider these variables before making a decision.
Factors Affecting Labor Costs
Geographic Location
Labor rates vary significantly depending on geographic location. Areas with a higher cost of living, a stronger union presence, or a higher demand for skilled labor will generally have higher roofing labor costs. For example, a roofing crew in a major metropolitan area like New York City will likely charge more per hour or per square foot than a similar crew in a smaller town in the Midwest. This difference reflects the varying economic conditions and competitive landscapes of different regions.
Contractor Experience and Skill
The experience and skill level of the roofing contractor directly impact labor costs. Highly experienced and reputable contractors with a proven track record often command higher rates due to their expertise, efficiency, and the lower risk of errors or delays. A less experienced contractor may offer lower rates, but this could potentially lead to longer project timelines, higher material waste, or even subpar workmanship requiring costly repairs down the line. The value of experience should be weighed against the immediate cost savings offered by less experienced crews.
Hourly Rates and Per-Square-Foot Pricing
Contractors typically charge either an hourly rate or a price per square foot for their labor. Hourly rates can range from $40 to $80 or more per hour per worker, depending on the factors mentioned above. Per-square-foot pricing often falls between $1.50 and $5.00, again varying greatly by location and contractor experience. It’s important to obtain detailed breakdowns of labor costs from multiple contractors to compare apples to apples. A detailed quote should specify the number of workers, the estimated hours of labor, and the total labor cost.
Comparison: Single Contractor vs. Larger Roofing Company
Choosing between a single contractor and a larger roofing company involves considering several trade-offs. Smaller contractors may offer more personalized service and potentially more competitive pricing due to lower overhead. However, larger companies often have greater resources, more established insurance coverage, and potentially better access to materials and equipment. Larger companies might have slightly higher labor costs, but this could be offset by potential efficiencies and reduced risk of project delays. Ultimately, the best choice depends on individual priorities and the specific circumstances of the project. Comparing detailed quotes from both types of contractors is crucial for informed decision-making.
Permitting and Inspections
Obtaining the necessary permits and inspections for a new asphalt roof is a crucial step in the roofing process, impacting both the legality and the overall timeline of your project. These requirements vary significantly depending on your location and the specifics of your roof, influencing the associated costs and potential delays. Understanding this process beforehand can help you budget accurately and manage expectations effectively.
Permitting and inspection costs typically involve application fees, plan review fees, and inspection fees. The application fee covers the administrative cost of processing your permit request. Plan review fees cover the cost of having a building official review your project plans to ensure they comply with building codes. Inspection fees are charged for each visit by a building inspector to verify that the work is being performed according to code. These fees vary widely by jurisdiction, ranging from a few hundred dollars to potentially over a thousand dollars depending on the complexity of the project and the local regulations.
Permit Acquisition Process and Potential Delays
The process of obtaining building permits generally involves submitting a complete application, including detailed plans and specifications for the new roof. This application is then reviewed by the local building department to ensure compliance with building codes and regulations. Once approved, the permit is issued, and inspections are scheduled at various stages of the project, such as during the tear-off, installation of underlayment, and final completion. Delays can occur at any stage of this process, most commonly due to incomplete applications, plan revisions needed to meet code, or scheduling conflicts with building inspectors. In some areas, permitting processes can take several weeks, while in others, it might take only a few days. Unexpected delays can significantly impact the overall project timeline and increase overall costs due to project standstill.
Factors Influencing Permitting Costs
Several factors can influence the cost of obtaining permits and inspections. For instance, larger, more complex roofing projects requiring extensive structural modifications may necessitate more extensive plan reviews and more frequent inspections, thereby increasing the associated fees. Conversely, smaller, simpler projects with minimal changes might incur lower costs. The location of the property also plays a significant role; areas with stricter building codes or higher administrative costs tend to have higher permitting fees. For example, a historical district might require more rigorous plan reviews and inspections, leading to significantly higher costs than a typical residential area. Furthermore, expedited permit processing, sometimes available for an additional fee, can reduce delays but comes at an increased cost.
Underlayment and Accessories: New Asphalt Roof Cost
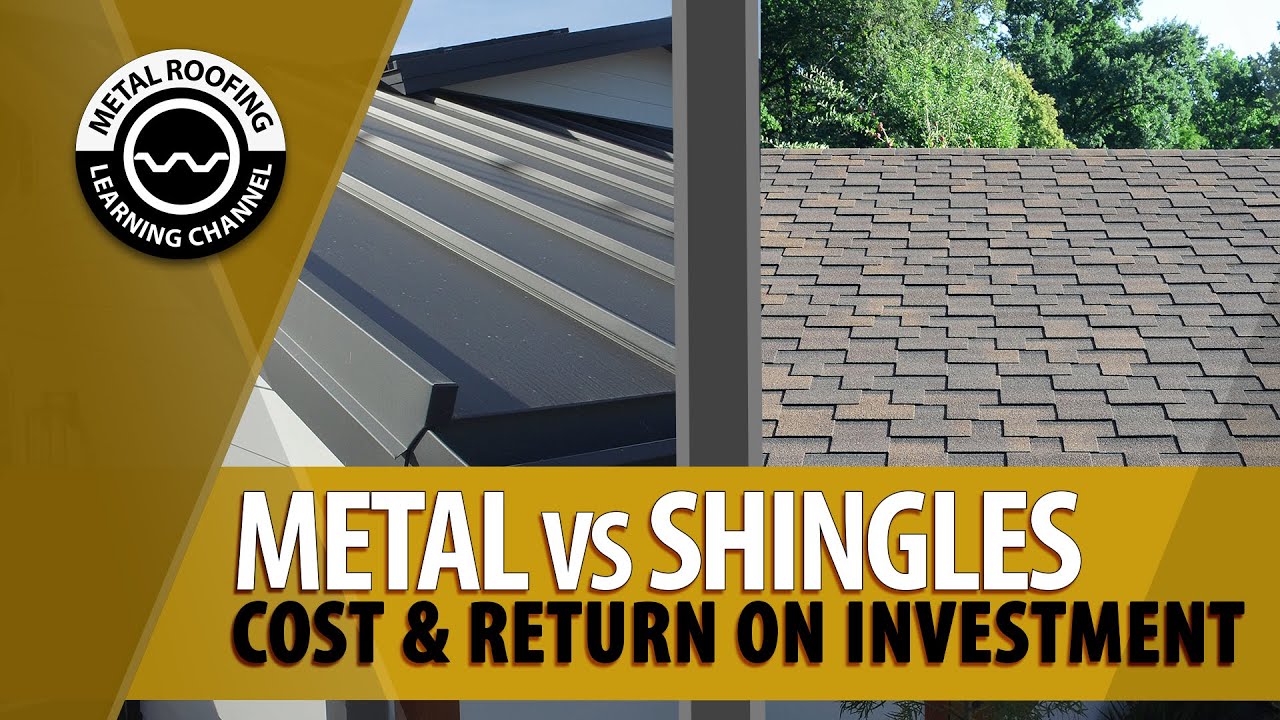
Choosing the right underlayment and accessories is crucial for a long-lasting and leak-proof asphalt shingle roof. These components provide an extra layer of protection and enhance the overall performance of your roofing system. While they might seem like minor expenses, neglecting them can lead to significant problems down the line, ultimately increasing your overall roofing costs.
Underlayment Types and Costs
Different types of underlayment offer varying degrees of protection and price points. Felt underlayment, a traditional option, is relatively inexpensive but less durable and offers less protection against moisture compared to synthetic alternatives. Synthetic underlayments, such as polyethylene or polypropylene, are more expensive upfront but provide superior water resistance, tear strength, and longevity. They often come with warranties that can extend the lifespan of your roof. The cost difference can be significant; expect to pay approximately $0.25 to $0.75 per square foot for felt underlayment, while synthetic underlayments can range from $0.50 to $1.50 per square foot or more, depending on the specific product and its features. The increased upfront cost of synthetic underlayment is often offset by its extended lifespan and reduced risk of future repairs.
Roof Vent Costs
Proper ventilation is essential for preventing moisture buildup within the attic space, which can lead to mold growth, structural damage, and premature roof failure. Roof vents, including ridge vents, gable vents, and turbine vents, are critical components of a well-ventilated roofing system. The cost of these vents varies depending on the type, size, and material. For example, a ridge vent might cost between $1 and $5 per linear foot, while gable vents could range from $20 to $100 per unit, and turbine vents can cost anywhere from $50 to $200 or more each. The total cost will depend on the number and type of vents needed for your specific roof. Larger roofs will naturally require more vents and therefore incur higher costs.
Flashing and Other Accessory Costs
Flashing, which is typically made of metal, is essential for sealing vulnerable areas of the roof where water can penetrate, such as around chimneys, vents, and valleys. Proper flashing installation is critical to prevent leaks. The cost of flashing varies depending on the material (e.g., aluminum, copper, galvanized steel) and the complexity of the installation. Other accessories, such as drip edges, ice and water shields, and starter shingles, also contribute to the overall roofing cost. These accessories protect the roof from water damage and improve the overall performance and longevity of the roofing system.
Common Roof Accessories and Approximate Costs
The following bullet points list common roof accessories and their approximate costs. Remember that these are estimates and actual costs can vary based on factors like location, material selection, and the complexity of the installation.
- Ice and Water Shield: $0.50 to $2.00 per square foot
- Drip Edge: $0.25 to $1.00 per linear foot
- Starter Shingles: $0.50 to $2.00 per square foot (included in many shingle packages)
- Flashing (aluminum): $1.00 to $5.00 per linear foot
- Flashing (copper): $5.00 to $20.00 per linear foot
- Chimney Flashing: $100 to $500 or more, depending on complexity
- Vent Flashing: $20 to $100 per vent
Tear-Off Costs
Removing your old roof before installing a new asphalt shingle roof is a crucial step that significantly impacts the overall project cost. Tear-off involves the complete removal of existing roofing materials, including shingles, underlayment, and potentially flashing, and proper disposal of the waste. The cost of this process varies considerably depending on several factors.
The primary factors determining tear-off costs are the complexity of the roof and the associated waste disposal. A simple, low-slope roof with easily accessible areas will naturally have a lower tear-off cost compared to a complex, multi-level roof with numerous valleys, dormers, and chimneys. The amount of waste generated also plays a critical role; larger roofs with more layers of roofing materials will produce more waste, leading to higher disposal fees. Accessibility also plays a significant role. Steep slopes or difficult-to-reach areas may require specialized equipment and more labor, increasing costs. Finally, local regulations concerning waste disposal and landfill fees can vary considerably from region to region, impacting the final cost.
Factors Influencing Tear-Off Costs
Several factors interact to determine the final tear-off cost. For example, a large, complex roof on a sprawling Victorian-style home with multiple layers of shingles, requiring specialized equipment and extra labor to navigate intricate valleys and dormers, will have a significantly higher tear-off cost than a small, single-story ranch house with a simple gable roof and only one layer of shingles. Similarly, the presence of asbestos or other hazardous materials in the old roofing system will add considerably to the cost due to the specialized handling and disposal required, often necessitating the involvement of licensed abatement professionals. Conversely, a small, flat roof with readily accessible areas and only one layer of relatively lightweight shingles will result in a lower tear-off cost.
Examples of Tear-Off Cost Variations
Consider two scenarios: a 1,500 square foot ranch home with a simple gable roof and a 3,000 square foot two-story colonial home with multiple dormers and valleys. The tear-off for the ranch home might cost between $1,500 and $3,000, while the tear-off for the colonial home could range from $4,000 to $8,000 or even more, due to increased labor and waste disposal requirements. This difference highlights the significant impact of roof complexity on tear-off costs. Another example would be the difference in cost between a roof with only one layer of shingles versus a roof with multiple layers of shingles, which increases the amount of waste and labor involved.
Typical Tear-Off Cost Range
The typical cost range for tear-off services varies widely depending on location, roof size, complexity, and the presence of hazardous materials. However, a reasonable estimate for a typical asphalt shingle roof tear-off might fall within the range of $1.50 to $5.00 per square foot. This broad range reflects the substantial variability inherent in roofing projects. It is crucial to obtain multiple quotes from reputable roofing contractors to get an accurate estimate for your specific project.
Warranty Information
Understanding the warranty associated with your new asphalt roof is crucial for protecting your investment. Warranties offer varying levels of protection against defects in materials and workmanship, but it’s essential to know the specifics to avoid unexpected costs down the line. This section will clarify the typical warranty periods and coverage you can expect.
Asphalt shingle and roofing installation warranties typically cover a range of issues, from manufacturing defects in the shingles themselves to problems with the installer’s workmanship. The length and breadth of coverage can vary significantly depending on the manufacturer, installer, and specific warranty type. It’s vital to carefully review all warranty documents before making a final decision.
Warranty Periods
Manufacturers typically offer warranties on their asphalt shingles ranging from 20 to 50 years. These warranties often cover defects in materials, such as granule loss, cracking, or curling, but they usually don’t cover damage caused by external factors like hail, wind, or fire. Installation warranties provided by roofing contractors typically cover workmanship for a shorter period, often 1 to 5 years. This covers issues resulting from improper installation, such as leaks or premature shingle failure due to installation errors. A reputable contractor will provide a clear and detailed written warranty outlining the specifics of their coverage. For example, a manufacturer might offer a 30-year warranty on the shingles themselves, while the contractor offers a 2-year warranty on their installation work.
Types of Warranties
Several types of warranties exist for asphalt roofing, each with its own terms and conditions. A common type is the manufacturer’s limited warranty, which typically covers defects in materials under specific conditions. Another type is the workmanship warranty offered by the roofing contractor, covering issues related to the quality of their installation. Some manufacturers also offer enhanced warranties for an additional fee, which might extend coverage or include additional benefits. For instance, a “full” or “comprehensive” warranty may cover a wider range of issues compared to a “limited” warranty. It is important to understand the differences to fully appreciate the level of protection each offers.
Warranty Limitations and Exclusions
It is imperative to understand that all warranties have limitations and exclusions. Common exclusions include damage caused by acts of nature (e.g., hurricanes, tornadoes), normal wear and tear, improper maintenance, or vandalism. Many warranties also require the homeowner to meet specific conditions, such as regular roof maintenance or prompt reporting of defects, to maintain coverage. For example, a warranty might be voided if the homeowner fails to remove debris from the roof regularly, leading to premature shingle damage. Carefully reading the fine print and understanding these limitations is crucial to avoid disputes later.
Payment Options
Choosing the right payment method for your new asphalt roof is a crucial step in the process. The best option will depend on your financial situation, relationship with the contractor, and the overall project cost. Understanding the advantages and disadvantages of each method will help you make an informed decision and ensure a smooth payment process.
Payment methods typically offered for roofing projects fall into three main categories: upfront payment, installment payments, and financing. Each option presents unique benefits and drawbacks.
Upfront Payment
Paying the entire cost of the roofing project upfront is often preferred by contractors. This provides them with immediate access to funds, allowing them to purchase materials and schedule labor without delay. For the homeowner, this method can sometimes result in a discount or other favorable terms negotiated with the contractor. However, it requires a significant upfront capital investment which may not be feasible for all homeowners. The major disadvantage is the potential financial strain of a large, one-time expense.
Installment Payments
Installment payments involve breaking down the total cost into smaller, manageable payments made over a specified period. This can alleviate the financial burden of a large upfront payment. A typical structure might involve a down payment upon signing the contract, followed by subsequent payments at predetermined intervals (e.g., monthly or bi-weekly) as the project progresses. However, contractors may require a larger down payment for installment plans to mitigate risk. Late payments can result in penalties or project delays.
Financing Options
Many contractors offer financing options through partnerships with lenders. This allows homeowners to spread the cost of the roof over several months or even years, with interest applied to the loan. Financing can make a new roof more affordable, especially for larger projects. However, it is crucial to carefully review the terms and interest rates before committing to a financing plan, as interest charges can significantly increase the overall cost. Credit checks are usually required, and approval is not guaranteed.
Negotiating Payment Terms
Negotiating payment terms with contractors is common practice. Homeowners can explore options like adjusting the down payment percentage, extending the payment schedule, or requesting a detailed breakdown of costs to better understand where their money is being allocated. Transparency and open communication are key to reaching an agreement that works for both parties. It’s advisable to have a written contract clearly outlining all payment terms, including due dates, amounts, and penalties for late payments. Consider seeking professional advice from a financial advisor if you’re unsure about managing the financial aspects of a large project.
Finding Reputable Contractors
Choosing the right roofing contractor is crucial for a successful and long-lasting asphalt roof installation. A poorly chosen contractor can lead to costly repairs, substandard work, and significant headaches. Taking the time to thoroughly vet potential contractors will protect your investment and ensure peace of mind.
Finding a qualified and reputable roofing contractor involves a multi-step process that goes beyond simply checking online reviews. It requires diligent research, careful questioning, and a keen eye for detail. By following these steps, you can significantly reduce the risk of encountering unscrupulous contractors and ensure a smooth, professional installation.
Contractor Licensing and Insurance Verification
Confirming a contractor’s licensing and insurance is paramount. Licensed contractors have demonstrated competency and adherence to industry standards, while insurance protects you from liability in case of accidents or damages during the project. You should request proof of both general liability and workers’ compensation insurance. Contact your state’s licensing board to verify the validity and status of their license, ensuring it’s current and in good standing. This step helps eliminate unqualified or unlicensed contractors who may cut corners or lack the necessary expertise.
Experience and References
Inquire about the contractor’s experience with asphalt roofing installations, specifically the type of roofing material you’ve selected. Ask for a list of references, including recent projects similar in scope to yours. Contact these references to discuss their experiences, the quality of the work, and the contractor’s professionalism and responsiveness. Look for a consistent pattern of positive feedback, paying attention to details like adherence to timelines and effective communication. Established contractors often have a portfolio of completed projects that they are happy to share, allowing you to visually assess the quality of their work.
Detailed Estimates and Contracts
A reputable contractor will provide a detailed, itemized estimate outlining all costs associated with the project. This should include materials, labor, permits, and any additional services. Compare estimates from multiple contractors to ensure you are receiving competitive pricing. Before signing a contract, carefully review all terms and conditions, ensuring that everything is clearly defined and understood. The contract should specify project timelines, payment schedules, and warranty information. A vague or incomplete contract should raise red flags. A well-written contract protects both the homeowner and the contractor.
Questions to Ask Potential Contractors
Asking specific questions helps assess a contractor’s qualifications and professionalism. For example, you should inquire about their experience with specific roofing materials, their approach to dealing with unexpected issues, and their process for managing the project timeline. Understanding their safety protocols and waste disposal practices is equally important. Inquiring about their approach to dealing with potential problems or delays demonstrates their preparedness and problem-solving abilities. The contractor’s responses should be clear, concise, and demonstrate a thorough understanding of the roofing process.
Avoiding Roofing Scams
Be wary of contractors who pressure you into making quick decisions, offer unusually low prices, or request full payment upfront. Legitimate contractors typically require a deposit, but not the full amount before the work begins. Always get multiple estimates and compare prices before making a decision. Thoroughly researching a contractor’s reputation through online reviews and checking with the Better Business Bureau can help avoid scams. Trust your instincts – if something feels wrong, it probably is. A reputable contractor will be transparent, professional, and willing to answer your questions thoroughly.
Factors Affecting Overall Cost
Several factors beyond basic material and labor costs significantly influence the final price of a new asphalt shingle roof. Understanding these variables allows homeowners to better budget for their project and make informed decisions during the planning process. These factors often interact, creating a complex interplay that determines the overall expense.
Roof Complexity
The complexity of a roof directly impacts the time and materials required for installation. Roofs with multiple levels, dormers, valleys, hips, and ridges present greater challenges for contractors. These features necessitate more precise measurements, intricate cuts, and specialized techniques, leading to increased labor costs. For example, a simple gable roof on a single-story house will be considerably cheaper to reshingle than a complex mansard roof on a multi-story home with numerous dormers and chimneys. The additional time spent navigating these complexities translates to a higher overall cost. Considerable extra care must be taken to ensure proper water sealing around these features.
Roof Pitch and Size
The steepness (pitch) and size of the roof are also key cost drivers. Steeper roofs are more dangerous and time-consuming to work on, requiring specialized safety equipment and more cautious work practices. This translates to higher labor costs. Larger roofs, naturally, require more materials and more labor hours, resulting in a higher overall price. A simple calculation isn’t sufficient; the angle of the pitch affects the amount of material needed to cover the actual surface area of the roof, impacting the total material costs. A larger surface area, regardless of pitch, will naturally require more shingles.
Geographic Location
Geographic location influences both material and labor costs in several ways. The availability of local materials and the cost of transportation can affect material pricing. Areas with limited access to asphalt shingle suppliers may experience higher material costs due to transportation fees. Labor costs also vary significantly depending on the local market. Highly populated areas with a high demand for skilled labor, such as major metropolitan areas, tend to have higher labor rates compared to rural areas with a lower demand. Furthermore, regional differences in building codes and permitting fees can add to the overall cost. For example, a roof installation in a coastal region might necessitate the use of more expensive, weather-resistant materials, leading to a higher project cost compared to an inland location.
Budgeting and Planning
Replacing your roof is a significant investment, so careful budgeting and planning are crucial to ensure a smooth and financially manageable process. This section Artikels a step-by-step guide to budgeting for a new asphalt roof, strategies for managing unexpected costs and delays, and techniques for prioritizing expenses to stay within your financial limits.
Developing a Realistic Budget
Creating a realistic budget involves several key steps. First, obtain multiple detailed estimates from reputable roofing contractors. These estimates should itemize all costs, including materials, labor, permits, and any potential tear-off expenses. Comparing these estimates will give you a clear understanding of the price range for your project. Next, factor in a contingency fund. Unexpected issues, such as hidden damage or material price fluctuations, can arise. Allocating 10-20% of the total estimated cost as a contingency buffer is a prudent measure. Finally, consider your payment options. Many contractors offer financing plans, while others require upfront payments or staged payments throughout the project. Understanding your payment capabilities will inform your overall budgeting process. For example, a homeowner budgeting $15,000 for a new roof should add a contingency of $1,500-$3,000, resulting in a total budget of $16,500-$18,000.
Managing Unexpected Costs and Potential Delays
Unforeseen circumstances can significantly impact a roofing project. For instance, discovering extensive underlying damage during the tear-off process could lead to unexpected repair costs. Similarly, inclement weather can cause delays, potentially impacting labor costs and project timelines. To mitigate these risks, securing a detailed contract that clearly Artikels all aspects of the project is essential. This contract should include clauses addressing potential unforeseen issues and their associated cost implications. Furthermore, maintaining open communication with your contractor is vital. Regular updates on the project’s progress can help identify potential problems early on, allowing for timely adjustments to the budget and schedule. A real-life example would be a homeowner encountering unexpected rot in the decking requiring additional replacement costs, adding $2,000 to the initial $15,000 budget.
Prioritizing Expenses and Staying Within Budget
Prioritizing expenses effectively involves focusing on essential aspects of the roofing project while considering cost-saving measures where possible. For instance, while high-quality materials are important for longevity, exploring different material options can help you find a balance between durability and cost. Similarly, while a tear-off may seem an added expense, neglecting a proper tear-off could lead to future problems and higher long-term costs. Careful consideration of the warranty offered on materials and workmanship is crucial. A longer warranty, while potentially more expensive upfront, can provide significant long-term cost savings by minimizing the risk of costly repairs down the line. A homeowner aiming for a cost-effective solution might opt for a slightly less expensive asphalt shingle while prioritizing a robust underlayment for enhanced protection and a longer-lasting roof.
FAQ Summary
What is the lifespan of an asphalt shingle roof?
The lifespan of an asphalt shingle roof varies depending on the shingle quality, climate, and proper installation, typically ranging from 15 to 30 years.
Can I finance a new asphalt roof?
Yes, many contractors offer financing options or you can explore home improvement loans through banks or credit unions.
How do I choose a reputable roofing contractor?
Check online reviews, verify licenses and insurance, obtain multiple bids, and ask for references before selecting a contractor.
What is included in a roofing warranty?
Warranties typically cover defects in materials and workmanship, but specific terms vary by manufacturer and contractor. Carefully review the warranty details.